固体推进剂火箭发动机
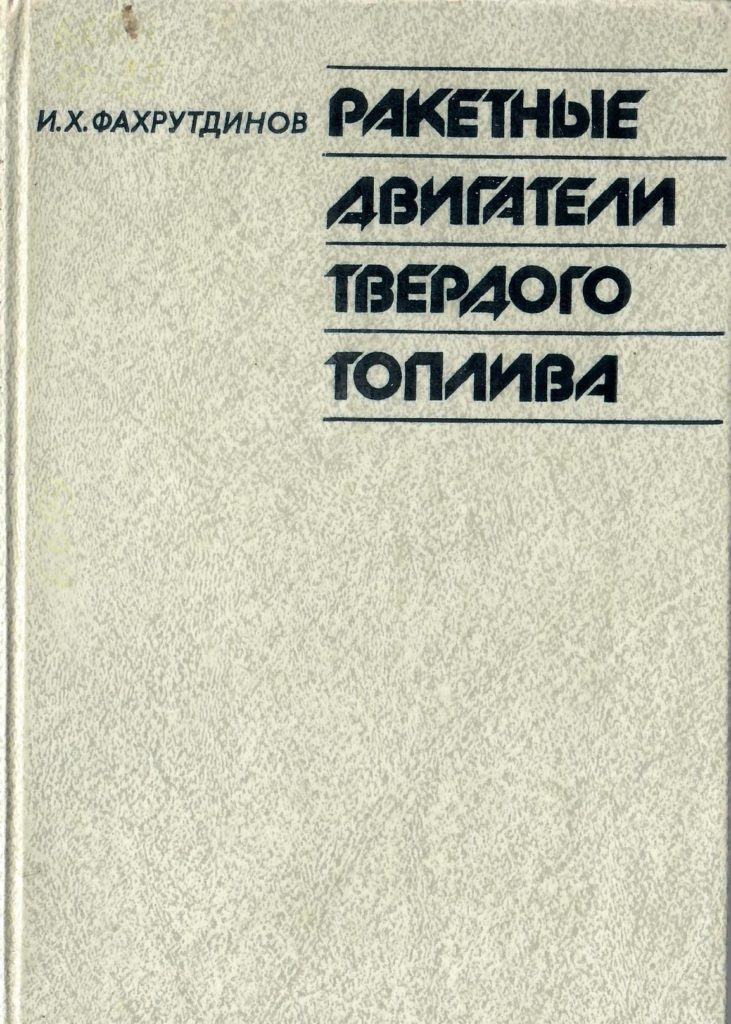
作者: И.Х.法赫鲁特季诺夫
本书从发动机研制的初步技术任务书编制,到批产所有研制阶段,一系列相互联系问题, 填补了SRM研制工作中的空白。从方法学上,依次阐述了能反映SRM研制所有阶段的资料,即:研制技术任务书的编制、内弹道学特性和推力特性的计算、初步结构方案的设计、载荷分析、结构材料选择、结构件的设计及其强度计算、工艺性保障、改进性试验研制和结构状态的预测、 SRM自动化设计 。本书以工程应用为着力点,给出解决问题的思路 。
本书比较经典,在很多方面仍有较大参考价值,是国内教材不曾涉及的。
目录
第一章:固体火箭发动机概述
1.1、发动机的结构
1.2、固体火箭发动机发展和应用史
1.3、固体火箭发动机分类
1.4、固体火箭发动机的研制阶段和组织
1.5、固体火箭发动机研制技术任务书
1.6、火箭和固体火箭发动机特性的相互关系
第二章:固体推进剂装药,固体火箭发动机的性能和结构型式
2.1、对推进剂装药的要求
2.2、固体火箭推进剂
2.3、固体火箭推进剂装药
2.4、固体火箭推进剂装药几何参数的计算
2.5、固体火箭发动机内弹道参数的计算
2.6、作用于固体火箭发动机的载荷分类
2.7、固体火箭发动机初步结构方案的制定
第三章:承载结构的结构材料选择
3.1、金属
3.2、纤维复合材料
第四章:固体火箭发动机结构件的计算和设计
4.1、金属结构件的计算和设计
4.2、纤维复合材料结构件的计算和设计
4.3、连接的计算和设计
第五章:固体火箭发动机的热防护
5.1、热防护材料的工作条件特点
5.2、热防护材料和抗蚀材料
5.3、固体火箭发动机结构的温度状态
第六章:固体推进剂装药的强度计算
6.1、固体火箭推进剂物理力学性能的特点
6.2、强度判据
6.3、装药的计算区域
6.4、装药中的应力计算
6.5、装药几何形状对强度的影响
6.6、装药强度计算概述
第七章:固体火箭发动机特种结构件的设计
7.1、点火器
7.2、推力的调节方式
7.3、推力的调节装置
第八章:固体火箭发动机结构的工艺性
8.1、结构材料的应用特点
8.2、固体火箭发动机圆筒形金属燃烧室壳体和微锥形金属燃烧室壳体的制作特点
8.3、燃烧室壳体外筒的焊接
8.4、可机加零件的工艺性
8.5、推重比和材料利用率
8.6、非金属结构的工艺性
8.7、对固体火箭发动机壳体设计师保障推进剂装药制作工艺性的建议
第九章:固体火箭发动机自动化设计系统的特点
9.1、设计师的自动化工位
9.2、对自动化设计系统算法的要求
9.3、固体火箭发动机设计的方法原理
9.4、对设计师的实际建议
第十章:固体火箭发动机试验改进和可靠性
10.1、固体火箭发动机试验样机的试验改进
10.2、固体火箭发动机的可靠性
第十一章:固体火箭发动机的发展趋势和经济性
参考文献书目
命名法
下标
- accessory附件发动机中除四大部分外的零部件
- break破坏,burning燃烧, bolt螺栓
- bst-booster助推
- chamber燃烧室,cylinder柱段,case壳体
- con-conical锥形的
- cr-critical临界值
- design设计状态
- exit出口
- eq- equivalent等效
- er-erosive侵蚀
- f-fuel燃料,fin翼,filber纤维
- F-force推力
- g-gas燃气,气体
- h-
- initial初步的,节点编号;inside-内部
- ig-点火
- j-节点编号
- k-编号
- l-liquid液体,ningxiang,left左端
- L-Load载荷
- m-mass质量,motor发动机,matrix基体
- n-number数量
- o-out外部,oxigen氧化剂
- p-pressure压强,propellant推进剂
- q-
- r-gasgenerator燃气发生器
- s-sustainer续航,specific比,
- sph-spherical球形
- t-time时间
- T-temperature温度
- tr-transition section过渡段
- u-速度
- v-速度
- w-wing翼
- x-坐标
- y-坐标
- z-坐标
- α-角度
- β-角度
第一章 固体火箭发动机基本概念
1. 发动机结构
所有类型的火箭发动机中SRM是最常见的一种。图1.1.所示的SRM的组成中包括有为燃烧室,其中放置所用推进剂装药。固体推进剂可制作成一个或几个具有预先给定的由相应几何形状、燃烧面和包覆面(不燃烧面)大小所决定的装药3。
为了防止壳体的壁受燃烧产物的热作用,燃烧室壳体的内表面覆盖有热防护层4。如果壳体的构件受到气动加热,那么,给燃烧室壳体的外表面也涂有热防护层(见图1.1图号2)。装药的点火借助点火器14实施。点火器装有特种火药剂,其点燃首先是由引燃装置—电点火管13进行。喷管装置可由一个或几个喷管9,以及用于控制推力级和推力矢量方向的结构件8组成。在喷管的喉部表面安置有耐烧材料或具有一定(额定)烧蚀的嵌入块11。
图1.1、SRM示意图:1—带前封头的壳体;2—外绝热层;3—固体推进剂装药;4—内绝热层;5—防护固定层;6—减小装药边缘应力的人工脱粘层;7—后封头;8—推力矢量控制装置;9—喷管;10—喷管内绝热层;11—喷管喉部嵌入块;12—密封膜片;13—电点火管;14—点火器;15—装药翼槽
与其它类型的火箭发动机相比较,SRM具有下列优点:结构和使用比较简单;可靠性和安全性高;常备发射状态;使用费用比较低。
属于SRM的缺点也有:由结构件不能冷却所决定的工作时间有限;发动机的比冲相对小;在宽范围内调节推力困难;参数偏差范围大;复合推进剂成本高。
1.2、SRM的发展和应用历史
由现有的资料可知,SRM是所有类型喷气式发动机中最古老的发动机。
虽然SRM在俄罗斯火箭炮的应用基础还是由彼得一世所鉴定的,只是在十九世纪在这个应用领域才取得了显著的成就。在十九世纪初,А.Д.扎夏德科将军所制作的带有发射装置的战术导弹是那个时代新的有效武器。在十九世纪中期,К.И.康斯坦季诺夫在SRM研究、研制和火箭大规模生产方面取得了辉煌成就,同时,特别重要的是建立和组织了大规模的安全火药生产。在按照Н.И.季霍米罗夫的倡议所建立的第一个国家火箭技术装备研究和试验设计实验室,后来改名为气体动力实验室的基础上,研制出了火药和固体燃料火箭发动机—各种用途的发射装置。众所周知的并成功应用在伟大卫国战争的“喀秋莎”火箭装置,就是根据气体动力实验室所取得的研制成果所制作的。
但是,最近二十年的特点是SRM的发展速度特别高。在这一时期,高热值复合固体推进剂、非金属复合材料、热防护材料、高强金属和耐热金属的生产,在很大程度上促进了SRM的加速研制和其应用范围的扩大。
1.3、SRM的分类
将火箭分类直接搬到固体推进剂火箭发动机只是单方面地说明了固体推进剂发动机的种类。SRM的结构形状、它的性能和所完成的功能绝不是取决于发动机所用于的火箭类别。使SRM研制人员感兴趣的首先是参数、结构特点和使用条件。因此,图1.2所列的方式是按最典型特征对SRM的分类,并对于这一类型发动机的研制人员来说是可接受的方式。
图1.2SRM分类
1.4、SRM研制阶段和组织
可将新的SRM试验设计研制过程假定分为图1.3所示的一个阶段由另一个阶段产生并相互关联的几个阶段。
图1.3、SRM研制阶段
所列的阶段示意图包含了从新的SRM研制技术任务书的编制到根据发动机所有研制阶段完成结果所修改好的技术文件转交批生产厂可完成的整个工作范围。这个工作范围符合已形成的SRM研制惯例,并与所有机械制造领域大多数复杂制品研制阶段有许多共同之处。
编制并与订货方协商技术任务书是SRM研制过程中的初步和重要阶段。这个阶段对研制结果所达到的SRM技术性能水平、它的经济指标、研制周期,最终发动机的生存性和前景都有一定的影响。
一方面,明显的是,在发动机结构中不采用新材料、新工艺过程和较之以前所设计方案有改进的发动机结构方案,就不能研制出技术性能水平高的SRM。但是,如果结构中所采用的新发明在协商SRM试验结构研制技术任务书之前检验得不充分,那么,在研制过程中所产生的与必须解决所提出问题相关的困难,就会导致费用非计划性的,有时是实质性的增大并使试验设计研制完成周期改变。
因此,新的SRM研制技术任务书的编制和商定阶段开始的必须条件应是完成解决主要问题的预先研究工作。在这种情况下,应当记住,甚至是新的SRM研制在已经完成专题问题的科学研究工作基础上已经开始的条件下,随后在发动机试验调整过程中也会产生一系列能引起在具体发动机中出现新过程相互影响和现象的其它问题。
另一方面,对采用新材料、新工艺过程和结构方案的必要性应进行相当严格的技术和经济论证,而且,只有根据订货方和研制方对所产生的问题共同分析的结果,应作出关于新措施的合理性决定。在分析过程中,可能会找到从实质上简化问题和缩短研制周期的折衷解决方案。
地面试验的费用和周期主要取决于SRM的载荷和产品的可靠性水平。技术任务书中所要求的对载荷、可靠性水平、使用和贮存条件的过高要求会使试验数量、测量数量不必要的增大,从而延长新研制发动机的试验周期。
在技术任务书商定阶段之前,不足的科学试验工作量和技术任务书要求过高,不仅有不合理增大研制费用和拖延研制周期,而且,还在某些情况下,可能成为批产之前SRM结构无形老化的主要原因。对技术任务书的每一条准确表述,也是影响试验量和试验周期的必须条件,这种准确表述要使有可能定义和确定性地理解要求的条文。在这种情况下,有益的是,或者规定应当确认任何一些要求可完成性所用的试验种类(试验台点火试验、静态试验、实物试验或模型试验、用有发动机或火箭的组成试验),或者规定用计算,或者用提交带有用其他发动机在类似条件下的试验结果的报告,诸如此类来确认的充分性。
在商定技术任务书时,SRM研制单位应遵循的最重要条件是其对完成可能性的信心,或者是关于完成技术任务书所有要求的保障途径的明晰认识。这是由SRM和火箭其他构件的参数相互关系所决定的,未完全完成SRM其中某些主要参数都可能会成为违反彼此商定的火箭许多构件参数优化性的原因,并导致必须对这些构件根本改变。遵守所列举的条件对于达到很准确计划和实现SRM其余所有的研制阶段是必需的。
下一个阶段是草图设计、方案设计—从计算最佳的燃烧室内的参数和选择发动机的初步结构方案开始,然后,从保障SRM在技术任务书,用计算所给定的加载条件下的功能,对初步结构方案进行分析。根据加载的特性(力载荷和热载荷)选择发动机各种结构件所用的结构材料。在选择结构材料后,详细设计SRM各构件的结构,并考虑到保障高水平工艺性(特别是金属的工艺性)的要求。
旨在提高工艺性、减少设计方案费用和周期的有效措施有:在所研制的SRM中采用标准件、规格化零件、借用件、外购件和装配单元;使结构材料和研制好的先进工艺过程统一化,以及考虑到试制工厂和所指定批产厂的生产特点。
由于SRM结构简单,通常不制定技术设计方案,而是在编制和顺利通过论证草图设计方案后马上进行工程设计,并随后发放订购结构材料所用的工程技术文件,制作SRM试验样机并对其进行试验。
SRM试验样机的试制生产准备、制作和工艺试验阶段是在设计师的积极和直接参与下由试制生产的主要专家(总工艺师、主管冶金工作者、非金属和焊接主管专家,以及试制生产的主任)创造性指导实施。在同时保障SRM所有零件和装配单元功能条件下,这个阶段达到最好的工艺性。
根据有问题结构的修改完善(改进)程度和所将来批产规模,在试制生产阶段应开始推广新的先进工艺过程的工作。最合理的是从最开始就与将实施所研制发动机批生产的工厂一起进行这些工作。吸收批产厂参加与试制工厂一起生产固体火箭发动试验样机,就有可能根据批生产厂的生产特点和前景进一步大大减少批产准备的费用和周期,保障发动机结构的高工艺性。在采用不同工艺过程可能等值制作结构的情况下,必须选择批生产厂已掌握的工艺过程。如果在批生产厂没有按结构所规定的新的先进工艺制作用的设备和工装,那么,批生产厂就要预先购买这个设备、制作工装、采用新的先进工艺过程、确定与材料和配套制品供应单位相互关系的可能性。在试验样机制作过程中,根据制作工艺过程的修改完善结果,修正SRM的工作设计文件。
试验样机的试验改进阶段会提供评估SRM技术参数、可靠性及其与技术任务书要求相符性的可能性。在这种情况下,无论是结构各单独构件的功能,还是整体发动机的功能都应得到保障。这个阶段的持续时间和其完成周期取决于SRM的静态试验、动态试验、其它试验台试验、特种试验、在火箭组装中的飞行试验数量以及试验装备的复杂性、试验方法、在试验过程中的测量量和测量精度、试验结果的诊断和处理方法。在这个阶段,工作的计划和组织方面最重要的是,根据足够量的测量和试验结果和可信度条件下最小费用和周期判据,使试验数量、测量量和测量精度最佳化。旨在减小这个阶段试验完善周期和费用的有效措施是,最大限度考虑以前在其它SRM上对各种结构件的试验和检验结果,以及利用在对一个或几个发动机试验过程中,将各种检验最大限度的结合来减少试验数量。所有这一切都应在制定最佳试验大纲和试验方法以及在试验过程测量方法时考虑。
在确认完成技术任务书要求的试验改进完成后,进行跨部门试验。在跨部门试验过程中,跨部门试验小组正式记录SRM主要性能和参数与技术任务书中所给定的相符性。在这种情况下,跨部门试验小组审核成套设计文件,对批产厂按照其制作和提供SRM的适用性。这种适用性的最好证明就是对在批产厂所制作的尽可能多的SRM试验样机进行地面试验、飞行修整试验和特种试验。
1.5、SRM研制技术任务书
SRM研制技术任务书是按一定顺序排列的要求清单。为了确定包含在技术任务书中要求的主要内容、大致数量和性质,我们来研究其中一个可能的方案。
在技术任务书封面上写有准确定义的SRM名称及其代号。在固体火箭动力装置包含一个或几个SRM、舵机传动机构、电源和各种不同的辅助装置的情况下,将动力装置称为固体推进剂火箭发动机装置。
包含在总技术要求部分中的条目由火箭的存放和使用条件所确定。例如,在使用条件的条目中,应指明SRM单独地和在火箭装配中存放和运输时的周围介质温度范围、相对湿度、阳光辐射作用量和性质以及其它特性。使用性能的保持周期用求对最终装配好的火箭所确定的周期与从单个SRM最终装配时刻到其在火箭装配中最终装配时刻所经过周期之和确定。这些条件是对选择结构材料、涂料材料、胶质材料、热防护材料和包装材料有实质影响的因素之一。
在总则中,对SRM组成扩大了的说明附加规定,象推力状态,或推力大小或矢量控制机构、燃烧室数量,以及工艺特性的要求(保障发动机中各单独装配单元和火箭中的发动机互换性的必要性,它们彼此对接处的检验条件等)这样一些特点。对外观和外形尺寸的详细要求在技术任务书所附的SRM外观图的初步方案中规定。在草图设计过程中,对带有外形尺寸的外观图进一步精确,与订货方协商并与草图设计同时提交。
在这部分中,所给定的可靠性水平是确定试验数量最主要的因素之一。例如,为了验证50%置信概率下的0.9,0.99和0.999可靠性初步水平,理论上需要相应进行5,69和693次试验。实际上直接试验验证的只是可靠性初步水平,而然后采用旨在减少与用直接试验验证相关的费用和周期的分析法和专门制定的措施体系进行论证可靠性。例如,可列入到这种措施的有,采用能马上给出可信数据的完善检测方法,各种不同的模拟试验,包括数学模拟,以及采用以前在类似SRM上所进行的试验结果。
在总则中,也列入有对发动机所提出的特殊要求。例如,属于这些特殊要求的是在各种异常情况下(在跌落,机械损伤等情况下)保持防暴安全性或防火安全性,保障SRM的生物害虫防护,无毒性和保障发射装置安全性的特殊要求等。根据所拥有的试验资料和所积累的经验,对特殊要求可满足性的验证或用进行试验,或用对以前在在类似发动机和类似条件下所得到的结果系统化就可保障。
对SRM结构的要求相对独立,在该部分中指明发动机及其重要的组成部分的质量和外形尺寸的标称值和允许偏差。对质心和转动惯量随时间变化的要求相对于纵轴 和横轴 和 给定,并同样带有所允许的偏差范围。在这部分中也规定有结构特点(例如,具备火箭稳定器、火箭电缆线、压强传感器固定部件及对其的具体要求等),关于试验研制、批产和使用成本的具体要求,SRM中结构材料和其它材料供货情况等。
对发动机动力特性和参数的单独要求。在该部分中推进剂装药的质量、总冲、推力和工作总时间用极限值给定。内弹道特性用规定其完成概率给定,因为在使用在非设计状态下,这些参数的偏差是允许。
工作时间的详细特性用技术任务书中所附的推力和压强与时间的关系说明图给定(图1.4)。从电指令发送到发火管发火时刻起进行时间记录,时间记录时刻t0在曲线图上用点0表示。从点0到点1,也就是说,到装药点火时刻的时间通常称为装药点火延迟时间,并用tig表示。再到装药稳定燃烧时刻所经过的时间(点2)称为推力延迟时间,并用tiF表示。曲线图(Pc—t)上点2的位置根据现有的经验特别规定。点2通常是燃烧室中的压强达到0.30~0.40MPa,或达到喷管堵盖(膜片)飞出时的压强时刻,也就是说,SRM推力出现的时刻一致。进入工作状态的时间tw等于燃烧室中的压强达到通常等于Pcmax的0.7值(点3)时刻所经过的时间。在压强下降段上的点4也与燃烧室内的这个值一致。将从点3到点4的时间tb称为稳态工作时间。将从与点4对应的时刻到下降段上压强Pc≈0.30~0.40MPa(点5)的时间称为下降时间(ts)。
将从点0到点5的工作总时间称为SRM的工作时间-ta。
图1.4、SRM工作时间特性
在技术任务书的这部分中列出在试验样机上必须测量的SRM的参数。同时,在对发动机试验样机试验改进时可提交的确认实际可实现参数的原始文件,规定是有益的。
对各单独附件和装置(推力矢量控制、推力终止装置等)的要求在技术任务书的专门部分阐述。
在“发动机载荷”部分应列出最受应力的所谓“计算情况”的SRM力学载荷、热载荷和振动载荷的详细特性。如果订货方和研制方在共同审核技术任务书时,有足够的令人信服的技术根据,那么,在这部分中指明所商定的,不同于所规定标准的SRM各单独构件安全系数的标准。
在技术任务书应给定对SRM结构有实质影响的特殊条件的要求。属于这些要求的有,例如,运输和发射时运输发射装置对SRM的作用、在各级分离过程中,分离时对接舱或其它级发动机对该SRM的作用等。
在技术任务书的必须部分中也可说出指明在SRM各种不同研制阶段,对订货方所交验的文件清单和阐述对文件格式和内容要求的部分。
在完成共同审订后,形成技术任务书、由专家签署并由订购方和研制SRM的企业主管领导批准。必要时,与专业化的部门研究所商定技术任务书。
1.6、火箭特性和固体火箭发动机特性的相互联系
发动机推力总冲与火箭总质量之比是火箭的效率判据。对于带有SRM的单级火箭来说,这个比可记作如下形式:
\(\frac{{{I}_{\text{t}}}}{{{m}_{0}}}=\frac{{{I}_{s}}{{m}_{p}}}{{{m}_{0}}}=\frac{{{I}_{s}}}{1+\alpha +\frac{{{m}_{L}}}{{{m}_{p}}}}\), (1.1)
式中Is–比冲;m0–火箭初步总质量;mp–推进剂初步总质量;mL–火箭所运载的有效载重和火箭除SRM外的所有结构件的质量;\(\alpha ={{m}_{\text{s}}}/{{m}_{\text{p}}}\)–SRM质量效率系数,等于发动机结构质量与推进剂质量之比;ms–SRM结构的质量。
由公式得出的结论是,在火箭所运载的有效载重和火箭除SRM外的所有结构件的质量值恒定的条件下,提高火箭效率的主要条件是增大比冲和减小SRM的质量效率系数α。
SRM的质量主要部分为燃烧室壳体。燃烧室壳体由直径为D和长度为L的圆筒段和两个封头构成。由圆筒段和两个厚度相同的封头构成的壳体质量我们用mc表示,而喷管和发动机其它构件的质量用ma表示。那么,测定SRM的质量效率系数的表达式就变成如下形式:
\(\alpha =\frac{{{m}_{c}}+{{m}_{a}}}{{{m}_{p}}}\), (1.2)
式中\({{m}_{c}}=\pi D\delta {{\rho }_{c}}L\left( 1+\frac{D}{2L} \right)\);在这里\(\rho {}_{\text{c}}\)–燃烧室壳体外筒的材料密度,对于近似分析来说,封头假定是近乎平面的。
燃烧室壳体外筒的厚度根据强度条件测定:
\(\delta =\frac{{{p}_{c}}D{{k}_{c}}}{2{{\sigma }_{b}}}\), (1.3)
式中\({{\sigma }_{b}}\)–燃烧室壳体材料中的破坏应力;kc–燃烧室壳体外筒的安全系数。
放置在发动机中的推进剂质量
\({{m}_{p}}=\Delta \frac{\pi {{D}^{2}}}{4}L{{\rho }_{p}}\), (1.4)
式中\(\Delta ={{V}_{\text{p}}}/{{V}_{\text{c}}}\)–固体推进剂装药体积与SRM燃烧室壳体内容积之比,这里叫做体积装填系数;\({{\rho }_{p}}\)–推进剂密度。
在用表达式(1.3)和(1.4)表示公式(1.2),并代入等式(1.1)中后,我们就得到
\(\frac{{{I}_{\text{t}}}}{{{m}_{0}}}=\frac{{{I}_{s}}}{2\frac{{{\rho }_{c}}}{{{\sigma }_{b}}}\frac{{{p}_{c}}}{{{\rho }_{p}}}\frac{{{k}_{c}}}{\Delta }\left( 1+\frac{D}{2L} \right)+\frac{{{m}_{L}}}{{{m}_{p}}}+\frac{{{m}_{a}}}{{{m}_{p}}}+1}\)。 (1.5)
由对公式(1.5)的分析得出重要结论:第一,关于选择比冲最大和密度高的推进剂必要性结论;第二,关于在安全系数kc最小和燃烧室压强pc最小条件下选择比强度\({{\sigma }_{\text{b}}}/{{\rho }_{\text{c}}}\)最大的材料的必要性结论;第三,关于在同时保障容积填充度最大值Δ条件下选择大长径比L/D燃烧室壳体的合理性结论,第四,关于尽可能减小SRM喷管和其它结构件的质量必要性结论。
在实践中,所列举的参数是相互联系的,同时取决于火箭的参数和级数。例如,有时,SRM燃烧室壳体的长径比和安全系数是预先所确定的。根据作用于SRM的载荷组合和所要求的推重比,燃烧室内的高压强级可能是最佳的。因此,SRM参数的最佳值在每一具体情况下根据影响发动机效率的一系列问题单独确定。
为了研究各种对象相互联系的特性,在分析影响因素(独立自变量)的较小变化时,使用偏导数相互联系方程是很方便的。处在1%范围的影响估算误差是完全可以接受的。相互联系方程被大大简化(被线性化)并变成如下形式:
\(\Delta A=\frac{\partial A}{\partial B}\Delta B+\frac{\partial A}{\partial C}\Delta C+\frac{\partial A}{\partial D}\Delta D+…\)
可以看出,在这种情况下,研究的不是一般形式的复杂函数关系\(A=f\left( B,C,D,… \right)\),而是所研究的函数A根据自变量B,C,D增量的增量。偏导数值通常采用电子计算机用数值方法测定。函数A的小增量根据在所研究的计算点中自变量C,D,…值恒定(恒等)条件下自变量B给定的小增量求出。
例如,地空导弹到达目标的飞行平均速度与SRM的结构质量、推进剂质量和比冲的关系可用如下形式表示:
\(\Delta {{V}_{cp}}=\frac{\partial {{V}_{cp}}}{\partial {{m}_{c}}}\Delta {{m}_{c}}+\frac{\partial {{V}_{cp}}}{\partial {{m}_{p}}}\Delta {{m}_{p}}+\frac{\partial {{V}_{cp}}}{\partial {{I}_{s}}}\Delta {{I}_{s}}\)。
如果作为例子,对于确定的火箭来说,假定偏导数值等于
\(\frac{\partial {{V}_{cp}}}{\partial {{m}_{c}}}=-1.5\frac{m}{s\bullet kg};\quad \frac{\partial {{V}_{cp}}}{\partial {{m}_{p}}}=2.5\frac{m}{s\bullet kg};\quad \frac{\partial {{V}_{cp}}}{\partial {{I}_{s}}}=2.3\frac{m}{s\bullet s}\),
那么,结构质量增加10kg就会导致平均速度减小15m/s,这个可用在SRM燃烧室附加放置6kg推进剂或将比冲提高6.5s来补偿。
第二章:固体推进剂装药,固体火箭发动机的性能和结构方案
2.1、对推进剂装药的要求
根据预先编制的任务书,提出对推进剂装药的要求。属于对SRM推进剂所提出的要求中所规定的主要数据之列的有[3]:比冲、推进剂密度、推进剂燃速级别、推进剂装药的结构特点(尺寸、形状、与燃烧室壳体的装填方式或自由装填,等等)、使用、存放和运输的温度范围、推进剂的质量、总冲的最小允许值和最大值、发动机的工作时间、对物理力学性能(σ,ε等)的要求和其它。
比冲应理解为在SRM燃烧产物连续流出时间间隔(t)内发动机推力冲量与发动机工作同样时间间隔内所喷出的燃烧产物质量(mr)之比:
\({{I}_{s}}={{I}_{s,t}}/m{}_{r}\),
式中\({{I}_{s,t}}=\int\limits_{0}^{t}{Fdt}\);在这里,F–SRM的推力。
现代固体火箭推进剂的密度为(1.5~1.95)·103kg/m3。在推进剂装药质量恒定条件下,密度越高,发动机燃烧室的容积越小,SRM结构的消极质量就越小。对装药质量偏差有明显影响的密度值离散一般在(5~10)kg/m3范围。
由成分而定的复合推进剂燃烧产物温度在2900~3500K范围内变化。带有含硝基或氯粘合剂的含金属推进剂特有的是燃烧温度值较高。
根据建立在考虑许多根本影响火箭外弹道特性的因素基础上的预先分析结果,选择固体推进剂最佳燃速。固体火箭推进剂的燃速(或线性燃速)应理解为在单位时间内装药表面燃烧锋面沿表面法线的位移,即\({{r}_{b}}=de/dt\),式中de–在dt时间内所烧完的层。值e通常称为装药的肉厚。单位时间内装药单位表面烧完的推进剂质量通常称为质量速度:\({{r}_{m}}={{\rho }_{p}}\frac{de}{dt}={{r}_{b}}{{\rho }_{p}}\)。那么,对于燃烧表面面积为Ab的具体装药来说,质量流量将等于\(\dot{m}={{A}_{b}}{{r}_{b}}{{\rho }_{p}}\)。
固体火箭推进剂燃速与燃烧室内压强的关系式其中之一具有\(r=ap_{c}^{n}\)的形式,式中a-常数,n-指数,它们取决于推进剂的性质。
燃烧室内压强升高时速度增大的原因是由于燃气到推进剂表面的热传递加快而使凝聚相中的反应速度增大。
对于高燃速的推进剂来说,通常突出的是压强指数n的值较高。
由于固体火箭推进剂导热性低,同时燃烧时间短,在SRM工作过程中装药质量中还保持着初步温度。在装药初步温度变化时,推进剂燃烧机理就会发生变化,这种变化就会导致燃速变化。燃速与装药初步温度的关系借助固体火箭推进剂燃速温度梯度评定:
\({{k}_{T}}=\frac{{{r}_{T}}}{{{r}_{+20}}}=\frac{B-20}{B-T}\),
式中B–通过试验途径测定出的每一牌号推进剂的热化学常数。kT通常随着装药初步温度升高而增大。温度梯度随着燃烧室内压强的增大和推进剂中氧化剂粒子尺寸的减小而减小。
相同牌号的推进剂燃速可能由于存在原料性能的公差、存在推进剂组分计量精度的偏差和制备条件的差异所引起的工艺原因会不一样。因工艺原因的燃速值偏差借助统计系数\({{k}_{\text{T}}}=1\pm \Delta {{\text{\bar{r}}}_{\text{p}}}\)考虑,式中\(\Delta {{\bar{r}}_{p}}\)—近似等于±3~±4%的速度值偏差。
燃速取决于装药应变状态:在高变形和高应力区,燃速发生局部增大。此外,在过程快速变化期(在进入状态期内燃烧室内压强急剧变化时、在从起飞状态的高压强过渡到巡航状态的低压强时、在推力终止时等),燃速可与稳态工作状态时的燃速明显不同。
SRM的特种试验表明[3],在加速度场的固体火箭推进剂燃速可能与静态条件特有的额定速度明显不同。加速度场可在火箭机动、旋转或加速的过载作用下产生。造成加速度场中复合推进剂燃速变化的原因是,比较大的金属粒子被惯性力阻滞在装药的燃烧表面,从而改善凝聚相的热输入,增大局部燃速。推进剂成分中所包含的铝(或其它金属)粒子越大,在过载情况下,燃速的变化程度就越高。
加速度场中的非金属化复合推进剂燃速可能由于最大的高氯酸铵(AP)粒子在燃烧表面滞留,以及因燃料分解产物最密实蒸汽挤压装药燃烧面使加速度场中的扩散过程强化而增大。
在燃烧产物对装药表面冲刷的速度增大高于一定的值时,可能就会出现侵蚀燃烧。侵蚀燃烧的主要原因是使化学反应活跃的燃烧表面热输入急剧增大和高速燃气流吹除燃烧表面的液体和泡沫状粒子。吹刷速度随着装药内通道烧大而减小,而过渡到标准燃烧时侵蚀燃烧就会终止。将出现侵蚀燃烧时的吹刷装药表面的气流速度称为阈速度Vcr。阈速度取决于复合推进剂的性质和燃烧室内的压强。对于每一牌号的推进剂来说,在初步温度值和燃烧室内压强值给定的条件下,实验确定侵蚀燃速与燃速之比与横向气流速度的关系(\({{r}_{2}}=f\left( \varepsilon \right)\),式中\(\varepsilon ={{r}_{er}}/{{r}_{0}}\))并确定阈速度出现的时刻。
应当认为不是与速度r2的关系,而是与所换算出的质量速度的关系(密流)\(\delta =\rho \upsilon /\rho {{\upsilon }_{\text{cr}}}\)是比较严格的,式中\(\rho \upsilon \)-气流密度(质量速度);\(\rho {{\upsilon }_{\text{cr}}}\)-在马赫数 时圆柱通道中产生的气流临界密流。
那么,测定ε的表达式将具有\(\varepsilon =1+C\delta \)形式,式中C-对于每一牌号实验测定的常数。
为了估算双基推进剂(火药)的稳定燃烧范围,应使用Ю. А.波别多诺斯采夫判据:œ=Ab/Ap ,式中Ap-被转换成喷管的装药端面上燃气自由通道面积。œ值随着燃烧室的压强增大而增大。
采用物理方法和化学方法来人为调节推进剂燃速。最普及的化学方法是建立在提高燃料和氧化剂颗粒的分散性,在推进剂组成中使用增大或减小燃速的特种催化剂,或阻燃剂的基础之上的。调节燃速的物理方法是建立在装药中使用按照一定规律放置的可加热棒或加热片的基础之上的。这个方法的变体是借助嵌入在装药中,并用电流加热到给定温度值的导体来调节燃速。
2.2、固体推进剂
按照成分和结构,固体火箭推进剂被分为双基(均质)推进剂、复合(异质)推进剂,或改性双基推进剂。固体火箭推进剂成分和性能的基本资料在专著[3,68]中给出。
双基固体推进剂
双基推进剂(火药)由用硝化甘油溶解硝化棉形成,也就是说,这是一种分子中含有可燃性元素原子和氧化元素原子的有机物固溶体。
硝化纤维素的通式具有[C6H7(OH)3–x(ONO2)x]n,式中n=1,2,3– ONO2基数,它取决于纤维素的各种硝化条件,并确定硝化棉中的可燃元素与氧化元素的比例。
硝化甘油C3H5(ONO2)3是溶剂和余氧载体。由于在硝化甘油含量超过45%时双基推进剂的力学性能就会急剧下降,它们固有的是氧原子不足以点燃推进剂的可燃元素。由于负氧平衡的结果,双基火药的动力特性就比复合推进剂的动力特性差。
在双基组成中,采用增塑剂(凡士林、蜡和矿物油)就可达到提高在压制推进剂块的过程中所需的硝化纤维素的热塑性。为了提高在燃烧室低压强条件下的燃速和燃烧稳定性,在双基推进剂组成中采用催化剂(氧化钛、氧化铅、硫酸钾等)。炭黑和石墨粉末作为工艺添加剂使用并同时增大辐射能燃烧表面的吸收系数。
双基火药的密度在(1.5~1.65)·103 kg/m3范围,稳定燃烧压力级高于4MPa。
复合固体推进剂
复合推进剂是晶状氧化剂、聚合物基粘合剂燃料和金属添加剂的固化机械混合物。复合推进剂的密度在(1.6~1.95)·103 kg/m3范围。
采用富氧的固体高氯酸盐和硝盐(例如,高氯酸铵NH4ClO4或高氯酸钾KClO4)作为氧化剂。氧化剂为推进剂总质量的60~80%。在氧化剂含量增大超过85%的情况下,推进剂的物理力学性能和工艺性能就会急剧下降。含有作为氧化剂的具有较低分解温度和分解产物小分子量的高氯酸铵的复合推进剂得到了最广泛推广(AP)。在燃速与燃烧室内压强和推进剂初步温度的依赖关系微弱的情况下,含有高氯酸铵(AP)的固体火箭推进剂的动力特性是比较高的。减小氧化剂粒子的尺寸是提高燃速的途径之一。譬如说,在将高氯酸铵粒子尺寸(粉碎细度或粉碎程度)从100μ减小到5μ的情况下,推进剂的燃速就会增大一倍多。但是,应考虑到改为较小粒级高氯酸铵就会使得推进剂粘度增大并使工艺性降低。将等于一克物质中所包含的粒子总面积的粉末单位面积认为是氧化剂的细度指标。
复合推进剂中的聚合物基燃料同时起着粘合剂的作用,并为推进剂总质量的15~30%。燃烧产物温度的最大值和比冲的最大值为燃料含量质量接近15%的推进剂特有的。
根据粘合剂的类型,复合推进剂分为聚氨酯推进剂、聚丁二烯推进剂、聚硫推进剂(多硫推进剂)。聚硫推进剂动力较低,物理力学性能不高。具有作为粘合剂的丁二烯橡胶或聚丁二烯和丙烯酸共聚物的聚丁二烯推进剂拥有高动力性和很好的力学性能。由于比冲高、密度高和在零下温度(达-50℃)使用的条件下保持弹性的能力,组成中具有作为粘合剂的聚氨酯橡胶的固体推进剂得到了最大普及。用在固体火箭推进剂组成中加入约为推进剂总量20%的细粒(粒子大小为1μ到20μ)金属粉末和细粉(铝粉、镁粉、锆粉、铍粉、硼粉)就可达到显著提高固体火箭推进剂的比冲、密度和燃烧稳定性。由于两相流所产生的损失增大,进一步增大铝含量是无效的。
由于比较廉价、无毒性、工艺性好和能够提高几乎任何组成的推进剂的燃烧稳定性,铝得到了最大的应用。为了减小(燃烧产物中所凝聚的)氧化铝粒子的尺寸和增大燃烧的充分性,采用对铝粒子镀金属薄膜或有机薄膜。有时在含镁合金中使用铝。
为了提高固体火箭推进剂的动力特性,在它们的组成中也采用氢化铝、氢化铍等,其效率是用氢含量高导致燃烧产物的低分子量以及高燃烧热来解释。含铍的固体火箭推进剂是特别昂贵的。此外,它们的应用受到生产的高毒性和含氧化铍的燃烧产物的高毒性所限制。
添加其使有可能提高固体火箭推进剂动力的氢化铝具有最大意义。在固体火箭推进剂中作为改善工艺性能、动力特性或提高燃速的添加剂使用的是各种增塑剂(工业凡士林、蜡、工业用油)。增塑剂也是燃料,有时含有某种数量的氧化剂(硝基增塑剂),在装药制作过程中是推进剂稀释剂,能改进装药的物理力学性能,减小装填时的推进剂摩擦,但不参与聚合反应。
在推进剂组成中也使用一系列其它粉末状或液体添加剂。这些添加剂是参与聚合过程的物质(二异氰酸酯、对醌二肟、环氧树脂)和增大燃速的物质(二氧化铁和其它铁化合物、二氧化锆、有机元素化合物、金属复合氧化物等)。
改性双基固体推进剂
改性双基固体推进剂由带有铝添加剂的纤维素和高氯酸铵组成[52]。在这种推进剂中粘合剂较少,而氧化剂是高氯酸铵和由硝基化合物分解出的氧原子。高氧含量使用可能在比聚氨酯推进剂燃烧高~500℃的燃烧温度下得到高比冲。
这种推进剂的成本比一般的复合推进剂的成本高很多。
2.3、固体火箭推进剂装药
复合固体火箭推进剂装药主要是按照加压浇注或自由浇注工艺制作。根据发动机的结构和推进剂的物理力学和热物理性能,装药或者在SRM燃烧室壳体中直接成型,或者用为装药增强件的专用构架成型,或者单独用专用钢锭模成型。装药的内表面几何形状用安置在发动机燃烧室壳体内的工艺锥体成型。
装药的制作工艺过程包括准备粉状组分混合物(高氯酸铵的烘干、粉碎、分级等);准备粘合剂(真空处理、混合液体成分、制备粘合剂与铝的混合物);制备推进剂和成型装药;装药聚合(固化)。
在用加压浇注方法制作装药时,应使用连续工作的搅拌器。用搅拌器所制备的推进剂(各组分的比例用连续工作的剂量给料器和天平保障)借助螺旋装药机输送到钢锭模或发动机燃烧室壳体中。在填充开始时推进剂的压力比较小0.5~1.0MPa,在填充结束排气时增大到2~4MPa。
在自由浇注时,液体组分的准备和推进剂的搅拌在单独搅拌器中进行,然后将推进剂浇注到钢锭模或其中预先在其中形成真空的燃烧室壳体中。
聚合过程是在压力下(3~8MPa根据装药和发动机的结构而定)在高于正常温度(40~80℃)条件下进行15~25昼夜。聚合后将确定装药内构型的工艺锥体抽出。
双基推进剂装药以及(在个别情况下)某些牌号的复合推进剂小尺寸装药用直通式模压方法制作(在借助螺旋装药机将推进剂挤压通过成型装药横截面的外和内形状的压模,此后对装药进行固化)。
用各种不同方法对装药进行包覆:用浇注包覆料、对嵌入式装药缠绕并浸渍所缠绕好的层。在直接填充的情况下,预先敷设在燃烧室壳体内表面的防护固定层起包覆作用。
为了检验装药的质量,采用建立在使用超声和放射性辐射基础之上的综合现代探伤方法。在遵守相应预防措施的个别情况下,允许对装药机加。
将直接在燃烧室壳体浇注成型的并与燃烧室壳体内表面粘接的装药称为贴壁式装药。如果装药直接在燃烧室壳体中成型,但不与燃烧室壳体粘接,或者成型,而然后用专用构件在燃烧室壳体中固定,那么,将这种装药称为自由装填装药(图2.1,а, з)。
自由装填装药使用在必须将它们与外加热(例如,空气动力流)的燃烧室壳体热隔离,或者推进剂的低力学性能(强度和弹性)不能保障装药与燃烧室壳体一起变形的情况下。自由装填装药的主要不足是:SRM的容积装填系数比贴壁浇注装药低;必须将燃烧室壳体与燃烧产物作用热隔离;由于有自由装填装药固定和定中心结构件,结构的质量比贴壁浇注装药的大。
在燃烧室壳体中配置一个贴壁浇注式或自由装填装药的情况下,将这个装药称为整体式装药。双基固体火箭推进剂以圆柱形实心或空心装药形式制作。如果装药由两个和两个以上装药组成,那么,将其称为多根装药(见图2.1,a)。
图2.1、固体火箭推进剂装药形状:a-多根装药;b–翼柱式装药;c–星形装药;d–车轮形装药;e–端面燃烧装药;f–双筒式装药;g–圆柱锥形装药;h–自由装填装药。
在装药燃速恒定、喷管喉部截面和其它尺寸恒定的条件下,SRM的推力变化符合装药燃烧表面随时间变化的规律。这个规律由装药的几何形状所决定,并与在相同物理条件和推进剂均质性条件下固体火箭推进剂以平行层和时间上均匀燃烧的性能相联系。
图2.1所示装药的主要形状。固体火箭推进剂翼柱式装药(图2.1.b)的燃面是由圆柱形或锥形通道和翼槽形成。在横截面中固体火箭推进剂的星形装药内通道具有不同星尖数量(见图2.1,c)的星形状和不同轮辐的车轮状(见图2.1,d)。固体火箭推进剂端面燃烧装药是由一个或两个端面形成燃烧面的实心装药(见图2.1,e)。固体火箭推进剂双筒式装药由两个或两个以上同心配置的推进剂构件组成(见图2.1,f)。如果装药燃烧面由圆柱和锥形内通道段形成(见图2.1,g),那么,将这种装药称为固体火箭推进剂锥柱形装药。
为了得到较复杂燃烧规律,装药的结构可用所列举的各种装药形状构件组合制作。在这种情况下,为了得到较扩展的燃面,在装药中可另外制作环向和径向通道和翼槽。
中性燃烧规律用燃面在SRM整个工作期间(在其进入状态后直到发动机工作结束时的燃烧室内压强下降开始)保持接近恒定的装药燃面。例如,带有内燃烧通道和外表面及端面包覆的圆柱形无翼槽装药(图2.1,h)。
图2.2、P—曲线图:а—恒面曲线图;b—减面曲线图;c阶梯(双推力)曲线图
燃面随时间增大的装药保障所谓的递增燃烧规律(内通道燃烧的圆柱形装药)。在装药燃面随时间减小的情况下,保障递减燃烧规律(例如,带有外燃烧面的圆柱形装药b)。
2.4、固体火箭推进剂装药几何参数的计算
SRM的性能主要取决于推进剂的性能和装药的形状。因此,对装药的形状提出附加的要求:
1、在给定发动机使用温度范围和燃烧室最大压强条件下,同时保障与承力壳体一起法向变形时保障最大的装填系数、保障稳定无侵蚀燃烧、保障烧完的余药量最少。
2、保障在装药整个燃烧时间内发动机质心位移最小(或给定的位移)。
3、保障包覆和热防护层的质量最小。
任何一种形状推进剂装药的选择,都取决于在同时保障给定曲线图p—t(见图2.2)条件下最大限度地把发动机燃烧室可用容积装填满推进剂的意图。在P=const条件下的恒面燃烧曲线图(见图2.2,a)可用选择能提供燃面值沿肉厚恒定的这类装药结构来保障。如果没有任何其它限制要求,可偏重能提供燃烧室最大装填的形状。根据工作时间的变推力(见图2.2,b)可用选择星形或翼柱装药相应形状来保障。双推力变化(见图2.2,c)可用通道翼槽推进剂装药,双牌号的星形推进剂或其它形状保障。
由火箭发动机理论已知,燃烧面、SRM燃烧室自由面积、装药的初步肉厚厚度用下列关系式测定:
\({{A}_{b}}=\frac{F}{ap_{c}^{n}{{\rho }_{p}}{{I}_{s}}}\);
\({{A}_{i}}={{\varepsilon }_{i}}{{A}_{t}}={{\varepsilon }_{i}}\frac{{{{\bar{F}}}_{{}}}\sqrt{{{R}_{g}}T_{g}^{*}}}{{{{\bar{I}}}_{s}}{{{\bar{p}}}_{c}}\Gamma \left( k \right)}\); (2.1)
\({{e}_{0}}=ap_{\text{c}}^{n}t\), (2.2)
式中\({{\bar{F}}_{{}}},{{\bar{I}}_{s}}\)–总工作时间内的发动机推力和比冲平均值;r0–在标准条件(例如,pc=4MPa)下的燃速;εi =1.5~2.0—喷管亚音速段的收敛比;n–燃速幂关系中的幂;\(\Gamma \left( k \right)={{\left( \frac{2}{k+1} \right)}^{\frac{k+1}{2\left( k-1 \right)}}}\sqrt{k}\),k–膨胀等熵指数。推进剂的质量
\({{m}_{p}}=\frac{\bar{F}t}{{{{\bar{I}}}_{s}}}\)。 (2.3)
发动机的比冲
\({{I}_{s}}={{\varphi }_{\Sigma }}\frac{\sqrt{{{R}_{g}}T_{g}^{*}}}{\Gamma \left( k \right)}\left[ \varepsilon \left( 1 \right)2z\left( {{\lambda }_{a}} \right)–\frac{{{A}_{t}}}{{{A}_{e}}}\frac{{{p}_{H}}}{{{p}_{c}}} \right]\) (2.4)
式中\(z\left( {{\lambda }_{e}} \right)=\frac{1}{2}\left( {{\lambda }_{e}}+\frac{1}{{{\lambda }_{e}}} \right)\);\({{\lambda }_{e}}\)–喷管出口端的燃气速度系数。
推进剂的秒流量
\({{\dot{m}}_{p}}=\frac{{{m}_{p}}}{{{t}_{a}}}=\frac{{\bar{F}}}{{{{\bar{I}}}_{s}}}\) (2.5)
喷管喉部截面面积
\({{A}_{t}}=\frac{F}{{{I}_{s}}}\frac{\sqrt{{{R}_{g}}T_{g}^{*}}}{{{p}_{c}}\Gamma \left( k \right)}\)。 (2.6)
为了估算SRM的质量并优化其结构,必须预先选择好推进剂的牌号并确定发动机燃烧室中的压强、喷管喉部截面和出口端的直径。在下面所阐述的测定所列举数据的方法中,采用下列不会导致明显降低结果精度的假定:
1、过程的参数假定为平均值。
2、假定初步数据是恒定的,它们的值没有偏差。
3、忽略燃烧室和喷管入口端的压强损失.
4、忽略在装药端面区中贴壁浇注式或增强的装药中有环向弹性人工脱粘层时从推进剂中所除去的体积。
5、无论是在测定端面燃烧面时,还是在测定装药的体积时忽略装药端面形状型面的曲率,忽略使用它的等值平均长度。
作为例子,下面列出通道翼槽装药的计算。
固体火箭推进剂的通道翼槽装药可保障图2.2所示的任何一种燃烧规律。燃面随工作时间的变化规律用选择圆柱段长度(Lc)与翼槽段长度(Lw)之间的相应比来保障(图2.3)。由计算得出结论,在\({{L}_{\text{w}}}/d\approx 1\)时,通道翼槽装药燃烧规律接近中性规律,在\({{L}_{w}}/d<1\)时,燃烧规律为递减规律,在({{L}_{\text{w}}}/d>1\)时,燃烧规律为递增规律。过渡段的长度Ltr假定等于肉厚值 \({{e}_{0}}\)。
图2.3、通道翼槽式装药
假定在推力—时间曲线图上推力的初步值和终值是按时间给定的(例如,见图2.2,b)。
由发动机理论已知,1/2级推力之比:
\({{F}_{1}}/{{F}_{2}}\approx {{p}_{c1}}/{{p}_{c2}}={{\left( {{A}_{b1}}/{{A}_{b2}} \right)}^{1/\left( 1-\text{n} \right)}}\) (2.7)
关系式(2.7)使有可能确定装药几何特性与所需推力值的关系。我们列出方程组:
\({{A}_{b1}}+{{A}_{b2}}=2{{{\bar{A}}}_{b}} \)
\({{A}_{b1}}/{{A}_{b2}}\approx {{\left( {{F}_{1}}/{{F}_{2}} \right)}^{1-n}} \)
由这个方程组我们就会求出
\({{A}_{b1}}=\frac{2{{{\bar{A}}}_{b}}{{\left( {{F}_{1}}/{{F}_{2}} \right)}^{1-n}}}{1+{{\left( {{F}_{1}}/{{F}_{2}} \right)}^{1-n}}}\)和\({{A}_{b2}}=\frac{2{{{\bar{A}}}_{b}}}{1+{{\left( {{F}_{1}}/{{F}_{2}} \right)}^{1-n}}}\) (2.8)
在装药一级燃烧结束时,假定燃面等于Ab2,而翼槽段和过渡段已经烧完。最终燃面Ab2仅仅取决于\({{e}_{max}}=0\)时的圆柱段燃面。
由公式(2.3)假定推进剂的质量mp是已知的。假定用\(a,n,{{R}_{g}},T_{g}^{*},\Gamma \left( k \right)\)值表征的推进剂类型也是选择好的。
那么,Lc和Lw段的长度比以下列方式进行选择:
1、给定(选择)燃烧室的压强pc。
2、测定装药的肉厚值e0。
3、测定工作过程中的燃面平均值\({{\bar{A}}_{b}}=\frac{{{m}_{p}}}{{{\rho }_{p}}{{e}_{0}}}\)。
4、按照公式(2.8)计算初步燃面和最终燃面所需的值。
5、装药的最终燃面
\(A=\pi d\left( {{L}_{c}}-{{e}_{0}} \right)=\pi {{d}^{2}}\left( {{{\bar{L}}}_{c}}-{{{\bar{e}}}_{0}} \right)\) (2.9)
式中\({{\bar{L}}_{c}}={{L}_{c}}/d\)。
通过假定\({{\bar{e}}_{0}}={{e}_{0}}/d\le 0.33\)来保障装药强度并使公式(2.8)和(2.9)相等,我们就得到下列方程:
\({{A}_{b2}}=\frac{2{{{\bar{A}}}_{b}}}{1+{{\left( {{F}_{1}}/{{F}_{2}} \right)}^{1-n}}}\)
\[\frac{2{{m}_{p}}}{{{\rho }_{p}}{{}_{0}}\left[ 1+{{\left( \frac{{{F}_{1}}}{{{F}_{2}}} \right)}^{1-n}} \right]}=\pi {{d}^{2}}\left( {{{\bar{L}}}_{c}}-{{{\bar{e}}}_{0}} \right)\]。 (2.10)
通过完成d,Lc和\({{\bar{e}}_{0}}\)几种组合的计算,就可确定出装药构件的质量值和装药质量的最佳值。
6、第一阶段圆柱段中装药横截面面积确定为\({{A}_{T}}=\frac{\pi }{4}\left[ {{d}^{2}}-{{\left( d-2{{e}_{0}} \right)}^{2}} \right]\)。
7、计算装药总长度
\(L=\frac{{{m}_{p}}}{{{\rho }_{p}}{{A}_{T}}}{{k}_{L}}\),
式中kL=1.03…1.06—考虑到翼槽所占体积的系数。
装药翼槽段的长度\({{L}_{w}}=L-{{L}_{tr}}-{{L}_{c}}\),式中:\({{L}_{tr}}={{e}_{0}}\)。
8、每一当前时刻过渡段中的燃面可根据如下公式计算:
\({{\text{A}}_{b.w.tr}}={{n}_{w}}\left[ 2\left( {{}_{0}}-{{}_{w}} \right)+{{b}_{w}} \right]+2\left( e_{w}^{2}-\frac{\pi _{w}^{2}}{4} \right)+\pi {{}_{w}}\left( d-2{{e}_{w}} \right)-{{b}_{w}}{{n}_{w}}\),
式中bw–翼槽的实时宽度,\({{b}_{w}}\ge 20…40\)mm。逼近的精度是足够的,也就是说,过渡段占据装药体积部分不大(通常不超过3…10%);nW–翼槽数量。
9、计算翼槽型面和数量所需的装药翼槽段燃烧周长的初步值(Пw)用解翼槽段初步燃面的两个方程来计算:
\({{A}_{b.w}}={{\Pi }_{w}}{{L}_{w}}\), (2.11)
\({{A}_{b.w}}={{A}_{b}}-{{A}_{b.c}}-{{A}_{b,tr}}-2{{A}_{b,e}}\)。 (2.12)
因为,端面的燃烧面积不超过装药总燃面的百分之几,可忽略翼槽缺口和端面型面的曲率并假定翼槽等于圆柱段装药横截面面积,即\({{A}_{.w}}\approx {{A}_{T.}}\)。将表达式\({{A}_{T.w}}=\pi \left( d-2{{e}_{0}} \right){{L}_{w}}\)代入公式(2.12)中后
\({{A}_{.}}=\left( \frac{\pi }{2}{{}_{0}}b{}_{1}+0.42_{0}^{2} \right){{n}_{w}}+\pi \left( {{}_{0}}d-e_{0}^{2} \right)-{{b}_{1}}{{n}_{w}}\)
\({{A}_{.c}}=\frac{\pi }{4}\left[ {{d}^{2}}-{{\left( d-2{{e}_{0}} \right)}^{2}} \right]\)
并联立解方程(2.11)和(2.12),我们就会得到
\({{\Pi}_{w}}=\frac{{{A}_{b}}-\pi \left( d-2{{e}_{0}} \right){{L}_{c}}-\left( \frac{\pi }{2}{{e}_{0}}{{b}_{1}}+0.42_{0}^{2} \right){{n}_{w}}-\pi \left( {{e}_{0}}d-e_{0}^{2} \right)+{{b}_{1}}{{n}_{w}}-\frac{\pi }{4}\left[ {{d}^{2}}-{{\left( d-2{{e}_{0}} \right)}^{2}} \right]}{{{L}_{w}}}\).。
10、根据所得到的Пw值,图示选择翼槽的数量和型面,这样使得翼槽段和圆柱段的燃烧时刻同时到来,也就是说,使得达到肉厚\({{\bar{e}}_{0}}\)和从翼槽顶部到轮辐对称轴线与装药外表面交叉点的最小距离相等。如果这个距离完成得明显小于初步肉厚,那么,推力与时间的关系曲线将符合图2.2上的型曲线。在这种情况下,如果起飞状态推力相对持续时间为\({{\bar{\tau }}_{t}}={{\tau }_{1.t}}/{{\tau }_{t}}\),那么,在第一次逼近中,从翼槽顶部到射束对称轴线与装药外表面交叉点的最小距离将为\[{{e}_{1}}={{\bar{}}_{0}}{{\tau }_{t}}{{\left( {{A}_{b1}}/{{{\bar{A}}}_{b}} \right)}^{1/\left( 1-n \right)}}\]。在图示建立翼槽缺口(见图2.3)时,通常假定翼槽上方的圆拱厚度\(h\ge 20…30mm\),翼槽顶部的半径\(r\ge 10…20mm\),翼槽的宽度\(b\ge 2r\)。沿高度的翼槽宽度既可是恒定的,也可是沿装药轴线方向增大的。翼槽增宽开始的位置和翼槽倾角要选择得使在轮辐燃烧时排除在工作时可能会折断的长悬楔的出现。随着肉厚的燃烧,燃烧周长、轮辐燃面面积和翼槽段端面燃面面积的实时值在估算时用图解测定是方便和简单的,编制用电子计算机解析计算它们的程序是较复杂的和很非力气的,并可推荐用于一定类型翼槽缺口型面的实用目的。翼槽缺口的型面可能与传统的星形通道型式有实质的不同:无轮辐尖顶、轮辐侧棱可能不是平面,而是由几个平面或曲线面交叉形成,同时,可能会出现比传统星形型式多的燃烧阶段。
11、然后在燃烧室新的压强值\({{\bar{p}}_{c}}\)条件下重复计算,并在新\({{\bar{p}}_{c}}\)的条件下,重新完成装药尺寸(d和L)、缺口的数量及其型面的所有计算方法。对于其它类型的推进剂(a,n等的其它值)来说,可重复计算。
12、在每一种情况下(也就是说在\({{\bar{p}}_{c}}\)的每一个值条件下),合理的是根据公式\({{p}_{c.\max }}={{\bar{p}}_{c}}{{\left( {{A}_{bi\ \max }}/{{{\bar{A}}}_{b}} \right)}^{1/\left( 1-n \right)}}\)对最大压强进行评估,式中\({{A}_{bi\ \max }}\)根据已烧毁的肉厚不同实时值\({{e}_{i}}\)条件下测定的\({{A}_{bi}}\)值选择。通常,在燃波到达翼槽上方的圆拱时刻,也就是说,在等于圆拱厚度\({{e}_{i}}\)的条件下达到\({{A}_{bi\ \max }}\)值。
压强实时值根据\({{p}_{c.i}}={{\bar{p}}_{c}}{{\left( {{A}_{bi}}/{{{\bar{A}}}_{b}} \right)}^{\frac{1}{\left( 1-n \right)}}}\)计算。
计算每一实时时刻的推进剂燃速计算公式可用如下公式表示:
\({{r}_{bi}}=ap_{c\ i}^{n}\)。
在一定时刻的已烧去肉厚值根据公式
\({{e}_{i\ j}}={{e}_{i\ j-1}}+\frac{{{r}_{bi\ j-1}}+{{r}_{bi\ j}}}{2}\left( {{\tau }_{j}}-{{\tau }_{j-1}} \right)\)计算,式中\({{\tau }_{j}}\)-稳态开始所算起的当前时间。
在这种情况下,推力的表达式变成如下形式:
\({{F}_{i}}=\frac{{{}_{c\ i}}}{{{{\bar{}}}_{c}}}\left( {{{\bar{F}}}_{{}}}+{{}_{}}{{A}_{e}} \right)-{{p}_{}}{{A}_{e}}\)。
通道中无侵蚀燃烧的检验只有对于翼槽段前配置情况来说的合理的。在翼槽段后配置时(也就是说在喷管旁边时)通常无侵蚀。
翼槽段前配置情况下的通道通气面积根据如下公式计算:
\({{A}_{p}}=\frac{\pi }{4}{{\left( d-2e{}_{0} \right)}^{2}}={{f}_{p}}\frac{\bar{F}\sqrt{{{R}_{g}}T_{g}^{*}}}{{{{\bar{I}}}_{s}}{{{\bar{p}}}_{c}}A\left( n \right)}\)。
由此所计算的\({{f}_{p}}\)值应满足无侵蚀燃烧的条件,也就是说,在值方面不小于1.5\({{F}_{kp}}\)。如违背这个条件,初步肉厚(和相应的\({{e}_{0}}/d\)比)通常由于推进剂特性a,n的变化,也就是说,在根据a或n变化对推进剂提出新要求或在选择新型推进剂的情况下就会减小。
体积和质量根据关系式(2.3)…(2.6)由所需的冲量值测定。
用求推力实时值积分来检验等于\({{I}_{\Sigma }}=\bar{F}\tau \)的推力总冲量是合理的:
\({{I}_{\Sigma }}=\sum\limits_{0}^{{{\tau }_{0}}}{\frac{{{F}_{i\ j-1}}+{{F}_{i\ j}}}{2}}\left( {{\tau }_{j}}-{{\tau }_{j-1}} \right)\)。
2.5、SRM内弹道参数计算
根据第一章所研究的SRM研制技术任务书内容确定,在草图设计开始之前,通常给定发动机的下列参数:总冲量、工作时间、推力限制(最大值和最小值)、推进剂质量、外形尺寸限制(发动机的外径、发动机的长度、喷管出口端直径)。
在设计开始,应对发动机所提出的所有要求进行综合分析,由此形成初步概念(无摆满的零件,无详细的结构设计和计算):第一,关于使用的主要决定性条件和对发动机参数所提出的要求的概念(关于结构的温度状态、过载、空气动力加热、秒流量、推力曲线图类型等概念);第二,关于发动机总的结构配置方案的概念(关于推进剂的类型、推进剂装药的固定方式、主要结构件和绝热层的材料、有或无外热防护、燃气通道、推力矢量控制的燃气动力机构等)。
然后计算内弹道参数[3,53,54,62]。在这个阶段上,选择推进剂装药的形状;确定发动机中最大压强的最佳级;表述对推进剂的要求;对内弹道参数进行计算。在没有专门规定的要求和特殊使用条件(例如,在从飞机发射前,由于空气动力加热燃烧室壳体的温度不可避免增大到250…350℃和其它)的情况下,最合理的是选择外表面与燃烧室壳体外筒固定的推进剂装药。这种装药结构保障发动机内容积最大填充推进剂。对于在宽温度范围中所使用的SRM来说,在使用具有高物理力学性能,比如说,在低温条件下高变形性,这才会变得有可能,也就是说,从其强度观点来看,对于固定的装药来说,决定性的是在最低温度条件下的中心通道表面变形量。满足这类条件的有一系列具有密度值和比冲值大致相同的高弹性橡胶、高氯酸铵、铝和少量工艺添加剂混合物基推进剂配方。可用改变特种催化添加剂含量来变化燃速。
对于在窄零上温度范围所使用的SRM来说,可使用利用少许降低物理力学性能所达到的高密度推进剂。对于装有自由装填推进剂装药的SRM来说,可使用也是利用少许降低物理力学性能(弹性)所得到的高密度和高比冲推进剂。这样一来,根据所设计的SRM使用条件和所采用推进剂装药的固定方式,就可选择推进剂类型。
在选择装药的形状时,应根据所积累的类似SRM设计和试验经验。选择没有应力集中点的最简单结构(例如,径向和环向槽)作为装药的初步形状是合理的。简单的装药形状能提高SRM的工作和使用可靠性,简化工装,简化装药的工艺过程和提高对装药探伤的可靠性。在用简单装药形状,甚至是用小环形凹槽不能成功保障所需的燃面因已燃烧肉厚量而变化的(中性、递增、递减或组合)规律的情况下,选择复杂的装药形状—通道翼槽形状或星形形状。在某些情况下,势必会根据比简单性和可靠性要求更占优势的其它要求选择装药形状。譬如说,在工作时间短和推进剂质量大时质量流量值大的情况下(\(\dot{m}={}^{{{m}_{p}}}/{}_{\tau }={{A}_{t}}u\rho \)),更好的可为燃面扩展的复杂(例如,星形)装药形状,这种形状需要比燃面不扩展的简单形状小的推进剂燃速,对于简单形状的装药来说,所需的高燃速率可能是很难达到的。
在确定燃面与已燃烧肉厚值计算关系并将其与所要求的比较后,对所选的装药形状进行精确。按照类似上面所研究的方法对所选形状装药的几何参数进行计算,然后对发动机的内弹道参数进行计算。
计算SRM内弹道参数的主要任务是将根据工作时间测定燃烧室中的压强和发动机所产生的推力,而在有推力矢量控制气体动力装置也测定由这个装置所产生的侧向推力。同时解决下列伴随而来的问题:测定推进剂装药通道、封头内侧、燃气通道(如果有这种燃气通道的话)中的气流参数(压强、温度、气流速度),这些参数在计算发动机结构件和绝热层的热状态和强度时使用。
为了计算现代SRM内弹道参数,可采用建立在利用横截面平均参数解热动力学和一维气体动力学准稳态过程方程基础上的解析方法,并考虑到质量输入和压差沿燃烧室长度的变化性、喷管最小截面烧蚀、燃速与不同因素的关系等。
由于采用电子计算机,计算内弹道参数的计算方法得到了广泛使用,但是,它们也不排除在编制技术建议、编制技术任务书和草图设计阶段选择装药形状和发动机结构方案时估算内弹道所使用的人工方法。作为计算机计算内弹道参数方法基础的是:将推进剂装药划分成单元区、有限增量形式的气体动力学和内弹道学微分方程表示法和用数学方法,例如,龙格-库塔法、欧拉法、逐次逼近(迭代)法联立解气体动力学和内弹道学方程组。
将燃面划分成单元区就使有可能在计算每一个随后单元区时考虑由燃烧产物流变化条件和燃速、通道截面面积和燃面面积变化所引起的燃气供给量分配变化,并依次按照所有单元区计算所有特性沿推进剂装药长度的增量。按照喷管喉部截面质量流换算密度方程,检验所计算出的喷管入口滞止压力,在该压力未满足的情况下,以新的初步条件重新重复计算。根据最终所计算出的燃烧室压强值和喷管入口气流参数,计算发动机所产生的推力。
2.6、作用于SRM的载荷分类
在发动机飞行和地面使用过程中,一定组合的外部和内部力学载荷和热载荷都作用于发动机。
图2.4、作用于SRM的载荷示意图
将外部力学载荷换算成轴向力N、弯曲力矩M和剪切力Q。针对不同加载情形—飞行、起飞、分离时刻、运输等情形设计外部载荷图和N、M和Q分布图(图2.4)。外部载荷图,N和M的符号和值分布图由火箭研制单位计算并作为技术任务书的附件发给发动机的研制单位。
承力结构件的材料,以及这些结构件的形状和截面根据作用于SRM的等效载荷确定。
在计算结构件时,应考虑到在飞行时对其加热的可能性和环境温度、湿度和阳光辐射强度的变化。因此,为了测定所谓的最大加载《计算情况》,应不仅了解各种结构件的力学载荷,而且还有热载荷在发动机的整个《寿命》期内将是如何变化的。
对于某些结构件,例如,承受运输载荷的固定件和刚性箍来说,计算情况可与运输最大应力状态相对应。对于SRM的燃烧室壳体来说,飞行中的《计算情况》通常与飞行主动段结束相对应。到此时刻,等于发动机推力与火箭质量之比的轴向过载nx和燃烧室壳体外筒的运动加热就会达到最大值。SRM的燃烧室壳体一方面由于与周围介质的热交换,另一方面由于与燃烧室内燃气的热交换而被加热。
在选择材料时,还必须注意也可能为力学载荷和热载荷的局部载荷。可将直接加载在稳定器、控制机构、推力终止装置、运输发射装置等固定部件上的载荷称作局部力学载荷。
结构材料的选择也取决于载荷的施加特性。按照施加的特性,将静态加载与动态加载,一次性加载与多次和疲劳加载区别开。加载在SRM主要承载结构件(燃烧室燃烧室壳体和喷管体中的燃烧室壳体和连接件)上的载荷主要是属于静态载荷。由于在安全系数低的条件下采用高强结构材料,为SRM构件载荷主要部分的静态载荷使有可能实现高的质量效率。
对燃烧室壳体加载的特点
目前,在SRM中主要采用三种类型的燃烧室壳体外筒:金属外筒、玻璃纤维增强塑料外筒或有机纤维增强塑料外筒和组合外筒(双层—用玻璃塑料或有机塑料编织层增强的金属外筒)。
从强度计算观点来看,将SRM燃烧室壳体看作是在(环境)温度从负值变化到很高正值条件下通常一次或多次加载瞬时静态内压的容器。
燃烧室内的压强是作用于燃烧室壳体和所有种类SRM所固有的主要载荷。不同种类SRM的燃烧室内压强级和火箭不同级的轴向过载大致在下列范围内:
图2.4、作用于SRM的载荷示意图
将外部力学载荷换算成轴向力N、弯曲力矩M和剪切力Q。针对不同加载情形—飞行、起飞、分离时刻、运输等情形设计外部载荷图和N、M和Q分布图(图2.4)。外部载荷图,N和M的符号和值分布图由火箭研制单位计算并作为技术任务书的附件发给发动机的研制单位。
承力结构件的材料,以及这些结构件的形状和截面根据作用于SRM的等效载荷确定。
在计算结构件时,应考虑到在飞行时对其加热的可能性和环境温度、湿度和阳光辐射强度的变化。因此,为了测定所谓的最大加载《计算情况》,应不仅了解各种结构件的力学载荷,而且还有热载荷在发动机的整个《寿命》期内将是如何变化的。
对于某些结构件,例如,承受运输载荷的固定件和刚性箍来说,计算情况可与运输最大应力状态相对应。对于SRM的燃烧室壳体来说,飞行中的《计算情况》通常与飞行主动段结束相对应。到此时刻,等于发动机推力与火箭质量之比的轴向过载nx和燃烧室壳体外筒的运动加热就会达到最大值。SRM的燃烧室壳体一方面由于与周围介质的热交换,另一方面由于与燃烧室内燃气的热交换而被加热。
在选择材料时,还必须注意也可能为力学载荷和热载荷的局部载荷。可将直接加载在稳定器、控制机构、推力终止装置、运输发射装置等固定部件上的载荷称作局部力学载荷。
结构材料的选择也取决于载荷的施加特性。按照施加的特性,将静态加载与动态加载,一次性加载与多次和疲劳加载区别开。加载在SRM主要承载结构件(燃烧室燃烧室壳体和喷管体中的燃烧室壳体和连接件)上的载荷主要是属于静态载荷。由于在安全系数低的条件下采用高强结构材料,为SRM构件载荷主要部分的静态载荷使有可能实现高的质量效率。
对燃烧室壳体加载的特点
目前,在SRM中主要采用三种类型的燃烧室壳体外筒:金属外筒、玻璃纤维增强塑料外筒或有机纤维增强塑料外筒和组合外筒(双层—用玻璃塑料或有机塑料编织层增强的金属外筒)。
从强度计算观点来看,将SRM燃烧室壳体看作是在(环境)温度从负值变化到很高正值条件下通常一次或多次加载瞬时静态内压的容器。
燃烧室内的压强是作用于燃烧室壳体和所有种类SRM所固有的主要载荷。不同种类SRM的燃烧室内压强级和火箭不同级的轴向过载大致在下列范围内:
压强级的这个差别不会对承力壳体结构材料的选择有质的影响,但是对选择封头与燃烧室壳体连接类的型和选择内绝热层有影响。
燃烧室内燃气的温度和由燃烧室内压强级所决定的气流速度对选择内绝热层有影响:燃烧室内的温度、速度和压强越高,需要的热防护材料耐烧蚀性和耐热性就越高。
作用于SRM燃烧室壳体的有下列外部载荷:
迎面气流或周围水(对于水下导弹的SRM来说)的剩余外压;
因轴向过载而产生的和在火箭各级分离过程中与发动机邻接的火箭舱对发动机作用的压缩力;
在火箭转弯、与迎面气流成攻角飞行、导致在燃烧室壳体外筒的材料中出现附加压缩应力、拉伸应力和切向应力的侧向过载时所产生的弯曲力矩和扭矩;
在火箭以大速度通过密实大气层时或火箭外挂在超音速飞机上时壳体外筒的运动加热。在第一种情况下,采用外热防护,在第二种情况下,采用外筒的耐热材料和防止固体火箭推进剂装药加热的结构措施;
被列入到局部载荷的配置在壳体上的结构部件的力学载荷和热载荷(例如,在采用连接发动机与火箭的开式桁架舱结构时,对凸出在外面的壳体构件和SRM前封头的局部热作用)。
结构材料的选择取决于所列举出的载荷单独或同时对结构的作用。
2.7、SRM初步结构方案的设计
根据对技术任务书内容的研究结果,设计师提交未来发动机概略总图,将发动机分为主要结构工艺部件,指定主要构件的结构材料。同时考虑到区别所设计发动机与已知发动机的技术任务书特殊要求。
在开始时,确定燃烧室内压强的大致级。然后,按照上面所阐述的方法计算发动机的主要参数,选择推进剂,确定装药的形状和尺寸、喷管喉部截面的尺寸和喷管型面的母线坐标。所有列举出的数据使有可能开始设计发动机初步结构方案。
用细线沿预先选择的装药形状轮廓完成初步结构型式的制图。此后,图示完成示意图配置—设计主要结构件(前封头、后封头;封头与燃烧室壳体连接部件;喷管装置构件和喷管装置与燃烧室壳体的连接部件;装药与壳体的固定件;点火器;耐侵蚀构件的热防护层等)。绘制初步结构图以布局—《配置》固定部件、挂架、发动机与其邻接的火箭舱的连接而完成。在用这种方式设计初步结构图后,对初步发动机的特性与技术任务书的要求相符性分析。
在绘制SRM结构图时,重要的是不仅要了解方法的顺序,而且还要了解各单独部件、零件和整体发动机的一系列设计特点。这就使有可能避免进行大量设计计算分析的必要性。
了解设计特点和预先预见到发动机各种不同零件和构件设计的结构特点和工艺特点的能力就成为设计师工作的创造性基础。在设计SRM结构方案时应考虑到的一些建议在第九章给出。
第三章:承载结构的结构材料选择
为了评定采用某一种材料的合理性,必须进行技术经济分析,技术经济分析是对潜在结构比较,以便选择最佳的材料,也就是说,在消耗最小和结构质量最小条件下具有最好性能的材料。根据这种分析的结果,如果在结构质量减轻大于极限值,昂贵的材料就可能是比廉价材料更可接受的。在分析过程中,除了材料价格外,还必须考虑制品和整个系统的成本。在计算材料的采用效率时,应当考虑不仅减小质量,而且还有伴随因素。将标准的两级弹道导弹发射质量消极质量减小1公斤等同于将所需推进剂减少40公斤。
作用于结构的载荷组合对选择这些结构的最佳材料有决定性的影响。从选择材料的主要准则(保障最小质量)的观点来看,对承载结构(例如,SRM壳体外筒)来说,如果结构中决定性的加载方式是拉伸,最有利的将是比强度最大的材料,或者,如果决定性的加载方式要求保障结构的稳定性,最有利的将是比刚度最大的材料。比强度理解为材料强度极限与其密度之比(\({{\sigma }_{b}}/\rho \))。比刚度理解为材料弹性模量与其密度之比(\(E/\rho \))。
3.1、金属
高强金属的主要性能在表3.1列出。由这个表可看出,铍的比强度值和比刚度值最高。此外,铍具有高导电性、高导温性、高耐热性、高熔点、高沸点、高耐蚀性、在周围介质参数变化时尺寸和形状不变化的性能,铍的密度低。这个金属被列入突出的航空航天材料之列,并拥有对核技术有吸引力的性能[47]。铍的应用在不断扩大。此外,铍具有下列缺陷:成本高、有毒性和冷脆性。
表3.1 高强金属
材料 |
密度, 1·10-3kg/m3 |
拉伸强度极限, 1·10-9Pa |
拉伸弹性模量,1·10-9Pa |
比强度, 1·10-6Pa·m3/kg |
比刚度, 1·10-6Pa·m3/kg |
极限延伸率,% |
强度下降的开始温度,℃ |
高强合金结构钢 42Cr2MnSiNiMoА(ВКС-1) 43Cr3SiNiMoWAlА(СП-43) |
7.79 |
1.76 |
201 |
22.6 |
2580 |
0.90 |
280 |
钛合金WTi22 |
4.68 |
1.18 |
108 |
25.2 |
2308 |
1.27 |
300 |
可变形铝合金В96Ц-3 |
2.89 |
0.54 |
67 |
18.7 |
2318 |
0.90 |
100 |
铍合金 |
1.86 |
0.76 |
271 |
40.9 |
14570 |
0.28 |
100 |
耐蚀钢 03Cr11Ni10Mo2Ti-WCu(ВНС-17) |
7.95 |
1.76 |
192 |
22.1 |
2415 |
0.20 |
300 |
目前,在美国纯铍的使用总量约为180吨并多半在下列技术领域:在核技术领域(~15%)、在航天技术领域—用于绝热板、吸热板、火箭和飞机的结构中(~60%)、在仪表制造业中—用于陀螺仪、电子计算机(~20%)、在光学仪器(~4.5%)、在航空发动机制造业中(~1%)。目前,根据毛坯件的种类,一公斤铍的价格在150…5700美元范围,并(在产量增大的条件下)有几乎降低二分之一的展望。例如,如果在惯性制导仪器中使用铍时,铍的优点是如此之大,而需求如此之小,以致价格具有次要意义,那么,在SRM承载结构中采用铍经济上是明显不合理的。技术性能-脆性高和在拉伸载荷条件下对缺口的敏感性增加了在SRM承载结构中采用铍的经济不合理性。
因此,表3.1所列出的其它金属在SRM生产中得到了最大的推广。由表中所列出的数据可看出,高强铝合金在比强度方面次于钢和钛合金,但在比刚度方面与它们接近。考虑到铝合金比钢高并比钛合金还高的工艺性和低成本,可将它们用来制作嵌入到燃烧室内的喷管部件和大批量生产稳定工作的SRM壳体(例如,潜射导弹的SRM)是很有效的。
高强钛合金和高强钢在SRM生产中得到了广泛应用。它们的应用需要专门的热处理制度、焊接后各单独构件和整体产品的连接、高的工艺技能。甚至是小的违反制作和检验规程都可能导致结构强度降低。
到目前为止,所达到的SRM设计和制作技能水平决定了大量所采用的高强金属结构强度的一定极限水平(\({{\sigma }_{b}}\le 2…2.4\)GPa)。试图在制作(SRM壳体那种)焊接容器时实现结构强度高于2.4GPa的材料暂时还未成功。
高强钢
通常,将在所有形式强化后强度极限\({{\sigma }_{b}}\le 1.5\)GPa的钢认为是高强钢。这种强度级是在两类钢-高碳中合金钢和马氏体时效钢( 不锈钢)上达到的。
高强钢的主要不足是对应力集中点的敏感性高。根据缺口相对轧制板材配置的方向,高强钢因应力集中的断裂趋势是不同的。根据专著[26]的数据,由马氏体时效钢所裁切的试件在不同方向具有不同的断裂韧性值。在缺口横着轧制纹配置时就会看到最大的断裂韧性。高强钢上的应力集中点视材料的厚度表现各不相同。试验件越厚,应力集中点存在表现的程度就越大。
为了减小高强钢对应力集中点的敏感性,采用下列冶炼方式:真空电弧冶炼;合成炉渣钢水罐精炼;电渣再熔炼;电子束再熔炼。这些方式使有可能降低钢中的气体含量、硫和磷有害杂质的含量。
结构高碳中合金高强钢在淬火和低温回火后就获得了最大强度性能。这些钢的强度主要是利用提高碳含量(大约0.48%)形成的[13]。随着碳含量增大到0.48%,淬火的低温回火钢的硬度和强度就开始增大,并保持塑性断裂特性。在含碳量进一步增大时,硬度开始继续增大,而拉伸强度开始减小(图3.1)。断口的塑性图变为脆性图。
图3.1、在220℃两小时回火后钢的性能与碳含量的关系曲线
在塑性和韧性良好的条件下,钢高强度性能的结合用在增大抗脆性断裂性条件下复合加入强化铁素体和提高钢淬透性的合金元素保障[36]。
我们来简要研究一下主要合金元素的影响特性。
铬(在结构钢中加入大约3%)使有可能提高硬度和强度,改善淬透性。与此同时,加入铬就使钢的韧性和塑性有点降低。
硅(加入大约2%)就使有可能在同时提高热稳定性、耐酸性和弹性性能时不降低韧性而提高强度。硅对4340钢强度的影响用图3.2所示。随着硅含量从0.24%增大到2.8%,在300℃回火温度条件下强度极限开始就从1.6增大到2.2GPa,同时塑性性能降低[10]。
锰(加入大约2%)就使有可能不降低塑性而提高硬度和冲击韧性。
镍(加入大约5%)能提高抗蚀性,同时提高强度、塑性、冲击韧性、淬透性并降低线性膨胀系数。应考虑到结构钢的密度随着镍的含量增大而增大。
钨(在结构钢中加入大约1.5%)由于生成碳化物(固体化合物)就会提高钢的硬度和热硬性。在结构钢中加入钨会在加热时阻止晶粒增长和回火脆性产生。
钼(在结构钢中加入大约0.6%)会提高强度、硬度、热稳定性,稍微降低韧性和塑性,并减小脆性。
钛(添加大约0.2%)使有可能提高强度和耐蚀性,有助于晶粒粉碎,但会增大钢的密度。
图3.2、硅含量对厚度1.79mm 图3.3、BKC-1钢性能与回火温
钢板强度和断裂韧性的影响 度的关系曲线(淬火940±10℃;
回火-2小时)
在钢的牌号开始用数字指明碳的百分数平均含量。元素的百分比含量(如果元素含量不超过1.5%)用相应字母之后的数字指明。钢的高纯度(有害杂质的最小量)和对冶金检验的高要求用可在牌号末写上的字母A表示。
这样一来,合金元素的结合和含量就使有可能得到对缺口敏感度适中的高强度极限钢。
在表3.2列出了在美国和英国火箭制造业和航空制造业中最普及的高强钢主要牌号和化学成分以及一些俄罗斯产钢牌号。由所列的数据可看出,对于不同的钢来说,淬火的加热温度值和淬火介质是不同的。
在比较低的回火温度(200…300℃) 条件下,高强钢具有最好的力学性能结合,这一点可由表3.2和图3.3中广泛普及的高强钢BCK-1(42Cr2MnSiNiMoА)例子看出。
在200…300℃温度范围回火时,强度极限依然在相当高的水平,在将回火温度升高超过300℃时,钢的强度极限、屈服点和塑性会大大降低。这就说明了为什么高强钢要在低温下回火这个事实。这种带有低温回火马氏体结构类型的钢强度极限主要取决于碳的含量。为了得到高于2GPa的强度极限,钢中的碳含量应不小于0.4%。超过0.4%的碳含量通常是极限的,因为,否则钢的脆性断裂趋势、对缺口的敏感性和比例因数的影响就会急剧增大。在按照表3.2的制度热处理后,BCK-1钢就获得了力学性能的最佳结合。
表3.2、高碳高强钢的力学性能
钢牌号 |
热处理制度 |
σb(MPa) |
σT(MPa) |
δ,% |
Ψ% |
|
淬火t秒,℃ |
回火t,℃ |
|||||
4330 |
815在油中 |
245 |
1760 |
1440 |
10.0 |
– |
4340 |
815在油中 |
230 |
1950 |
1610 |
10.0 |
35.0 |
30CrMnSiNiWМo |
930空气中 |
250 |
1680±10 |
1310~1420 |
6.0 |
35.0 |
42Cr2MnSiNiМoА |
930空气中 |
250 |
1860±10 |
– |
6.0 |
– |
28Cr3SiМoWVА |
940空气中 |
350 |
1620 |
– |
7.0 |
– |
38Cr3SiNiМoWVА |
940空气中 |
350 |
1760 |
– |
7.0 |
– |
3.2、纤维复合材料
近10-15年来,航空航天技术进步使得大大改进了飞行器的最重要参数,其中包括减小SRM的消极质量比率。这些成就中有相当大作用是属于研制了全新的结构材料—纤维复合材料,它们拥有传统金属合金和聚合物材料实际上达不到的高水平强度性能、物理性能和其它性能(图3.4)[60]。这些材料的采用使得有可能制作完全符合工作特性和工作条件的给定性能的结构。
图3.4、技术成就对减小飞行器消极质量的相对贡献
图3.5、结构材料所采用的门捷列耶夫表的元素
业已查明,玻璃纤维强度为块状玻璃的50—100倍。这是因为微分子强度主要在纤维轴线方向中定向和累加以及急剧减少在纤维小的外表面产生缺陷(裂纹、气泡,诸如此类)—断裂源。用粘合剂将纤维结合在一起就可得到性能独特的纤维复合材料。在纤维复合材料出现之前,采用过基体中有门捷列耶夫元素周期表第二、第三和第四族所列元素的一些材料来生产飞行器(图3.5)。
其余的元素由于密度高是不可容许的。
我们来研究第二和第三族的元素(Li,Be,B,C,Na,Mg,Al,Si,P和S),从由其制作最小质量的结构材料观点来看,这些元素具有最大意义。显然,其中四种元素(图3.5上所划掉的Na,Li,P和S)由于其化学活性不再研究。在实践中,广泛采用的是Mg,Al,Ti,Cr,Fe(图3.5上置入粗线框中的)元素基结构材料。剩余的元素中只有四种元素Be,B,C和Si(图3.5上置入双框内)适用在结构材料中采用。
硼非常脆,因此,在块状体中是不适用的。硼纤维是用在直径13μ左右的难熔钨丝上气相沉积硼得到的。按照一般工艺由氯化硼得到的硼纤维直径为76—127μ。纤维的连续长度达3000m。硼纤维的基本性能如下:
密度,kg/m3 2600
拉伸强度极限,MPa 3500
弹性模量,MPa 420000
熔点,℃ 2050
硼纤维的比刚度具有重要意义,它超过玻璃纤维比刚度4倍,超过高强钢、钛合金和铝合金比刚度5倍。
为了降低硼纤维成本,在美国研制出了在直径为0.032mm碳纤维上沉积硼的方法[80]。
环氧粘合剂硼纤维增强塑料得到了最大普及。美国《Авко》公司的硼纤维增强塑料的基本性能如下:
强度极限,MPa 1750
弹性模量,MPa 220000
块状体的碳也是脆性的并在承载结构中是不可使用的。碳纤维是由粘胶丝或聚丙烯腈在1600…3000℃温度下热解得到的,在热解过程中产生一定的拉伸。根据温度和拉伸程度就得到高强碳纤维(σb=2100~2450MPa, E=250…280GPa)或高模量碳纤维(σb=1400~1750MPa, \(approx 380Gpa\)纤维用来制作下列半成品:短切纤维、短纤织物、预浸布和连续粗纱。国外工业高模量纤维HT的基本性能如下:
密度, kg/m3 (1700…1800)
拉伸强度极限,MPa (2400…3100)
弹性模量,GPa 约300
到1973年,根据纤维的类型,一公斤碳纤维的价格为180…380美元。随着生产的扩大,价格会迅速下降。
碳纤维增强塑料多半是采用环氧粘合剂制作。环氧碳纤维增强塑料的基本性能如下(根据《考陶尔兹》公司法国分部的数据):
格拉菲尔 HT-1 |
格拉菲尔 HM-5 |
|
密度, kg/m3 |
1500 |
1600 |
拉伸强度极限,MPa |
1600 |
1300 |
弹性模量,MPa |
130000 |
190000 |
比强度,MPa.m3/kg |
107 |
81 |
比刚度,MPa.m3/kg |
8700 |
12000 |
除高比刚度外,高模量碳纤维增强塑料拥有高的耐静力强度。碳纤维增强塑料的减震能力和耐振强度比金属高,这是因为在相同应力级条件下,变形比玻璃纤维增强塑料的变形小,这就会减少聚合粘合剂破裂。碳纤维的高导热性会降低材料的自加热。碳纤维的性质保障碳纤维增强塑料小的或者甚至是负的热膨胀系数(对于环氧碳纤维增强塑料来说,沿纤维方向的热膨胀系数在20…300℃范围内为1.5…5.0·10-6(1/℃)。在外部剩余压力、弯曲力矩和轴向压缩力作用下,稳定工作的结构中采用碳纤维增强塑料是有前景的。也研制出了《碳/碳》复合材料,在这种复合材料中采用碳石墨化基体作为碳纤维的粘合剂。这种材料具有高的绝热性能、化学惰性,将强度性能保持到很高的温度并具有下列性能(碳纱基复合材料):
密度,kg/m3 1460
抗拉强度极限,MPa 在20℃条件下28100
在2500℃条件下27400
为了得到《碳/碳》复合材料,开始用甲酚醛树脂将碳纤维粘合起来,并随后在压力下固化,然后使所得到的碳纤维增强塑料在可控制气氛中受到力学作用和加热(碳化)。碳化后所得到的孔隙度使有可能对复合材料进行再饱和碳(例如,沉积CH4蒸汽碳)。因而就得到密度为1600kg/m3于0.7GPa材料。采用《碳/碳》复合材料制作SRM喷管超音速扩散段是合理的。
由碳纤维和金属-粘合剂(铝、镁、镍)组成的复合材料较之硼纤维基非金属复合材料是很有前景并具有实质的优点。金属碳复合材料比金属硼复合材料便宜和工艺性好。
《联合碳化物》公司(美国)的《镍/碳》复合材料的大致性能如下:
密度, kg/m3 4700
抗拉强度极限,MPa 800
在1000℃条件下的强度极限,MPa 200
弹性模量,MPa 266000
除玻璃纤维外,碳纤维是复合材料很有前景的和有效的填料。正在初步拟定改进碳纤维制作工艺和进一步提高它们力学性能的一些途径。在实验室条件下,已得到抗拉强度极限为3.5GPa和弹性模量为700GPa的纤维。
块状体的硅与硼和碳一样,作为结构材料是不适用的,但是玻璃纤维在比强度方面超出所有已知的结构材料。美国空军科学研究所所研制出的高模量玻璃纤维在密度为2600 kg/m3左右时抗拉强度极限为5.6GPa,弹性模量为126.5GPa[51]。
玻璃纤维是用将所熔化的玻璃液挤压通过直径0.8-3.2mm的喷丝头并在喷丝头出口以约3800m/min的速度快速拉伸到19…35μ。纤维的一般直径等于6…9μ。
用玻璃纤维制作复合材料所用的下列类型填料。
纱(丝)由连续单纤维组成(纱中有200左右根纤维)。
粗纱由一系列合并成带的平行不加捻纱组成(粗纱中有12、60或120根纱)。粗纱或纱用来缠绕制作产品。如果粗纱或纱预先浸有树脂(粘合剂)并以预干燥形式进入缠绕过程,那么,将产品的缠绕过程就称为《干法缠绕过程》。如果粗纱或纱在缠绕前直接经过树脂,那么,就将缠绕过程就称为《湿法缠绕过程》。
短切纤维是将粗纱切成6-50mm小段得到的。可将所短切的纤维与树脂一起喷敷在用于制作产品的模具上。可用短切纤维与树脂的混合物准备压制配料。
无纺布垫用来手工成型和压制简单形状的零件,不用预先成型。
织物分成两种类型:捻纱织物和粗纱织物。捻纱玻璃布采用在要求零件均质性和较高强度的情况下,以及用来用缠绕方法制作零件。
玻璃纤维将物理力学性能保持到350℃温度。将玻璃纤维加热到400…500℃温度并随后冷却会将其强度降低几乎二分之一。
对于承力壳体来说,采用由具有合金添加剂的铝硼硅组分所制作的玻璃纤维。对于热防护(烧蚀)复合材料来说,采用达1200℃都不会降低特有性能的二氧化硅纤维和石英纤维。
有机纤维。化学的重大成就使得有可能制作出非常有前景的高强高模量聚合物基纤维[75,77]。《杜邦德聂穆尔》公司(美国)的凯夫拉-49有机纤维(原来的代号为III型PRD-49)具有下列性能:
密度, kg/m3 1450
抗拉强度极限,MPa 2500
弹性模量,MPa 130000
延伸率,% 2.1
比强度, MPa.m3/kg 193,000
比刚度,MPa.m3/kg 9,000,000
这种耐化学物质的纤维也拥有比玻璃纤维大20…30%的抗表面损伤性、良好的电绝缘和绝热性能并在达290℃温度都不会失强。
在比强度方面,有机纤维可与玻璃纤维竞争。但是,比较低的压缩强度和高塑性变形以及高成本都限制着有机纤维增强塑料的应用。目前,有机纤维增强塑料被用来制作SRM壳体。
用在一种复合材料中将高模量有机(聚合物基)纤维与碳纤维组合所制作的纤维复合材料具有意义。在这种复合材料中,聚合物纤维提高弹性、冲击强度并降低密度,而碳纤维提高强度和刚度。
由所引证的结构纤维复合材料综述可看出,这些复合材料与传统金属合金的区别是复合材料与结构制作同时成型。同时,制品中的复合材料力学性能取决于纤维的铺放方式并可由制品的制作单位有意识地变化,也就是说,结构可以可调节材料各向异性来制作。因此,在研制用缠绕方法制作的复合材料结构时,设计就需要同时包括不仅是确定结构几何尺寸的问题,而且还有确定材料的内部结构-层的数量和交互方式、定向角度、增强纤维的种类及其在复合材料中的相对含量的问题。这就需要保障结构形状与复合材料的性能和用连续缠绕方法实现结构的工艺条件相符合。因此,下面简要说明用缠绕方法制作结构的主要工艺流程图。
连续缠绕方法使有可能制作形状相当复杂的回转壳体(SRM燃烧室壳体、喷管的扩散段、点火器构架等)。用连续缠绕方法制作结构的过程由下列组成过程构成:将由单向纤维组成的带(粗纱)浸胶,送到旋转芯模上并按测地线或以与测地线的小偏差铺放。根据燃烧室壳体的加载特性和它的几何形状,缠绕可与芯模旋转轴成任何角度(从0到90º)进行。沿圆周所缠绕的纱带层(与芯模轴成90º)只是承受圆周(切向)应力。为了使壳体能够承受轴向载荷,必须在环向层之间铺放纵向层。
表3.3给出了针对用纵向-横向缠绕制作的圆筒计算出的主要复合材料比较性能。为了直观比较,金属(除铍外)和纤维复合材料的比刚度性能用图3.6所示。
图3.6、结构材料比强度和比刚度值对比
结构材料的选择取决于作用于结构的主要载荷。由表3.1,3.3和图3.6得出的结论是,对于短时工作而不持久加热的SRM壳体来说,采用有机纤维增强塑料是最有效的。在采用聚酰亚胺树脂作为玻璃纤维增强塑料粘合剂的情况下,在300℃以下温度条件下采用玻璃纤维增强塑料和有机纤维增强塑料是有利的。在这种情况下,玻璃纤维增强塑料本质上就变得比金属更有效。但是,在SRM壳体直径为200mm以下时,有机纤维增强塑料和玻璃纤维增强塑料由于发动机燃烧室内径的减小和在强度相同的条件下的壁厚比金属的壁厚大,可能就不如高强金属有利。同时,在SRM壳体直径小和延伸率大的条件下,有机纤维增强塑料和玻璃纤维增强塑料由于对火箭所不允许的弯曲变形比金属壳体大得多,总的说来可能是不能允许的。所以,选择材料之前应对由不同材料制作的结构应变状态进行比较评定。同时,应考虑到纤维复合材料在增强方向拉伸时在断裂之前都是线性弹性的,然后,应进行技术经济分析,并考虑到不仅是制品,而且还有整个系统因素的影响。也应考虑到生产工艺条件和新设计实施周期。
我们来研究一下被作为选择《钛-3Ц》、《民兵》、《短跑》、《不死鸟》(美国)导弹SRM壳体材料基础的最可能理由。
《钛-3Ц》导弹助推SRM壳体具有下列主要尺寸:长30m左右,直径3.5m。壳体大概基于下列原因用钢制作。壳体的生产是唯一的,也就是说,制作特别庞大的设备、工装和工艺机械在经济上未必是证明有效的:一方面,它需要相当大花费和相当长时间的研制和调试周期,另一方面,在采用后由于所制作的壳体批量小,它会闲置很长时间,同时,制作这种外形尺寸的焊接金属壳体可按已试验调试好的工艺过程实施。此外,在每一次加载工作内压后,安全系数小(1.35…1.5)的玻璃纤维增强塑料壳体变化是微乎其微的,但会丧失部分强度。众所周知,《钛-3Ц》导弹助推SRM金属壳体是多次使用的。这会产生相当大的效果。采用多次使用的玻璃纤维增强塑料壳体就需要改变热防护的涂敷工艺并增大壳体的安全系数,而这就会导致壳体质量增加并使其造价增大。这种SRM壳体由彼此可机械连接的比较短的分段件组成。壳体质量由于有延伸率小的玻璃塑料增强塑料舱特种连接的增大就会减小玻璃纤维塑料的优势。
表3.3、高强复合材料
材料 |
密度 kg/m3 |
拉伸强度极限, MPa |
拉伸弹性模量, MPa |
比强度, MPa.m3/kg |
比刚度, MPa.m3/kg |
极限延伸率,% |
纤维强度开始降低的温度,℃ |
纵向-横向缠绕的玻璃纤维增强塑料(玻璃纤维,环氧散装树脂) |
2070 |
980 |
39200 |
47,300 |
1,894,000 |
2.5 |
350 |
纵向-横向缠绕的硼纤维增强塑料(硼纤维,环氧散装树脂) |
2060 |
880 |
117 |
42,700 |
5,680,000 |
0.75 |
500 |
纵向-横向缠绕的碳纤维增强塑料(碳纤维RAE,环氧散装树脂) |
1540 |
550 |
110 |
35,700 |
7,143,000 |
0.5 |
2000 |
纵向-横向缠绕的有机纤维增强塑料(玻有机维,环氧散装树脂) |
1350 |
780 |
42170 |
57,800 |
3,124,000 |
2.1 |
80 |
备注:1、性能是针对在复合材料强度极限与纤维强度极限之比为0.285条件下用纵向-横向缠绕制作的标准圆筒计算测定的。
2、复合材料强度开始降低的温度取决于粘结材料:对于一些聚醚树脂来说为150℃,对于铝和聚酰亚胺树脂来说为250…300℃,对于铜来说为540℃,对于镍来说为800℃,对于陶瓷来说为800℃以上。
一次性使用的《民兵》导弹第三级和《短跑》导弹两级发动机尺寸比较小,工作时间短,在工作时间内壳体的壁材料本身保持着初步的低温度(约80℃)。这类因素可能就决定了这些发动机壳体用玻璃纤维增强塑料螺旋缠绕方法制作。
众所周知,《不死鸟》机载导弹悬挂在超音速飞机的机翼下面或机身下面。这就意味着,当飞机飞行时,扰流导弹的超音速空气动力气流可能使发动机壳体受到运动加热数十分钟。在研制《不死鸟》导弹开始时还没有用聚酰亚胺粘合剂生产玻璃纤维增强塑料足够的经验,也就是说,没有在超过80…100℃温度条件下工作的玻璃纤维增强塑料。这大概也是采用高强钢制作《不死鸟》导弹SRM壳体的原因之一。
第四章:SRM结构件的计算和设计
由飞行器的研制实践已知,没有其质量在再设计时最好不可能是被降低的结构。由图3.4可看出,设计方法在使有可能降低结构质量的措施总量中起着重要作用。
在本章中阐述了SRM最典型结构件的估算原理和对其设计的建议,这些建议在解决结构材料的有效使用和达到未来结构工艺性:确定结构件最合理的相互配置和选择结构件最合理形状的问题时是必需的。
4.1、金属结构件的计算和设计
发动机外筒
SRM壳体的主要承载结构件是外筒。从强度设计和计算观点来看,发动机壳体的外筒被看作是薄的轴对称外筒。按形状,壳体的外筒分为圆筒形、锥形和球形外筒,而按有无焊缝,分为(用环形焊缝、螺旋焊缝和纵焊缝)焊接的外筒和无焊缝(旋压和整压)外筒。外筒可为光滑的,或具有钎焊或焊接在它上面的局部构件。外筒末端可为法兰或封头转接部分,而且壳体可具中间刚性箍(环、护圈、卡箍)。
为了近似估算长的光滑圆筒中燃烧室内压强的作用初步应力,我们利用如下公式:
\({{\sigma }_{1}}=\frac{{{p}_{c}}D}{2\delta };\quad {{\sigma }_{2}}=\frac{{{p}_{c}}D}{4\delta }\) (4.1)
式中\({{\sigma }_{1}},\ {{\sigma }_{2}}\)–沿母线和沿环形截面中的相应应力。
在有将几段外筒连接成一个外筒或将外筒与法兰连接的环形焊缝时,就可产生对外筒增强(增厚)的必要性(图4.1.a)。焊缝附近增厚的必要性通常是与下列工艺特点相关的。在焊接两个邻接的壳体时不可能达到所焊接边沿整个环向的理想重合。由于所焊接边直径不同、厚度不同和焊接装配时的偏差,就会产生焊接边偏移(见图4.1.b。此外,焊缝的综合力学性能(\({{\sigma }_{b}},\varepsilon ,\psi ,{{a}_{k}}\))次于基材的类似综合性能。而且,焊缝附近区域可能会产生因焊缝不可避免的收缩和在焊接外筒热处理过程中不均匀的热影响所引起的圆筒母线畸变。
图4.1、对接焊接:a—焊接边增厚;b焊接边偏移。
在长的外壳中,忽略在边缘作用的载荷影响。对于其将完成\(\beta l\ge 3\)条件的壳体认为是长外壳,式中\(\beta =\frac{\sqrt[4]{3\left( 1-{{\mu }^{2}} \right)}}{\sqrt{\frac{D}{2}\delta }}\)。
对于金属外壳来说,采用泊松系数\(\mu =0.3\),我们就会得到\(\beta =\frac{1.285}{\sqrt{\frac{D}{2}\delta }}\)。所以,可将\(l\ge 2.4\sqrt{\frac{D}{2}\delta }\)的外壳认为是长外壳。
长圆壳外壳中的初步应力根据公式(4.1)计算。在计算短圆壳时,应考虑圆壳末端的法兰或封头的增强作用。
对壳体外壳的稳定性评估根据著作[6]中所列出的公式进行,这些公式考虑了下列载荷的作用或组合:在无燃烧室内压时SRM壳体外壳上的外部余压、轴向压缩、弯曲力矩等。在这种情况下,通常,不考虑固体火箭推进剂装药的增强效应。归根结底,在所谓的计算情况下(也就是说,在最大总载荷作用的情况下),计算作为每一个其它承载结构件的壳体外壳的等效载荷对壳体的作用。
我们来研究在计算情况下轴向力N、弯曲力矩M和燃烧室内压强pc同时作用于壳体外壳的例子。
圆壳外壳中外部力的最大法向应力\({{\sigma }_{\max }}=\frac{N}{\pi D\delta }+\frac{4M}{\pi {{D}^{2}}\delta }\)。
燃烧室内压强的应力根据公式(4.1)计算。那么,外壳中所有力的作用的等效应力将为\({{\sigma }_{1}}=\frac{{{p}_{c}}D}{2\delta };\quad {{\sigma }_{2eq}}={{\sigma }_{\max }}+{{\sigma }_{2}}\)。
由此可见,实际上,沿两个轴线的实际应力与等于1:2的理想应力是不一致的。因此,在评估外壳的内载荷和外载荷作用的双轴应力状态时,必须知道根据在模拟双轴加载的条件下试件试验所得到的结构材料力学性能。
为了较精确测定壳体外壳在双轴加载条件下的应力变形状态,必须考虑到壳体的长细比、局部增强和过渡区等的影响。
封头
设计SRM前封头和后封头(喷管一端)的问题包括确定封头外壳最佳的形状和壁厚度。金属封头通常用冲压或旋压制作,很少用沿整个表面机加制作。封头通常以沿整个表面相同的厚度制作。封头可与壳体成一体制作或单独制作。封头与壳体用法兰、螺纹和其它连接。可将在内容积相当大的条件下和保障与发动机所连接火箭舱最好布局的条件下满足最小质量要求的工艺封头列入最佳封头。
半球形封头的质量最小,这是由子午线应力和环向应力相等的无力矩应力状态所决定的:\({{\sigma }_{sph}}=\sigma {}_{1}={{\sigma }_{2}}=\frac{{{p}_{c}}{{R}_{sph}}}{2\delta }\),式中\({{R}_{sph}},\delta \)–封头外壳球形部分的半径和厚度。
半球形封头的最小质量与等于0.58的b/R比一致(图4.2)。最小质量存在的原因是,在封头外径相同的条件下增大b/R会使Rsph减小,因而会使在封头达到半球形时达到最小值的外壳厚度减小。但是,另一方面,在b/R增大时封头的表面也在增大,这就有助于增大封头质量。绝热层的存在会使b/R的最佳值减小。但是,比值的减小会导致压缩从封头到壳体过渡区中的环的力增大,因而会导致环的应力和质量增大。
在已得到最大普及的椭圆形封头(图4.2.a)中,应力s1和s2可根据方程\({{\sigma }_{1}}/{{R}_{1}}+{{\sigma }_{2}}/{{R}_{2}}={{p}_{c}}/\delta \)测定,式中R1和R2–相应的子午线和环向曲率半径。在封头中心,R1=R2=Rsph,因此,s1=s2=ssph。在边缘上\({{R}_{1}}={{b}^{2}}/R\),而R2=R,环向应力\({{\sigma }_{2}}=\frac{{{p}_{c}}R}{\delta }\left( 1-\frac{{{R}^{2}}}{2{{b}^{2}}} \right)\)。
图4.2、封头示意图:а-椭球形封头;b-碟形封头;c-比采诺封头。
封头圆周边缘上的压缩应力和壳体圆筒外筒上的拉伸应力是从封头到圆筒外筒过渡段上弯曲变形的原因。在比b/R=0.707的条件下压缩应力\{{{\sigma }_{2}}\)等于零。在这种情况下,\{{{\sigma }_{1}}={{p}_{c}}R/\delta \),但是,壳体外筒和封头的边缘位移差依旧存在。因此,从封头到圆筒的过渡区域使用环加强。
建议根据如下公式测定椭圆封头的厚度:
\{\delta =\frac{1+2{{b}^{2}}/{{R}^{2}}}{6{{b}^{2}}/{{R}^{2}}}\frac{{{p}_{c}}R{{k}_{c}}}{{{\sigma }_{b}}}\),
式中kc-安全系数。
椭圆封头的\{b/R\)值应在0.4…0.7范围内,特别可建议的值为0.607。
环形球形封头(蝶形封头)(见图4.2. b)由球形面与环形面在封头圆周部分结合构成。在这种情况下,\{{{R}_{T}}\ge 0.12R\)。
由拉普拉斯方程得到下列应力:在环形部分\{{{\sigma }_{1}}=\frac{{{p}_{C}}{{R}_{T}}}{2\delta }\left( 2-\frac{{{R}_{T}}}{r} \right)\);\{{{\sigma }_{2}}=\frac{{{p}_{c}}{{R}_{T}}}{2\delta }\);在球形部分\{{{\sigma }_{1}}={{\sigma }_{2}}=\frac{{{p}_{c}}{{R}_{sph}}}{4\delta }\)。在球形到环形面的过渡区域会产生附加弯曲变形。碟形封头的这个很大的缺陷在比采诺封头中被减小(见图4.2.c)。
在比采诺封头中球形到壳体圆柱形外筒的过渡面由方程\{x/R=0.15\arccos {{\left( r/R \right)}^{2}}-0.26\sqrt{1-{{\left( r/R \right)}^{4}}}\)给定的曲线旋转形成,式中x和r–坐标(r轴通过E点)。封头的壁厚度可根据无论是常数,还是变量的计算结果确定(除半球形封头的壁外)。在确定壁的变厚度之前应进行深刻的工艺经济分析,这种分析一方面要考虑到封头质量减小效果,另一方面要考虑到必须附加机加或采用旋压所产生的费用。
第五章:SRM的热防护
SRM结构件的功能取决于固体推进剂燃烧产物的参数和成分,取决于燃烧产物与发动机内部构件之间、发动机周围迎面气流与外表面之间的热交换强度以及发动机的工作时间。
对现代SRM参数的分析表明,燃烧室内燃烧产物的最大压强在4…15MPa范围,而工作时间1.5—100s。现代复合固体推进剂的特点是燃烧产物温度高(Tg=3000…3500K)、凝聚相粒子含量大(约为质量的40%)。在燃烧产物的这些参数条件下,现代SRM中的热交换过程进行得非常剧烈。对现代SRM主要构件的热强度的分析表明,它们的单位热流可达到20…116×106w/m2。
显然,对发动机壁不采取专门的热防护措施,在发动机点火后过某一时间发动机就会因下列其中一种原因而毁坏:由于对壁的加热或力学破坏或由于壁烧毁、材料熔化或分解破坏。
因此,在设计SRM时,应力图制作使承力壳体的温度在整个工作过程中都不超过所允许的值。这一点用正确选择承力壁的热防护方式、有根据的选择结构的材料和确定结构主要构件所需的厚度来达到。
5.1、热防护材料工作条件的特点
SRM的承力壁通常用热防护材料防高热焓燃烧产物的作用。SRM燃气通道的材料在化学活性燃气流中,在燃气、单位热流和温度梯度的高温、高压和高速条件下工作。也必须指出,各种各样的装药几何形状(有翼槽、有翼肋、有突然扩大和收缩)会使SRM气流通道中出现复杂的流体运动图。十分明显,在这些条件下,燃气通道的大多数热防护材料带有质量烧蚀工作,这可能是由高热焓燃气流的热作用(焦化、热化学分解、熔化、升华等)、(含凝聚相的)高速燃气流对所加热表面的化学和力学作用以及上述所有总和的因素所造成的。
通过研究SRM燃气通道热防护材料的质量烧蚀任何机理,就可以指出,决定在任何质量烧蚀机理条件下材料功能的主要因素是对材料的加热程度,这是在燃烧室中给定的燃气温度和压力条件下由燃气的运动速度所决定的。
根据气流对热防护材料的作用强度,可将SRM燃气通道划分成下列区域:
1)滞留区域;
2)前封头区域(燃烧产物运动速度达50m/s);
3)喷管后封头区域(燃烧产物运动速度达300…350m/s);
4)喷管通道的亚音速区域(燃烧产物运动速度从350m/s到音速);
5)喷管装置的喉部区域;
6)喷管通道的超音速区域(速度达2500…2800m/s)。
对于前三个区域来说,热防护材料的主要用途是防护承力结构件过分加热;对于后三个区域来说,热防护材料的主要用途是保持给定的几何形状。这种情形也就决定了将材料主要分为热防护层和抗蚀层。因为工作条件和对材料的具体要求变化范围宽,应始终考虑这种划分的相对条件性。
由于SRM中气流的各种不同气体动力特性,为了正确选择和确定抗蚀材料和热防护材料,就需要根据SRM的结构特点,仔细研究固体推进剂燃烧产物流对材料的复杂体动力作用、热作用和化学作用;根据材料性能变化和结构转变仔细研究气流与材料之间的相互作用;仔细研究所采用材料对SRM特性的可能影响。
5.2、热防护材料和抗蚀材料
相当大的内部热载荷和外部热载荷都作用于SRM结构件。内部热载荷是由高压强和燃气高运动速度条件下的燃烧产物高温度所造成的。
外部热载荷是由火箭发射时(特别是由发射井发射时)的高温气体作用和在密实大气层飞行时的空气动力加热所造成的。因此,在较低温度条件下,强度就开始明显降低的高强钢、合金和玻璃纤维增强塑料承力结构件就需要专门的热作用防护。
壳体和封头的热防护层
橡胶和混合粘合剂基弹性比较轻的材料越来越广泛地被用作壳体内表面的热防护层。在选择发动机燃烧室内防护的热防护层时,内防护的限界尺寸和工作条件具有重要的意义。壳体和封头的内热防护是指热防护层和防护固定层。
热防护层的功用是防护结构承力壳体免受高温燃气流的作用。防护固定层的功用是保障固体推进剂装药与壳体牢固的固定和防护固体推进剂免受外部热流(空气动力加热)的作用。
对绝热层提出下列要求:表面破坏温度尽可能要高;抗热分解、抗热氧化分解和抗燃气烧蚀性要高;耐各种不同介质化学稳定性;导热性和导温性要低;比热要高;密度要低;无论是对金属表面,还是对装药或防护固定层的粘附性要可靠。
对防护固定层提出下列要求:密度要低;强度和刚性性能要接近装药的性能;性能在时间上要稳定;对承力壳体表面和装药表面的粘附性要可靠;防护固定层抗湿性要足够。
为了防护发动机燃烧室的壁免受热作用,采用橡胶基弹性热防护层和夹布酚醛塑料或模压材料制作的刚性热防护层。
燃烧室热防护层的主要组分是粘合剂(高分子树脂、橡胶、橡胶和树脂混合物)和填料(磨碎的氧化物、矿物、固化和磨碎的树脂)。
为了保障工艺性,在热防护层配方中采用特种添加剂。
橡胶基热防护层的弹性大、导温性低、密度较低、热防护性能稳定、喷涂工艺性好。但是,它们的很大缺陷是在燃气流速度大的条件下抗蚀性低。
刚性热防护层的特点是抗蚀性高、热防护性能稳定、物理力学指标高。但是,它们的弹性(延伸率)小,这就会导致热防护层在发动机工作时破坏。由于承力壳体变形大,热防护层就可能会随时间以及在运输和振动时而破坏。
就其性能是弹性和刚性热防护层中间的并将它们优良性能结合的热防护层是涂有橡胶和加有填充料的布。这种材料的性能取决于橡胶和布中所包含的组分。同时,布的影响不仅取决于纤维的性质,而且还取决于布织纹的类型。
根据成分,热防护材料以片状、粒状、粉末状形式生产。在制品零件上的喷涂方式应根据半成品的初步状态选择。
采用胶合剂将热防护层固定在壳体的表面上,这些胶合剂应保障热防护层在制品长期存放时与零件表面粘附的可靠性;保障高的耐热性;保障一定的弹性;保障工艺性;保障(与所胶合的热防护层一起)的制品金属表面的侵蚀防护。
在最大程度上能满足规定要求的是橡胶和高分子树脂基多组分胶合剂。
为了防护燃烧室内表面,采用两种类型的材料—橡胶基材料和耐热塑料。
对于在温度高,但燃气运动速度小($\omega \le 50m/s$)条件下工作的SRM前封头和壳体的内热防护来说,通常采用酚醛橡胶材料和无矿物填料的橡胶。
对于在燃烧产物速度高(达150m/s)条件下燃烧室构件的热防护来说,采用相同类型的材料,但或者是用石棉布增强的材料,或者是带有矿物填料的材料,这些材料保障高的抗蚀性。
对于壳体过渡区域的后封头热防护来说(对于ω达300m/s的发动机的各区域来说),石棉布基、玻璃布基和碳布基层状材料(表5.1和5.2)得到了最大普及。
在所列举的材料类型中采用在520…700K温度下发生分解的酚醛树脂和环氧树脂作为粘合剂。所指出的层状材料的缺陷是拉伸延伸率低,通常不超过1…1.5%,这就会在采用其作为壳体的热防护材料时产生一定的困难。为了提高带有任何填料的甲酚醛树脂基类似材料的弹性,在材料中采用多半是丁二烯丙烯腈橡胶取代部分酚醛树脂。在这种情况下,物理性能和抗蚀性变化不大,但抗拉强度减小[83]。属于在燃气速度不大区域所采用的橡胶状材料之列的有类似腈基橡胶、丁二烯腈橡胶、聚氨酯橡胶和丁基橡胶的混合体。聚氨酯热防护层采用在《民兵》导弹第一级壳体的前部中。应认为,在许多SRM中,其中包括在《民兵》和《北极星》导弹SRM中所采用的聚丁二烯丙烯腈共聚物基材料具有最合适的性能。这些用能保障高抗蚀性的填料增强的材料用于燃烧室其它构件的热防护。石棉、二氧化硅、碳、石墨和其它粉末状、纤维、颗粒状的材料作为填料添加。
在耐热塑料中主要采用有机硅树脂、酚醛树脂、环氧树脂、聚醚树脂作为粘合剂。酚醛树脂得到了最大普及。塑料的增强用无机填料、二氧化硅填料、石英填料、碳填料、石墨填料、石棉填料、陶瓷填料实施。填料的含量一般为25…35%。
表5.1、 布基热防护层[42]
热物理性能 |
带(在900K处理的)二氧化硅布的酚醛粘合剂 |
带(在900K处理的)二氧化硅布的有机硅粘合剂(K-4) |
带(在900K处理的)二氧化硅布的酚醛粘合剂环氧树脂(ЭД1-10) |
带石棉布的酚甲醛粘合剂 |
密度,1·10-3kg/m3 |
1.48 |
1.50 |
1.63 |
1.60 |
在20℃下的导热系数,W/m.K |
0.27 |
0.26 |
0.37 |
0.4 |
在20℃下的比热,kJ/kg.K |
1.05 |
0.88 |
1.10 |
1.15 |
表5.2、 布酚醛树脂热防护层
性能 |
碳布酚醛树脂 |
石英布酚醛树脂 |
密度,1·10-3kg/m3 |
1.40 |
1.6 |
压缩强度,1×10-9Pa |
0.17 |
0.16 |
弯曲强度,1×10-9Pa |
0.17 |
0.14 |
弯曲弹性模量,1×10-9Pa |
0.014 |
0.02 |
抗剪强度,1×10-9Pa |
0.025 |
– |
在93℃下的导热系数,W/(m.K) |
0.12 |
– |
在66℃下的导热系数,W/(m.K) |
0.16 |
– |
在℃下的比热, 1×10-3J/(kg.K) |
1.21 |
– |
树脂含量,% |
– |
30 |
对于SRM外表面的热防护来说,采用几种类型的材料;用在体积玻璃纤维布基上喷涂和涂层方法所涂的无机填料环氧树脂基薄层材料得到了最大应用。在这种情况下,对于在迎面气流绝热恢复温度不超过1500…2000K的条件下采用第一种类型涂层,在超过2000K温度条件下采用第二种类型的涂层。
此外,在美国采用《Инсульк(英苏里克)2755》软木涂层作为外热防护材料。
在燃烧室内表面涂热防护层
在壳体内表面涂绝热层可用机械化(喷涂粉末、离心喷涂膏剂)或手动(铺片、覆盖颗粒层))方法实施。喷涂过程如下。在喷涂热防护材料之前,在喷砂装置上清理零件的内表面,然后用溶剂对所清理的内表面进行化学清洗,涂抹胶,进行铺放(固化或未固化的)热防护材料片。在采用固化材料的情况下,将制品在室温条件下加小压力置放一定的时间。涂抹预固化的热防护层就能够制作严格公差的复杂型面,消除在成型过程中热处理时所产生的内部应力。在采用未固化材料的情况下,用保温箱在413…435K温度下加0.8…1压力对材料进行热处理一定的时间。采用安装在支承装置花盘上的金属筒形式的专用型架来形成压力。在金属筒上套有用来将压力传递到热防护层的橡胶袋。
热防护层的固化保温箱是一个包括工作容积、带风机系统的加热器、温度过程控制仪器、液压真空系统的结构。热处理结束后,对成品的热防护层进行检验。检验可用验证试件,也可在制品上(破坏和无损方法)进行。用验证试件检测物理力学性能、固化度、密度。由制品直接检测胶合质量(粘附性)、几何尺寸、硬度和根据硬度的固化充分性。
热防护层、防护固定层对金属的粘附质量用超声波仪器测定。为了实施检验,应制作标准样件,在该标准样件上应完全重复热防护层和防护固定层的铺放方式和零件的形状。此外,必要时,粘附质量用热防护层和防护固定层与制品金属表面直接剥离测定。同时测定实际粘附强度。
喷管的抗蚀涂层
固体火箭方发动机喷管工作条件对这个部件的防护层提出了硬性的和多方面的要求。喷管构件材料的选择取决于两个主要因素:在发动机工作时温度沿喷管的分布,燃烧产物的化学和侵蚀作用。SRM喷管的材料应拥有在达3500K温度下的耐热性和耐热强度;足够的结构强度;在饱和固体粒子的高温超音速流中的抗蚀性;最小质量;与周围介质和内部介质的相容性。
相当轻的喷管只有在喷管结构中使用多层性原理方可得到,在结构的每一单层履行严格确定的功能时,在喷管性能良好的条件下整个装配件整体就会保障功能。
按功能和配置位置,喷管装置的零件可分为几类:头帽、输入锥、喷管嵌入块衬套、喷管嵌入块增强件、输出锥、扩散段。
作为喷管装置材料在SRM中得到了最广泛普及的是难熔金属及其合金—对于喉部截面嵌入块,增强塑料—对于大型SRM,增强塑料—对于输入锥体、输出锥体和扩散段。
制作SRM喷管嵌入块材料的选择取决于零件在发动机中的用途和工作条件。嵌入块的用途或者是保障喷管最小截面直径值的稳定性,或者是在固体推进剂燃烧产物化学活性两相流对零件作用条件下保障给定的直径变化规律。
对嵌入块材料提出高热强度、高耐热性和高抗蚀性的要求。在表5.3中列出主要类型的材料。作为喉部截面尺寸小(约300mm)的SRM喷管嵌入块材料,石墨和耐热金属—钼和钨(多半是专门处理的)正在得到很大的应用。譬如说,《北极星A-1》中程弹道导弹SRM喷管嵌入块用钼制作(用锻造,用使壁变薄的旋压方法),而《民兵》洲际导弹其中一级的SRM喷管拥有高密度石墨的嵌入块。
为了防护喷管嵌入块,在其工作面用某一方式涂有特种涂层。石墨嵌入块最普及的涂层是钨及其合金、碳化钨、钼及其合金、氧化铝、氧化钽和其它一些金属氧化物、特种石墨陶瓷涂层(组成如下的涂层类型:50%石墨、25%硼化钛、24%二硅化钼、1%特种粘合剂)、热解石墨等。
表5.3、 在T=293K条件下喷管材料的典型性能
性能 |
导热耐热材料 |
||||
石墨ATJ |
钨(锻制的) |
热解石墨 |
|||
密度,g/cm3 |
1.73 |
19.0 |
1.80…2.26* |
||
导热系数,W/(m2.K) 顺着纤维或经纱层 横着纤维或经纱层 |
104…23.7* 59.4…22.3* |
142.5…89.1* – |
142.5…89.1* 1.78…0.45* |
||
比热, J/(kg.K) |
0.25…0.6** |
0.033…0.047** |
0.22…0.5** |
||
温度系数, K-1.106 顺着纤维或经纱层 横着纤维或经纱层 |
2.7 4.0 |
4.5 – |
2.4 36 |
||
性能 |
烧蚀复合材料 |
||||
碳布MX-4926 |
石墨布FM-5064 |
石英布MX-2600 |
|||
密度,g/cm3 |
1.43 |
1.45 |
1.75 |
||
导热系数,W/(m2.K) 顺着纤维或经纱层 横着纤维或经纱层 |
1.23…1.38*** 0.71…0.86*** |
3.40…4.31*** 1.02…1.36*** |
0.52…0.56*** 0.45…0.48*** |
||
比热,J/(kg.K) |
0.20…0.36*** |
0.24…0.39*** |
0.24…0.30*** |
||
温度系数, K-1.106 顺着纤维或经纱层 横着纤维或经纱层 |
6.7 9.5…55.8*** |
9.5 31.7 |
7.0 29.7 |
||
*最小值相对应的是温度2473K
**最大值相对应的是温度2473K
***最大值相对应的是温度673K
有时,取代在石墨上喷镀防护层,对表层进行得到所谓超级石墨结构的再结晶、对零件进行以在工作表面得到碳化钛、碳化锆等高耐热层为目的的特种处理、进行结果是在零件表层形成石墨与碳化硅键合结构的硅化处理就足够了。
保障石墨嵌入块侵蚀防护很有效的方式是在其工作表面喷镀钨防护层。(对于喷镀防护层和对于用气态热解沉积直接制作嵌入块来说)镀层可用气焰或等离子喷镀、电解沉积、真空烧结喷镀。
热解石墨也属于SRM喷管嵌入块所采用的材料。热解石墨的生成过程是含碳气体高温热分解和游离碳沉积在工业用的石墨芯模上。热解石墨就是晶体定向的石墨。
对热解石墨的兴趣的原因是其导热性特殊的各向异性:在薄层中可实现达2000K的温度差。应当注意到热解石墨一系列使难于在真实结构中实际使用这种材料的实质缺陷。应属于这些缺陷的首先是脆性、与喷管结构所使用的其它材料连接强度低、存放过程中趋于分层。
对于喷管扩散段及其构件制作来说,玻璃塑料材料作为热防护材料和结构材料正在得到广泛应用。玻璃纤维增强塑料的导热性为不锈钢导热性的1/80。为了制作玻璃纤维,采用不同牌号的玻璃:不含硼的铝镁玻璃,或《碱》玻璃,铝硼硅玻璃,或不含碱的,碱金属氧化物含量不超过2%的玻璃,氧化硅含量100%的石英玻璃和氧化硅含量为96…98%的氧化硅玻璃。
氧化硅纤维和石英纤维在达1370…1770K温度都不会失去自己的性能,也就是说,比不含碱的铝硼硅玻璃纤维的使用温度高500…600K,这是由它们的2020…2070K高熔化温度所决定的。
与其它树脂结合的改性树脂和环氧树脂作为用玻璃纤维增强塑料制作SRM结构的粘合剂得到了最大应用。
研究得最好的是酚醛树脂。这些树脂具有良好的化学稳定性、力学强度、良好的介电性能、低成本和加压浇灌再处理能力。与其它类型树脂相比,酚醛树脂由于能在高温下生成高强焦炭而得到最多的应用。缺陷是它们的脆性高。
环氧粘合剂的强度高、粘附性和化学稳定性好、吸水率很低、收缩量小。环氧树脂的一般使用局限于420K温度。改性的环氧粘合剂,特别是那些含有酚基的环氧粘合剂适用于在较高温度条件下使用。使用可溶型酚醛树脂作为固化剂会提高环氧树脂的耐热性和耐火性。
有机硅树脂的特点是耐热性好、力学性能高并具有在420…470K温度条件下长时间使用,而在达570K温度条件下短时使用的能力。
预浸布带用普通的织物组织带或布制作并用来与气流平行铺层缠绕热防护层。
在交叉带中玻璃纤维与带的方向成角度(通常是45º)配置。交叉带用来与气流垂直或成一定角度铺层缠绕电力驱动零件。交叉带用沿交叉铺放单向带层的玻璃布对角线裁剪并随后剪成所需宽度的交叉带制作。
扩张角不超过30º的扩散段用环向缠绕,也就是说,用在具有与未来扩散段内型面相同外型面的芯模上与旋转轴平行铺布带制作。
缠绕按下列方式进行:布纱器上的布带被铺在芯模的旋回圆筒上并然后根据铺放角度以一定的间距螺旋缠绕到芯模的可拆卸环上,在停止输送时在可拆卸环上缠绕所需加厚部分。缠绕结束后,将毛坯件在液压釜中在取决于材料牌号的一定温度和压力条件下固化。然后将固化的毛坯件从芯模上取下,在外表面和端面机加并粘入金属壳体中。
在完全用玻璃纤维增强塑料制作扩散段时,起先缠绕抗蚀层,随后在液压釜中对毛坯件固化并机加。然后,根据芯模的几何形状和尺寸,与轴线成0…30º范围内的不同角度按照测地线用单向带缠绕承力层。玻璃纤维带的铺放角度可逐层或经过几层后变化。遵照强度和数量所有要求缠绕扩散段承力层的基本条件是按测地线铺放布带。
为了缠绕在喷管喉部截面工作的零件,采用交叉布带,交叉布带的结构使有可能与零件轴线成约90º角度进行铺放布带。通常是在芯模垂直安置的旋转型缠绕机上用交叉布带进行缠绕零件。交叉布带通过布纱器时在升高的温度下变软并从一端拉伸,而然后绕芯模或与旋转轴成某一角度铺放在水平面上。
缠绕后,对零件毛坯件在压力达7MPa液压釜中进行热处理。
难熔材料
象钨、钼、钽和它们的合金这类难熔金属在现代SRM中得到了广泛应用。
钼:钼的较低密度、高导热性和高比热使有可能采用其来制作SRM喷管装置中的护面层。几乎所有的钼零件都是用锻造制作。研究表明了钼的相对抗蚀性和抗含有铝的固体推进剂燃烧产物化学作用性。但是,必须注意到,在钼表面温度约为2320…2370K时,氧化介质对钼表面的作用会使钼氧化。在2420…2470K温度条件下会生成被大速度燃气流可冲刷得易熔共晶体Mo—MoO2。在固体燃烧产物不使钼氧化的情况下,钼的功能范围取决于接近其熔化温度的温度。在钼加入钨元素时就可提高钼的熔化温度和热强度。
钼的一些性能在表5.4中列出。
表5.4、 某些难熔金属的性能
性能 |
Mo |
Ta |
W |
熔化温度,K |
2890 |
3269 |
3680 |
在290…2000K范围的温度系数,K-1 |
6.7 |
7.7 |
5.10 |
在下列温度下的导热系数,W/(m2.K) 290K 1000K 1500K 2000K 2500K |
136 113 94 78 70 |
62 71 76 80 98 |
156 110 104 98 95 |
在下列温度下的拉伸强度极限,MPa 290K 1000K 1500K 2000K 2500K |
670/260 450/120 170/60 43/25 7 |
500 190 85 35 14 |
1500/300 800/180 350/100 140/60 45/35 |
密度,kg/m3 |
10200 |
16600 |
19200 |
钽:钽的熔化温度比钼高,但是,在高温下钽会与水蒸气、氧化碳、盐酸相互作用。钽与钨的合金是较稳定的。钽的一些性能在表5.4中列出。
钨:由于目前已将现代高能推进剂燃烧温度提高到3500K,钨广泛应用于喷管装置热应力最大的结构件。譬如,用钨制作了《民兵》和《北极星》导弹的喷管嵌入块。
钨的抗蚀性最高、抗化学作用强度相当高。钨的很重要性能是熔化温度高、抗热冲击作用、在高温下比强度最大。实质的缺陷是密度大。
在使用钨时,必须注意到,在大多数情况下,材料的烧蚀可能远在零件内表面达到决定材料物理状态变化的熔化或蒸发温度之前就已开始。固体推进剂燃烧时喉部截面钼的明显烧蚀(在推进剂燃烧产物具有对钨的氧化能力的条件下)在表面温度为1970K时就已经开始。
在采用燃烧产物组成中有氧化铝Al2O3凝聚粒子的固体推进剂时,凝聚粒子起初落入到嵌入块防护层较冷的表面,在壁上沉积形成防护嵌入块材料的层。Al2O3微导热层厚度的进一步增大会将嵌入块表面加热到决定Al2O3氧化物熔化的温度2323…2370K。从这一时刻起所沉积的层烧蚀就会加剧,直到钨露出。
如果固体推进剂燃烧产物不使钨氧化或使钨微氧化,那么,就可将钨的功能保障到较高温度。如果固体推进剂燃烧产物对钨有大的氧化能力,那么,钨就开始氧化和烧毁。
石墨是SRM喷管热应力构件最普及的材料。石墨拥有高升华温度、高导热性、足够的强度,特别是在高温条件下,拥有足够高的耐蚀性和抗侵蚀性[58]。
有许多种工业石墨,其中多晶体(密实)石墨、硅化石墨和热解石墨最广泛应用于制作喷管构件。多晶体石墨由用粘合基体结合的石墨晶体构成。各种多晶体石墨具有1.6…2.0·103 kg/m3。密度大1.9…2.0·103 kg/m3的石墨特点是抗蚀性相当高。也广泛使用硅化石墨,其高抗蚀性是由组分(碳化硅和石墨)高分解温度、足够的强度、良好的导热性、低热膨胀系数所决定的。原料的不缺乏、较简单的硅化工艺都有助于使用其来制作SRM的喷管装置。硅化石墨的基本性能用表5.5表示。
表5.5、 石墨的性能
性能 |
热解石墨 |
石墨 |
密度,1·10-3kg/m3 |
2.2…2.23 |
1.6…2.0 |
比热,1×10-3J/kg.K |
0.971 |
0.712 |
导热系数,W/m.K 顺着薄板 垂直于薄板表面 |
372 3.59 |
|
在20℃下的强度极限, 1×1-09Pa |
0.103…0.137 |
0.014…0.028 |
在下列温度下的比强度,1×10-6Pa.m3/kg.290K 2970K |
0.47…0.62 1.7 |
0.09…0.14 |
热解石墨得到越来越多注意。这种材料的密度与纯石墨的理论密度一致(2200kg/m3)。晶粒的高定向度决定着最大的各向异性,这对于高温条件下的喷管嵌入块材料来说是特别重要的。热解石墨在晶粒定向方向的导热性可能比垂直方向高两个阶。晶粒分布平面中的强度也比一般种类的石墨强度高得多。
除高升华温度外,将良好的高温力学性能、可接受的抗蚀性、导热性的各向异性结合,就使有可能将热解石墨看作是给以希望的材料,这种材料原则上允许制作功能达3500K温度的喷管喉部截面嵌入块。
在研究石墨材料时,必须注意到,在喷管装置条件下,石墨(其中包括硅化石墨)的特点是质量烧蚀相当大,从2070…2170K温度就开始烧蚀。由于吸湿度差,Al2O3保护层在石墨上的沉积不如在金属上的沉积急剧。
质量烧蚀额定的材料
增强塑料较之其它材料拥有低导热性、在很宽几何尺寸范围内制作喷管构件的可能性和在其破坏时吸收大量热能的能力这样一些重要的优点[3,11]。
在大型SRM结构中,增强塑料取代难熔金属和石墨也用作喉部截面的主要热防护。当用填料纤维定向所保障的侵蚀速度比较小(\({{\omega }_{yh}}\le 0.2…0.3mm/s\))的增强塑料出现时,这就成为了可能。譬如,碳石墨塑料(在塑料中一定部分的纤维与燃气流方向垂直定向)具有小于大约0.1mm/s侵蚀速度。由于在固体推进剂高动力特性条件下,无附加防护要保障喉部截面无烧毁工作实际上是不可能的,问题的最简单解决就是采用质量烧蚀额定的喷管(特别是对于大型SRM来说)。在这种情况下,给定的推力变化程序用与由于质量烧蚀而发生的喷管喉部截面面积额定变化相协调的推进剂装药燃面随时间的变化来保障。
在这种情况下,主要的任务是要查明影响质量烧蚀线性速度变化的因素,并尽可能简单数学描述烧蚀过程。
目前,SRM大型喷管燃气通道的所有构件通常用增强塑料制作(例如,《钛-3Ц》火箭的SRM喷管装置)。
增强塑料在填料和粘合剂的成分、制作工艺和性能方面可有多种多样。
在一次逼近中,可将所有增强塑料分成两类:碳石墨布基增强塑料、玻璃和二氧化硅纤维基增强塑料。
一系列增强塑料的基本性能用表5.2表示。
第六章:固体推进剂装药的强度计算
本章提供了关于评估固体推进剂装药强度的方法的基本信息。从各种各样的固体推进剂装药结构中,选出了最常见的与壳体固定的通道翼槽式圆柱装药构型作为分析应力变形状态的典型例子。此外,在这里,研究了固体推进剂的物理-力学性能的特点。
第七章:SRM特种构件的设计
本章主要介绍:点火器、推力的调节方式、推力的调节装置。
第八章:SRM结构的工艺性
工艺性的保障问题由设计师在设计过程的所有阶段解决。实际上,在设计工作中,完全缺乏关于结构工艺性的材料是严重的失误。《结构的工艺性》名称本身指明,在这一章节中研究直接在产品研制过程中结构工艺质量的保障问题。
与研究材料和产品加工工艺过程实质的工艺章节不同,在结构工艺性章节中研究的是关于几何形状和尺寸以及相互连接、配置和装配方式是如何进一步影响到产品制作的材料用量、劳动量、时间和成本的问题。因此,如果加工的工艺规程由工艺师编制,那么,工艺性的保障问题就由设计师解决并在设计文件中得到反映。
研制技术经济最佳的结构没有其工艺性的保障是不可思议的。按照全苏国家标准14.202-73和全苏国家标准14.204-73,工艺性的保障是在产品研制阶段、制作工艺准备阶段、使用阶段和修理中,在同时缩短时间和减少资金情况下,提高生产效率,而不降低产品的质量。
提高工艺性是设计过程最重要的组成部分之一,因此,设计师应拥有结构工艺性主要问题的相应建议。
结构的工艺性优化修整是从制定草图设计和工作设计到试验件制作和发动机批生产的连续过程。
在设计和试验修整产品并保障其工艺性时,应遵循下列要求:
1、结构的工艺性取决于产量规模和生产的类型(批量生产,大批量生产,小批量生产,试验批量,单件生产)。一种产量和批量规模的高工艺结构对于另一种产量规模来说可能是工艺性不好的。在从单件生产和试生产转变为大批量和批量生产时,结构可能会受到根本改变。
2、工艺性应相对于整个产品来研究。不能研究单独零件或装配单位的工艺性问题,而不考虑其对整个产品工艺性的影响。
3、工艺性应考虑到从零件毛坯件制作开始到以成品产品装配和试验结束的生产工艺过程所有阶段的相互影响以及考虑到安全技术的要求来研究。
4、工艺性应考虑到使用标准的、规格化的、借用的零件、外购件和装配单位的可能性、工艺过程的统一化以及试制和批生产制造厂的特点来研究。例如,正如以前所提到的那样,研究[72]表明,在大型SRM中采用5%的未调试好的工艺过程就会使研制时间增加50%,成本大致也增大50%。
5、工艺性也包括主要决定产品再生产的稳定性和产品质量的设计文件编制的一致性。
结构工艺性指标的选择规则及其定性和定量评估由相应的标准确定。归根结底,所有的规则都归结为评估所研究的零件、装配单位或产品不同结构方案的劳动量和材料用量。
下面,仅研究能反映SRM零件和装配单位特点的一些问题,了解它们不管是在制定初步结构方案过程中,还是发动机所有的随后研制阶段上都是必需的。
对于与拟在飞行器中采用的大多数产品一样的SRM来说,特有的是批量较小,这并不总是允许采用高效率特种设备。
这种情形使SRM结构的工艺性保障问题更加复杂,并要求研制人员了解在SRM生产中先进的工艺过程的采用特点。
8.1、结构材料的应用特点
在高可靠性条件下,保障SRM结构最小质量的要求迫使采用,例如,象强度极限超过1.8GPa的钢,高强钛合金,钼、钨、铌基合金这类高强和耐热材料。所有这些材料是难于变形的,并不好机加。因此,列入提高发动机工艺性的有效措施之列的有减少所采用材料的目录、简化零件的几何形状、最大减少点状孔、螺纹孔和铣削面的数量和目录。应尽可能排除深拉延制作的零件。为了简化对孔和复杂表面的机加,应规定用高频电流对所加工区域局部回火。结构工艺统一化和标准化也是提高SRM工艺性的有效方向。
提高SRM工艺性的最有效方向是用非金属纤维复合材料(玻璃纤维增强塑料、邮寄纤维增强塑料、碳纤维增强塑料)替换金属。
8.2、SRM圆壳形和微锥形金属壳体的制作特点
结构工艺性的要求取决于在研制期间科学技术进步的水平,并随着时间变化。例如,在出现板厚度公差范围很小的高质量冷轧板前,以及在出现象电子束焊接和激光焊接这类能保障得到高质量焊缝的焊接方式前,旋压(碾压)方法使有可能得到了质量更好的、更可靠的和具有最小质量的无缝外壳。我们来较详细研究这些方法。
壳体外壳的旋压。在作出关于采用旋压外壳合理性决定前,设计师应弄清楚,工业是否生产力学性能和厚度公差不次于碾压时所得到的这些性能的板。如果外壳的计算厚度大得需要热轧板来制作它,那么,应当较详细研究这些板的性能。
大厚度的热轧板具有一系列不足:
- a) 板的厚度公差相当大并不均匀。众所周知,结构的强度根据板的最小厚度计算,而质量根据板的最大厚度计算。因此,这个不足就造成发动机质量效率逼迫下降;
- b) 有导致焊接边缘对接过程复杂化并使得必须排除焊缝区变形和保障外壳空气动力规则几何形状的翘曲和凹凸不平。此外,不规则的几何形状会导致热防护层消极质量和剩余推进剂增大;
- c) 有很难用已知检测方法发现的冶金缺陷(表面上的氧化皮,卷裹在板厚度中的氧化皮,板厚度中形状不同的分层);
- d) 用板沿母线或螺旋线焊接制作外壳的必要性。在质量不好的材料中焊缝的存在会降低可靠性,这就要求增大安全系数,进而增大外壳的质量。在这些情况下,采用无缝外壳是合理的。无缝外壳可用机加、冲压-拉伸、热挤压、冷旋压和冷轧(碾压)制作。
由于劳动量、保障厚度和其它参数的硬性公差的复杂性,不建议采用机加。此外,在机加过程中会切断材料的纤维,这就导致外壳强度性能和使用性能降低。
应列入无缝外壳制作的更具工艺性的方法是用深拉延制作小直径(约500mm)铝外壳和用碾压制作钢外壳。碾压使有可能制作恒定壁厚、变壁厚和阶梯壁厚的外壳(其中包括过渡到法兰的外壳)。
冷碾压(旋压)这是使固定在旋转芯模上的环形毛坯件冷局部变形的过程。
碾压在独特的碾压机上进行。为了得到毛坯件高度变形的大型外壳,需要大功率的碾压机。它们是昂贵的并在具有大跨度和吊车轨道高度的专用车间厂房内占据相当大的生产面积。因此,旋压外壳的选择应考虑到专用设备的具备、它的利用率和旋压毛坯件材料的利用率。
8.3、壳体外壳的焊接
用来制作SRM壳体的钢具有高强度、足够的塑性、弯曲角、较低的价格。但是,在焊接这种钢时,会产生一系列与其中碳含量增大相关的困难(钢的强度增大,但是,钢的焊接性恶化)。
高强钢的不足是它们对力学特性、扩散特性或腐蚀特性的表面各种各样损伤形式的应力集中点敏感性高,其后果是产品过早脆性破坏。焊接连接最普通的应力集中点可为气孔、未焊透、咬边、非金属夹杂等。因此,为了得到高质量焊接连接,应采用高纯度焊接材料和专门的焊接工艺方法。
用不熔化焊条在惰性气体(氩气或氦气)介质中制作厚度为1.5…6mm的高强薄钢板焊接结构不总是会保障与基材相同的焊接连接强度。列入这个工艺的缺陷有在焊缝中金属结晶过程条件不利,并在热影响区形成薄弱区和过热,因而有焊缝和热影响区的强度降低。
为了得到与基材强度相同的焊接连接,将所焊接坡口加厚,或者采用螺旋焊缝。这些方法会增加结构成本并使得结构质量增大。
采用焊条横向摆动的高强钢焊接工艺实际上会保障焊接连接和基材的强度相同。
在制作SRM焊接零件和装配单位实践中,氩弧和氩-氦弧焊接、助熔剂层电弧焊接和电渣焊(用来焊接厚壁外壳和专用工装-缠绕玻璃纤维增强塑料壳体用的芯模,用来焊接装药成型工装)得到了普及。电子束焊接和用激光束焊接是很有前景的。
在氩弧和氩-氦电弧焊接时,保护气体以沿焊条通过并包围它的射流引入电弧区。射流防止焊缝熔体生成氧化物。方法的优点是生产效率相当高、焊缝质量好、没有必要用其他手段保护焊缝(没有焊剂,也没有焊渣)、灵活性(小质量的焊机头使有可能使焊接机械化)、通用性(适用于焊接许多金属)等[69]。
在助熔剂层电弧焊接时,金属焊条与所焊接外壳之间的电弧在熔化的熔剂层下燃烧,熔化的熔剂在金属熔体表面形成防金属受空气有害作用的渣覆盖层。熔剂所防护的熔化金属冷却缓慢,这就对于焊缝成型创造了良好的条件,大部分渣和气体从焊缝中来得及排出。这个方法使有可能使过程自动化,将焊接结构的制作转为流水作业。
在电子束焊接时,轰击连接处的快速移动电子能熔化零件的焊接边金属。过程在真空室或充满惰性气体的室中进行。得到的焊缝很窄并结实,不需要附加处理。特别是对于大型零件来说,采用这种焊接形式应全面论证,因为,大型焊接装置是唯一的,并使用相当复杂。
所列举出的所有焊接形式中最有前景的是激光束焊接。量子发生器(激光)所发射出的巨大能量密度的光束是一种比电子束还更强大、更细小和更灵活的介质。激光焊接装置使用也比电子束焊接使用简单。激光束比电子束要灵活得多。可借助镜面将其折射,这就使有可能既可达到放置远的零件,也可同时达到几个焊接工位。目前,功率大于2kW激光焊接装置的主要不足被认为是由电能、冷却水、更新通道中气体和保护气体的稀有氦气消耗大造成的它们的高成本和高使用成本。
在研制SRM焊接壳体时,必须考虑到一系列建议。
1、在设计SRM焊接结构件时,应遵循在设计加载高内压的容器时所采用的原则。其中主要的是不允许相当大的应力集中,特别是在焊接部位。
2、外壳焊接的最好焊缝是螺旋焊缝。螺旋角应至少与外壳母线成55。螺旋角根据如下条件测定:
\({{\sigma }_{s}}=\frac{{{\text{p}}_{\text{c}}}D}{4\delta }\left( 1+{{\cos }^{2}}\alpha \right)\)
式中δ—外壳的壁厚;α—螺旋线与外壳母线之间的夹角(图8.1)。
图8.1、螺旋焊缝的外壳示意图 图8.2、连续螺旋焊缝的外壳焊接机
(α≥55~60°) 示意图:1—扇形齿条装置;2—滚轮;
3—辊;4—机械进给部件;5—球星支座;
6—托架部件;7—滚轮支座;8—焊机头。
3、优质马氏体时效不锈钢外壳可按照在用钢带生产焊接管中所采用的方式制作(图8.2)。在这种情况下,焊接连接可用三种方案中的一种得到:焊接热硬化状态钢带、焊接热硬化状态钢带并随后时效、焊接未热硬化的钢带并随后对焊缝热硬化和感应软化。
用这个方法制作的外壳的材料利用率具有很高和制作劳动量很小(在过程自动化条件下)。这个方法很有前景,还是因为在采用它时,可使用用焊接螺旋焊缝的激光束预先加以热力学处理到2…3GPa强度极限的钢带来制作外壳。
4、如果对外壳焊上某种零件,那么,必须达到尽可能的平稳增大结构的刚度(图8.3)。焊接处的零件厚度建议规定小于外壳的壁厚。
图8.4所示为管接头与壳体外壳或封头合理焊接的实例。
焊接时的工艺缺陷及其对结构强度的影响
为了制作SRM壳体,采用了两种高强钢—这就是中合金高碳钢和马氏体时效钢。这些钢的硬化机理是不同的,但是,这两种都具有一系列所有高强材料共同的性能。属于这类性能的有对应力集中敏感性高和力学性能变化取决于决定钢强度的元素的化学成分和有害杂质的变化;取决于由再处理过程中金属变形方向所引起的性能不均匀性;取决于表面和内部应力集中;取决于在应力状态与不同介质的接触。
图8.3、焊接在外壳上的支座示意图 图8.4、所焊接上的管接头示意图
焊缝的金属具有对钢所列出的所有缺陷,而且还由于焊缝具有铸造粗晶结构而加重。因此,在选择焊接形式时,必须了解各种不同形式焊接特有的焊缝结晶方向、热影响区和焊缝根部及其正面成型区的状态和大小。引起结构转变和相变的焊缝冷却时金属体积的变化以及对金属近焊缝区的温度作用都会导致焊接连接变形,因而导致出现焊接结构几何尺寸失真和形状变形,这些失真和变形会使焊接连接区中的应力增大超过计算值的。
在选择焊接制度,选择焊接方式和工艺装备方面的工艺过程应调试得使工艺缺陷出现微乎其微。检验方法应以最大可靠性查明焊缝中所有不允许的缺陷。
在SRM高强钢(WЛ1Cu, SiP43,WCoSi-1等)壳体焊接过程中,可能会出现降低结构强度的工艺缺陷:孔泡、气孔、裂纹、未焊透、钨夹杂、咬边、坡口错位和近焊缝区翘曲。
气孔率。气孔的产生是由液体金属中气体形成所造成的。在结晶期,在碳素钢中发生过饱和碳和氧化亚铁,由于它们的相互作用就生成氧化碳。钢中不溶解的氧化碳形成气泡胚。氢也有助于形成气孔。氢在所有实际技术装备中采用的金属中溶解并生成填隙熔体。氢进入不致密处,增大它们的尺寸并转化为气泡。氮气也有助于气孔产生。
在焊缝截面中气孔数量达到与横向截面减小接近5%相符的量级情况下,就可看到结构强度明显降低。
未焊透—基体金属坡口与焊缝金属熔化不够或完全没有熔化,这是经常遇到的焊接结构的缺陷。它可能是焊接电流值小、焊条相对焊接接头引导不精确、焊接速度过高、零件焊接准备质量低的后果。未焊透是一个在底部半径在0.01…0.1mm范围内的V形自然凹口。在外部力作用下的未焊透区中,可能产生弹性区应力高度集中和超过材料弹性极限的局部塑性变形集中。未焊透区中变形的集中和局部塑性的降低是焊接对接连接变形性能的指标。未焊透会显著降低结构的静态强度和动态强度。
钨夹杂。在焊接高强钢时,都采用钨焊条。在用钨焊条焊接时,在电流强度与钨焊条直径不相符的情况下,小块钨可能会掉入焊缝的金属中;采用制作质量不高的焊条(有分层、有不密实性、有裂纹);发生钨焊条与焊缝金属接触。
在横向截面面积由于钨夹杂而减小超过5%的情况下,就会发生焊接连接的强度明显降低。
坡口错位—焊接连接最常见的缺陷之一。坡口错位是由于焊接零件制作不精确、电弧对所焊接坡口的热作用和焊接的不精确而出现。
在坡口错位时,可观察到在静态负载时表现出来的力学性能变化。在动态负载时,焊接连接的强度极限随着坡口错位增大而减小。在零件坡口相互错位超过材料厚度的30%情况下,由于坡口错位就可看到焊接连接的力学性能明显降低。
8.4、可机加零件的工艺性
大型SRM的低刚度和在焊接和热处理时所产生的它们几何形状变形使得难以得到较高的机加精度。壳体几何尺寸的高精度要求由发动机不同构件在火箭中的相互配置精度的要求、密封性要求以及保障互换性要求和壳体与成型推进剂装药的工装装配条件所决定。
如果规定用高频电流对可机加的部位局部回火,用强度为2GPa左右的材料制作的法兰的机加工艺性就会实质性地提高。
在没有结构质量硬性限制的条件下,在大批量制作中的SRM外形尺寸比较小(直径500mm以下)的情况下,把封头与壳体和喷管与封头或壳体的螺栓连接换成螺纹连接、键槽连接或楔形连接可实质性提高工艺性。
对尺寸精度和表面加工光洁度的过高要求不仅由于制作的劳动量增大,而且还因为工具寿命缩短和标准产品的无理由报废,都会降低结构的工艺性。
8.5、金属用量和材料利用率
在一些机械制造领域中,在设计阶段就形成达85%的材料消耗。应当考虑到,在设计中考虑不周的事经常是很难的,而且有时,由于对技术设备根本改造的必要性、时间的不足和相当大的花费,在生产中改正是不可能的。结构的完善就使有可能减少约20%的材料消耗[67]。因此,与考虑和评估产品其它重要性能的同时,材料用量和材料利用率的问题都应在设计的技术经济优化阶段考虑和评估。
在设计SRM时,材料用量的减少通过纤维复合材料替换金属、采用比强度最大的和比刚度最大的结构金属(在假设结构安全系数最小时)和提高材料利用率来实施。
在设计时,提高材料利用率主要是依靠研制使有可能采用经济毛坯件:壳体和封头法兰所用的压制焊接型材、有不可机加表面的精密铸造和冲压、用板冲压并不用随后机加的毛坯件等来达到。合理的将结构分解成必须以高工艺性单独制作,然后组合成装配单位的构件也是提高材料利用率的很有效方向。
我们来研究几个合理分解的示例。如果在法兰或中部卡带上应有吊耳,合理的是单独制作它并随后焊接在壳体上(见图8.3)。这就使有可能利用取消滚铣提高工艺性并同时提高材料利用率。
不建议采用由锻件和冲压件车削得到的封头(图8.5)。这种结构的制作劳动量大(特别是在由钛合金制作封头时),而这种结构的材料利用率很少超过0.1…0.15。合理的是将封头分解成单独构件。图8.5,б表明,球形段3可用冲压板毛坯件制作;锥形过渡段4可用板焊接制作(型面可在型材弯曲压力机上完成并随后用滚轮卷起);结构有些变化的法兰1和加强环2可由机加余量很小的经济性压制型材焊接而成。在这种分解情况下,制作的劳动量就会减少一半以上,金属利用率会从0.12增大到0.7。通过在焊接前引入零件型面预先变形和尺寸预先偏差,就使有可能在焊接和焊缝收缩过程后得到满意的封头型面,并避免小型封头特有的焊缝区出现较大翘曲。
图8.5、SRM后封头:а—由整体毛坯件车削的后封头;б—由分解成构件制作的后封头
车削的大型封头工艺性特别不好并材料利用率值低。
在图8.6,a上虚线所示为具有嵌入到燃烧室中部分和后凸法兰的喷管封头冲压毛坯件外形。封头具有大直径的孔。在制作劳动量很大的条件下,采用整体冲压毛坯件情况时的材料利用率不超过0.13。在图8.6,б所示的部位采用附加焊缝和螺纹钎焊(或者只是钎焊)连接就能够采用较经济的毛坯件:法兰3的热轧环形毛坯件(由相同毛坯件制作的两个零件);封头本体1用的加厚冲压件;法兰2的热轧(或焊接)环形毛坯件。
图8.6、SRM喷管构件:a—由整体毛坯件制作的构件;б—由分解成构件制作的结构件;1,2,3—分解喷管的零件
这种分解使有可能将材料利用率增大到0.6,并几乎将劳动量减少一半。同时,当在部件中只是机加配合面和孔时,封头的图纸应规定这种工艺。
应当注意到,在单独制作首批试验件的初步阶段,大的劳动量和低的材料利用率可能在经济上是有理由的。在试验研制阶段,由于试验结果不满意,可要求在短期内对结构根本性改变并随后对其试验。制作复杂的和昂贵的工装可能需要比用不经济毛坯件制作零件多得多的费用。此外,办理订货单、制作工装和制作经济毛坯件所需的时间使得产品试验修整的周期大大增加。
因此,结构的高工艺性特点是制作的劳动量小、材料利用率高、没有难以解决的问题、能够在合理分解复杂结构基础上组织短的制作生产周期、能够采用可批量制作的设备、能够采用在高度统一化、标准化和规格化基础上的协作、合理选择分解方式、所选牌号的材料工艺性好和数量最小、工艺装备的花费水平低、可达到的精度级和其它简化零件制作的因素程度低。
第九章:SRM程序化设计系统的特点
SRM的设计应从研究技术任务书开始。
在设计过程中不是总是都会成功保障满足技术任务书的所有要求。在用逐次逼近方法的SRM草图设计阶段,通常在采用折衷方案时会找到最佳的参数。
SRM参数的优化所指的是旨在保障发动机结构的最小重量,同时保持技术任务书给定范围内所有其余特性(动力特性、使用特性、经济特性等)不变的设计过程。
研制符合技术任务书现代要求的SRM,必须要先详细、深入和全面仔细研究设计方案。不采用程序化设计系统*(*有时采用机器设计系统或设计程序化系统的名称来取代程序化设计系统)来制定现代SRM的最佳设计方案不仅变得费力、昂贵和时间长,而且,深度还不能令人满意。同时,除了延长调整试验(试验件的试验)周期、使批生产准备复杂化(因为对设计方案做了许多修改)和使SRM昂贵外,经常会出现发动机无形老化。
随着具有图形信息输入-输出工具(显示器、绘图仪、坐标绘图机,诸如此类)以及能提供实施人-计算机对话工作可能性的高级数学软件系统的计算机的出现,大大增大了对程序化设计系统的兴趣。
程序化设计系统是建立在采用描述所研制结构主要构件设计过程和计算的算法基础之上的。与这些算法相对应的工作软件位于计算机的存储器中,并能够根据研制设计师的指令按需要的顺序《运行》。此外,在计算机存储器中保存着设计所需的大量格式化信息:标准结构件、标准、规格和其它参考信息。
图9.1所示为SRM程序化设计系统框图的其中一种可能方案。每一个单元或者是在计算机上计算的特殊程序,或者是特殊程序库。程序和单元是设计系统的逻辑方法链。统合单元是优化单元。按照优化单元的一个程序(或许多程序),由管理程序进行制定设计方案。
相应专家(内弹道、气体动力学过程、热传递的计算专家、强度计算专家和经济计算专家等)从事制定方法和调试用于列入到程序化设计系统相应单元库中的特殊程序。设计师与程序员一起从事设计优化单元的方法和程序及管理程序。
优化单元的算法不仅说明计算的顺序和按阶段给出图形信息和数字信息,而且还评估结果。为了制定设计优化单元和管理程序所需的合理方法以及指导设计过程,设计师应具有关于所有特殊方法和特殊程序内容和列表的概念,并掌握设计所有主要单元的近似计算评估方法。对于程序化设计系统的运行控制和设计师洞察力的产生—与计算机进行对话的设计师精湛创造的基础-主要素质来说,这是必需的。对作为机器设计过程的直接领导者和参与者的设计师的要求责成他吸引相应专家来参与与计算机的对话、协商和精确程序等。设计师与计算人员之间功能的这种自然分配要求他们每一个都具备相应的知识。计算人员应不仅深刻了解程序化设计系统的现代计算方法及其编制特点,而且,还要会创造性地制定适用于具体情况和在设计过程中所产生的不可预见的情形的新方法。作为机器设计过程领导者的设计师应拥有工程方面的渊博知识,很好了解综合系统中的设计过程、感觉所设计的发动机结构《特点》是如何根据所有设计阶段上不同计算结果变化的,并学会创造性地,足智地提出旨在完善结构的建议。设计师也应了解所采用的材料结构和工艺性能,同时考虑到必须满足使用要求和经济要求以及技术任务书工艺结构要求。
图9.1、SRM程序化设计系统框图:1—优化单元;2—管理程序;3—装药初步几何形状构成、内弹道和气体动力学计算单元;4—结构图构成和强度计算单元;5—绝热层和结构件计算单元;6—结构详细设计单元;7—质量、重心和惯性矩计算单元;8—基本参数的最终评估单元
9.1、设计师的程序化工位
设计师的程序化工位这就是用于使图形信息准备、变换和编辑的操作以及设计师与程序化设计系统互作用的操作程序化的程序化设计系统终端系统。借助程序化工位所解决的主要问题的特点是[3,35]:
大量的多方案计算,这就使有可能将任务分配给单独的子系统,组织使任务解决方案贯通程序化;
可观察到的概念名称表,这就使有可能建立《从目录选择》类型的系统,并指定所选方案的有限修改组。
程序化工位使有可能在独立解决方案中不仅实现生成、编辑、显示技术文件,而且在编排本地技术文件档案库和本地标准程序库时实现本地设计子系统。例如,这可为结构强度计算子系统。在解决这些问题时,程序化工位保障:
设计师-计算机图形语言信息的实时交互;
使信息(首先是图形信息)的输入-输出过程程序化;
生成技术文件(图表,图)。
图9.2所示的程序化工位的技术实现可在能履行显示处理器功能、程序化工位装置控制器功能和组织与中央计算机通信功能的微型计算机基础上进行。此外,程序化工位组成包括:
A—保存标准零件和部件档案、设计师个人档案库和服务程序的外存储器;
B—中间结果和最终结果输出;
C—数据输入或读入;
D—设计师与程序化工位通信的输出装置;
E—在设计师-机器对话模式实时交互和图形显示,它使有可能借助字母-数字和功能键盘及光笔输入字母-数字和图形信息并将其变换。图形显示器通过相应接口与微型计算机交互数据和指令信息。
F—用于快速获取显示器屏幕上照片的照相机;
G—图形数据采集系统,提供被测物体集合信息;
H—控制和操纵平台。
图9.2、设计师程序化工位示意图
与中央计算机共轭单元实施微型计算机与中央计算机通信。在图9.2所指出的组成中,程序化工位使有可能实施:
- a) 在图形信息半自动编码机上半自动准备图纸语言的初步数据;
- b) 借助鼠标和功能键盘绘制草图,或借助功能键盘绘制尺寸图;
- c) 借助平移操作、旋转操作、定标操作,其中包括沿轴线,划轮廓阴影线操作、绘制对称图形操作、按给定比例划分线段操作编辑图;
- d) 编辑符号信息,擦除、补加符号和行,拆分文本,形成打印机输出格式;
- e) 编排设计结构—图构件、部件、整体结构;
- f) 借助自动绘图机、打印机、输出装置编辑信息文件。
对于程序化工位正常工作来说,除了技术设备外,高级数学软件是必需的,可将该软件分为内部和外部软件。内部数字软件的组成部分如下:
图形信息输入-输出装置的数字软件(这里包括图纸读出装置,绘图仪);
图形交互装置(显示器)的数字软件;
由基础程序和参数化程序组成。基础程序用来描述在象带给定坐标的点、带有具体坐标的具体类型直线、带给定斜度和缩放的字符等这类几何变量基础上绘制的具体图象。
参数化程序用来描述外形相似,但线性尺寸不同的几何图象的自动绘制和变换,它面向编排图形程序库。参数化程序应包含:
1)形状均匀图形结构(螺栓、螺帽等)的简洁描述软件;
2)实现格式(显示器格式、自动绘图机格式)转换功能的图形信息输入-输出软件;
3)图形编辑软件;
4)本地文档库编排和管理软件;
5)用来将图象语言转换成微型计算机表示语言的翻译程序,图纸识别程序;
6)由标准程序库、设计应用程序包、图形文档库组成的程序化工位程序库;
7)在微型计算机操作程序基础上建立的和补充有输入-输出程序和与中央计算机通信程序的操作系统。
程序化工位的外部数学软件组成部分是中央计算机数学软件的一部分。传统的软件系统应补充图形信息的说明软件、与处理几何信息相关的标准设计程序组、交互软件。认为选择用来设计数学软件的语言有重大意义。设计师所使用的设计语言及其翻译程序。软件以标准程序库形式合理设计。
设计师使用程序化工位的工作采用带有字母数字功能键盘的图形显示器和鼠标以对话模式建立。借助它们,可采用图形库中的标准零件组装产品或部件,查看所得到的图象并对其修改,用程序化工位的外部存储器记录屏幕上的图,或者将其传输到中央计算机中,同时,将计算结果从计算机输出到屏幕上。
设计师与应用设计任务的对话、任务之间的数据交互和数据库的形成借助将设计任务组成一个统一综合体的专用管理程序实施。
可将设计程序本身划分成两类:特性计算程序;产品的参数优化程序。
对于它们的运行来说,信息软件是必需的,信息软件应包含:参考信息数据库;原型机标准图纸和特性库;设计逻辑图;设计人员的个人数据库。
管理程序和操作系统实施对档案库所有这些组成部分的管理。
下面列出对按照设计师任务所履行的几个简单功能示例的说明,这些示例表明SRM程序化设计系统在程序化工位上制成信息图方面的某些可能性。
例如,为了在显示器屏幕上给定(显示)一个点,设计师将光笔靠近这个点并按压功能健盘上的带《基本点》标志的按键。所显示的点只是大致位于设计师所指出的位置。如果必须在屏幕上以高精度设置点,按压《点》按键。在这种情况下,在显示器屏幕上出现控制表,设计师利用该表从字母数字键盘输入点的坐标(x,y,z)。通过利用所输入的数据,计算机就将带给定坐标的点发送到显示器屏幕上。
为了在屏幕上绘直线,可给定直线的两个端点,此后按压《线》按键。如果需要画一条与这条直线平行的直线,设计师用光笔标记初步直线,并按压《线》按键。在这种情况下,在屏幕上将显示出控制表,设计师利用该表指明,划定的平行线应在初步直线哪一侧以及它们之间距离。
除了点和直线外,设计师还可使用借助功能键盘的单独按键给定的其它几何要素:《弧线》、《圆》、《圆锥》、《椭圆》、《立方体》。这些按键保障绘制圆弧、锥形截面、三次曲线。指定功能键也使用图象转换操作:《比例尺》—改变图象的比例;《旋转》—图象相对给定直线旋转;《传输—旋转》—带图象旋转和不旋转传输图象;《透视图》—绘制透视图象;《几何值》—计算给定形状的几何值;《截面,剖面》—绘制几何形状截面图等。功能键盘包含数十个按键。
在必须得到截面图或图象的情况下,设计师订购载体材料(例如,纸、描图纸和其它)、比例尺和其它数据。这数据输入到在短时间内就发出相应图纸的绘图仪中。
9.2、对SRM程序化设计系统算法的要求
SRM研制过程和该过程的程序化设计系统,从系统分析观点来看是典型的大系统,也就是说,表现出可将系统划分的子系统。在这些子系统中确定任务,同时确定任务之间和不同级子系统之间的相互联系。任务和相互联系应以算法的形式表示。算法应描述图9.1,a所示SRM程序化设计过程的每一个阶段,即:
绘制SRM的初步构型(结构图);
测定外部和内部的力学和热载荷并逐个构件强度计算;
精确尺寸或改变SRM构件结构或整体结构;
图形表示输出信息(逐个构件表示和整个SRM表示);
计算质量、重心、惯性矩。
SRM的程序化设计系统的研制,应从有效地将单个专用算法(确定结构图、载荷图,强度计算等)合并成一个统一系统开始,并保障单个算法之间数据交互;应建立使有可能评估设计方案,对结构做系统改变的统一逻辑,并通过《计算-评估-修改》迭代过程中的循环将其持续到最终目标。SRM的程序化设计系统的最终目标是将输入数据转换成输出数据,并考虑到加在构件和整体结构上的强度和变形限制,以便使结构质量最小。
设计实践表明,通常达到收敛性很快,需要不超过三次逐次逼近。
SRM的程序化设计系统的算法应满足四个基本要求:
1、算法的模块化。SRM的程序化设计系统应按照模块原则建立,也就是说,算法应是独立说明标准过程、部件、构件、情况的单个计算方法。希望在SRM的程序化设计系统范围内可实现的算法也具有模块结构,也就是说,允许将它们划分成足够小的彼此相连的单元。
2、算法的层次性应在SRM的程序化设计系统中表现有说明零件、部件特殊组成部分不同方案、过程计算方法的算法和组合的、相互关联部件方案和过程的计算算法(见图9.1)。同时,提高在SRM的程序化设计系统范围中它们的实现效率的算法也应具有层次结构。
3、算法的功能冗余。应当力求创建不是多用途的算法,而是专用的算法(即使它们的运算范围界限有些重叠)。多用途算法需要从一种运算方式调整到另一种运算方式。专用算法的采用使有可能对于每一种情形创建更有效的算法,同时简化程序的设计。
4、算法的阶梯性。必须具有几个阶梯的算法:从近似评估的算法到相应过程、部件或特性的精确和更准确的计算算法。
评估算法使有可能快速得到近似的结果。较高级的算法拥有更大的准确性,但是,是以增加计算机工作时间为代价的。实践表明[79],在五次或六次逼近后的所进行的计算对结构的改进不大。
9.3、SRM设计的方法基础
根据对技术任务书的研究结果,设计师应直观地设想未来整体发动机的结构《特点》,将其划分为主要工艺结构部件、主要构件的结构材料。同时,应当考虑到将所设计的发动机与传统发动机区别开来的技术任务书的特殊要求。在开始设计前,技术任务书中给定的所有载荷都相应乘以过载系数或安全系数。有时,在绘制结构图前,将未来发动机最可能的结构件参考数据输入到计算机存储器中。此外,可将结构材料、紧固件、压力传感器和信号装置、电点火管、密封圈的标准和其它多次使用的数据输入到存储器中。在程序化设计过程中,这些数据可从系统的存储器中选取并在显示器屏幕上用相应等值线组合起来。
设计从绘制SRM初步(基准)结构图开始。由于从技术任务书中知道了发动机燃烧室前封头直径*(*通常将向着火箭头部的一端认为是SRM前封头,将向着SRM喷管的一端认为是SRM后封头)和发动机推力随时间变化的关系,设计师就预先规定燃烧室中的压强值,并将这些数据输入到计算机设计的程序中。
然后,按下列顺序进行运算(见图9.1):
1)根据内弹道计算和装药计算结果,确定装药的几何形状;
2)在显示器屏幕上,沿预先选好的装药外形绘制SRM初步结构图;
3)从保存在存储器中的构件目录中选择最合适的结构件,在显示器屏幕上调整并放在发动机布局图上;
4)作为特别重要的构件,单独实施调整和安置SRM喷管结构的操作,并同时预先选择非嵌入或嵌入到发动机燃烧室内的方案;
5)保障图的比例尺与放置在图上的结构件的比例尺一致。在将整个发动机安置在显示器屏幕上排列困难的情况下,将作为基准件连接在发动机图上的结构件输入到存储器中。
燃烧室内压最大值的选择是设计中最重要的阶段之一。选择是考虑到动力因素、燃烧室壳体结构承力构件的强度特性以及装药的特性进行的。在初步设计阶段,应以在类似发动机中确定为最佳的压强级为目标。为了防止发动机在其工作开始前或者工作结束后过早破坏(对于第二级和随后级的发动机来说),保障发动机壳体外壳抗外部剩余压力作用稳定性的条件成为规定燃烧室压强的基本判据的情况是可能的。在这些情况下,燃烧室中的最大压强值要选择得,使按这个压强作用计算的壳体外壳壁厚度能保障给定抗外部剩余压力作用稳定性裕度。
在选定发动机燃烧室压强后,从计算机存储器中选择基准发动机及其各结构件(前封头、后封头、封头与壳体连接部件、喷管装置结构件、喷管与壳体连接部件、装药与壳体固定件、点火器、绝热层、抗蚀构件等)的图形。然后,设计师在显示器上再次详细画出结构件的截面、厚度和过渡区域。
在初步设计阶段的布局以配置固定部件、吊挂部件和发动机与其邻接的火箭舱连接部件而结束,此后,完成对所得到的SRM特性的分析,以便确定是否满足技术任务书的要求。这个分析分为初步分析和二次分析。
初步分析是检验结构数据、质量数据、弹道数据和其它数据与所要求的相符性;在这个阶段也对SRM的参数进行优化。二次分析与初步分析并行进行。主要关注对所建议的结构方案计算论证。二次分析包括详细评估结构的温度状态和强度、详细尺寸调整在所有截面和体积中的发动机整个结构相结合的和邻接的部件和零件,也就是说,解决平面上的体积问题(保障输出三维图象的SRM程序化设计系统,使图形解决这些问题直接成为了可能,从而缩短设计和模拟试验的时间)。
在从所研究的备择配置之列中选择最可能接受的SRM配置后,对优选方案进行最终修改,设计主要部件(封头、壳体、喷管等),完成草图设计(或者技术建议书)的插图和图表。
在整个设计过程中,仅仅研制SRM的一半结构(沿发动机的轴线划分)就足够了。全发动机的结构可根据图形对称性绘制,并附加不对称配置的结构件图(例如,运输和使用时的SRM固定部件图)。
发动机的配置可以任何视角的等距图形显示在显示器屏幕上,这就会大大减轻和加速图解材料的准备工作。
9.4、给设计师的实际建议
在所有设计阶段上,重要的是设计师应不仅了解设计过程的组织方法顺序,而且,还应既要了解整体SRM的一系列设计特点,还要了解它单个部件和零件的一系列设计特点。
了解这些特点就有可能使设计师避免进行大量计算分析的必要性。正是了解这些特点和能够预先预知不同部件和零件的设计特点对未来发动机外形和特性的影响就构成了设计师的创造性知识基础。
下面所提出的一些建议有可能使设计师不仅得到关于SRM和主要结构件的设计特点的概念,而且还制定出设计经验的积累方法、设计过程中创造性分析的洞察力积累方法。
结构方案的选择
在结构方案选择阶段,应了解,在长径比为2-5条件下,将得到SRM壳体的最小质量。如果在技术任务中已确定直径,那么,就很难影响这个参数,因为壳体的长度由保障最大允许装填系数的装药计算确定。
在确定壳体的长度和直径后,选择封头的构型。
封头的形状取决于订货方是否给定发动机长度或与发动机邻接的并用于安置设备的舱空间的限制。封头的标准形状:半球形形状、椭圆体形状、环球形封头和卵形封头。
半球形封头的封头质量与内容积之比是最有利的,但是,在总长度相同的条件下,半球形封头的发动机壳体具有比较平封头(例如,椭圆体封头)壳体小的装填系数。
椭圆体封头不太深,可或者以恒定厚度制作,或者以变厚度制作(通常在车削的封头中)。但是,在这类封头到壳体过渡区域,会产生切向压缩力,在椭圆轴线之比小于0.61时,切向压缩力就变成危险的,并可导致在这个环形区域失稳。然而,在封头制作成可拆下的并具有刚性法兰的情况下,椭圆半轴线之比可减小到0.515。
车削封头的结构与旋压的或焊接的封头不同。在发动机中采用车削的封头或焊接封头的问题应根据技术经济分析结果解决。
在设计发动机壳体壳体(或锥形,如果SRM是锥形的)段前选择壳体段的材料。在这个阶段对各种不同材料(金属和非金属)进行比较评估。
对于设计师来说,不应有差的材料。这就是金属,或者是非金属纤维材料,采用它们的有利性或合理性取决于对整体SRM及其构件的综合技术要求、力学载荷和热载荷。对于壳体和封头来说,合理的是在技术任务书中给定的条件下,具有最大比强度或比刚度的材料。
通常,发动机燃烧室内压强是决定材料选择的主要载荷。但是,在装药质量相同和燃烧室压强恒定的条件下,发动机工作时间的减少会使得推重比(推力与质量之比),即过载增大。同时,可变成临界参数的不是燃烧室压强,而是根据壳体抗压缩稳定性的轴向载荷或在无燃烧室内压条件下壳体的外部剩余压力。对材料选择可能有决定性影响的是壳体外壳的最大温度级,并考虑到SRM在这个温度下的工作时间。考虑到综上所述,应注意由对表3.1和表3.3分析得出的下列先决条件。
1、对于一次性使用的壳体壁上最大温度不超过80…120的SRM来说,《蚕茧》式,也就是说,用螺旋缠绕方法制作的并完成封头与壳体外壳完全吻合的玻璃纤维增强塑料壳体是最有利的。
2、用纵向-横向缠绕方法制作的玻璃纤维增强塑料壳体要求用机械方法将封头固定在其上。机械接头(通常是柱销接头)的存在会减小结构的质量增益。因此,在壳体长度与其直径之比大于按照公式(4.7)计算出的值条件下,这种壳体在质量方面就具有对金属壳体的优势。
用纵向-横向缠绕方法和用螺旋缠绕方法制作的玻璃纤维增强塑料的温度限制是相同的。对于长度超过8米和直径超过两米的壳体来说,由于负重很大和工艺装备复杂,采用用螺旋缠绕方法制作的壳体就变得困难。对于大型发动机来说,用纵向-横向方法制作的壳体工艺性更好。
3、对于壳体壁温度达300℃,无论是对一次性,还是多次使用的SRM的外形尺寸无限制的SRM壳体来说,高强钢是合理的。
4、在高湿度条件和海上条件下,高强不锈钢作为抗蚀钢采用。
5、由于成本高和较之钢的工艺性差,高强钛合金在SRM中的应用应最大限制并深刻技术论证。钛合金对于SRM壳体的应用,可能在作为抗蚀和在将壳体加热到400…450℃条件下工作的材料多次应用的特殊情况下是有理由的。
6、将高模量(高比刚度)铝合金用于负载外部剩余压力的小型壳体和喷管嵌入到燃烧室的部件是很有效的。这种零件工艺性好并廉价。在结构质量无硬性限制的情况下,将其应用在大批量和大量生产的SRM是合理的。
下列例子验证了所列出的一些建议。
《凤凰》导弹作为军用超音速飞机的武器采用。由于携带导弹的多次起飞和降落,SRM壳体可受到 -50到+300℃温度的循环作用。《凤凰》导弹的壳体用高强不锈钢制作。
《短跑》导弹是一次性使用的导弹,存放和发射都在保持零上温度范围的发射壳进行。在《短跑》反导弹上的SRM壳体是由玻璃纤维增强塑料用螺旋缠绕方法制作的。
壳体材料的选择,而且有时甚至是壳体主要尺寸的选择都可取决于不同性质的因素。公认,威力大的大型SRM可以并希望采用当今已经试验好的结构方案和研制好的工艺来设计。如果可以,甚至从已试验好的发动机全部借用工作量最大的和不可靠的部件(壳体、喷管、推力矢量调节系统)。有时,这种方式不仅由经济效益所证明,而且还由通过大大缩短试验周期使有可能防止无形老化所证明。已查明[61],用变化工艺过程达到将大型SRM特性提高5%,就会使得研制费用增大50%。发动机故障风险也大致增大这种程度。
在考虑到所列出特点初步选择材料后,按照第四章中所推荐的近似公式测定壳体的近似初步壁厚。
绘制SRM结构图的下一个主要要素是选择喷管结构方案。SRM喷管不同结构方案最有实质性的特点为以下。
从所需绝热层质量的观点来看,在喉部截面尺寸相当大(200…250mm以上)的大型喷管中,具有喷管中能量损失最小特性是最好的单喷管结构方案(图9.3),它允许在喷管的亚音速段、喉部和超音速段采用额定烧蚀的复合材料。
图9.3、喷管图:a—嵌入到SRM燃烧室中的喷管;б—标准(外伸)喷管
嵌入到燃烧室中的喷管(图9.3,a)使有可能缩短SRM的长度,减小推力矢量控制部件的质量(在用从燃烧室中放出气体的结构方案中)。在这种情况下,由于必须增大嵌入到燃烧室内的喷管部分的径向刚度和绝热层厚度,喷管直接质量就比上一方案喷管的质量大。
对于为了在飞行中保持重心位置需要将发动机接近火箭重心和远离火箭后端的地方配置的SRM来说,特有的是在亚音速段带长尾喷管方案(图9.4)。
在实践中,采用喉部截面尺寸可变化的两种主要喷管方案:喉不部截面可互换的嵌入块和使有可能(例如,在双模式推力特性的SRM中)进行分级,或无级调节喉部截面(以便在宽使用温度范围内推进剂性能偏差很大的情况下将推力保持在窄的值范围内)的结构件。
图9.4、长尾喷管
多喷管方案(图9.5)使有可能缩短SRM的长度,对于借助摆动喷管控制推力矢量的方案来说是合理的。热防护构件的质量比单喷管方案的大一些。达到喷管抗烧蚀构件相同烧蚀值的不可能性就会导致产生推力差。
图9.5、四喷管方案
带推力矢量控制的一个摆动喷管的方案(图9.6)对于推重比很小的SRM,也就是说,对于弹道导弹的SRM来说是最合理的。对于工作时间短、推重比大的高速反导弹SRM来说,由于在百分之一和千分之一秒内保障喷管摆动所用大力矩的困难性,这些方案是不合理的。
图9.6、带弹性构件的摆动喷管方案:a—带弹性构件的喷管;б—计算所用的喷管构件详图
由于沿喉部圆周不均匀的和相对大的烧蚀,外扩张喷管(环形喷管)未必在推进剂燃烧温度2000K以上和工作时间超过0.5秒的可预见的未来SRM中得到应用。
点火器安置在前封头区域,很少安置在喷管区域。安置在喷管区域中的点火器保障SRM进入状态的时间较长,但是,较容易,也就是说,或者可与发动机分开安置在发射装置上,或者可安置在被SRM最开始工作时的燃烧室内压打落的发动机隔板上。任何一种方案的选择都取决于发动机用于火箭哪一级、取决于对进入状态是什么要求、装药的位置如何(例如,在翼槽后或者在翼槽前,如果装药是通道翼槽式的话)、在使用期间要求进行什么定期工作。
发动机的质量效率也取决于附加结构部件的存在。属于它们的是发动机与邻接火箭舱对接所用的构架、稳定板或空气动力舵和与它们相连的装置(舵机和它们的电源)在发动机上的固定部件、在发射装置或运输发射壳上的固定部件、电通信系统固定部件、电源固定部件、索具接头等。这些构件和它们安置处的壳体补强增加了SRM的质量。必须力求将附加部件安置在发动机上现有的刚性箍(法兰和封头区)中。在不可避免将部件安置在壳体或封头的外壳上时,必须利用对外壳的结构补强使部件周围的局部应力微乎其微。
壳体与封头的连接主要是以加楔连接、销接和法兰-螺栓连接形式完成,在金属封头与玻璃纤维增强塑料壳体连接的情况下的连接种类是销钉-螺栓连接。在设计螺栓连接时,为了减小弯曲力矩对接头的作用,必须力求使螺栓轴线尽可能接近为壳体外壳中间层延伸的线与法兰对接面交叉点。螺栓轴线的最终位置根据计算精确。
SRM喷管程序化设计系统程序设计方案
在这里所研究的喷管程序化设计程序设计方案[84]使有可能得到关于SRM任何结构部件和整体发动机的程序化设计程序设计方案的概念。
为了研制SRM喷管的程序化设计系统,必须:
1)设计在实践中遇到的喷管结构图并编制结构图的分类符;
2)编制使得喷管结构定量特性变化的可变参数表;
3)设计喷管结构模块化构件;
4)设计气体动力计算程序和喷管型面的计算程序;
5)设计热计算程序;
6)设计强度计算程序;
7)设计所设计的喷管结构的绘图程序。
结构图分类
按照连接到发动机的形式,喷管被分为外喷管和嵌入式喷管。外喷管是连接在火箭发动机燃烧室后部的拉瓦尔超音速喷管。嵌入式喷管的结构由于首先必须不仅在里面,而且还从外面防嵌入部分受热气体的作用,其次由于必须保障嵌入部分抗外部剩余压力的稳定性而复杂化。
通常,给SRM都提出保障推力矢量控制的要求。推力矢量控制功能或者可由摆动喷管,或者可由连接在固定喷管上的专用系统,例如,用向喷管超音速段喷射液体或喷射热气体的推力矢量控制系统来履行。推力矢量控制实质上使喷管结构复杂化了。
所有可能的推力矢量控制方式中最普及的是三种类型的摆动喷管和固定喷管用的三种推力矢量控制系统。
图9.7和图9.8所示的摆动喷管具有履行双重功能的同类型构件:保障喷管活动部分相对固定部分移动并将活动部分固定在固定部分上。这类构件可为球窝节、通用柔性接头和柔性密封。具有仅在一个平面中位移的铰接喷管(例如,这正如《民兵》导弹第一级SRM四喷管系统中所完成的那样)是带通用柔性接头喷管的简化变体。在摆动喷管中产生力图使活动部分脱离固定部分的力。为了保障喷管活动构件相对固定部分运动并同时平衡分离力,规定有结构措施。例如,在铰接喷管中,载荷通过承力嵌入块从活动部分传递到固定部分。承力嵌入块和环形气体密封或者在密封面中,或者在密封面前,或者在密封面后可具有旋转轴。
图9.7、摆动喷管:a—带承力嵌入块 图9.8、摆动喷管的变参数图形
的喷管;б—带通用柔性接头的喷管;
在结构方面,带通用柔性接头的喷管类似于在密封面中带有旋转轴的铰接喷管,但是与其不同的是没有承力嵌入块(见图9.8,б)。在这种喷管中,使活动部分与固定部分分离的力通过万向支架环传递。在一个平面中旋转的铰接喷管变体中,分离力通过柱销轴传递。在一般情况下,旋转轴应位于密封面中。
密封件的动力学和静力学要求,将柔性接头以喷管轴线与连接旋转轴和密封横截面中心的线之间45左右的夹角或者配置在密封前,或者在密封后。
这样一来,摆动喷管对于带球窝节的结构来说就有三种方案的旋转轴位置,两个方案用于带弹性密封的结构,一个方案用于柔性和通用柔性结构。按照活动部分与固定部分的分离位置,可有三种方案(见图9.9):1)分离线在超音速段的喷管(既可采用在外喷管中,也可采用在嵌入式喷管中);2)分离线在亚音速段的喷管(适宜于外喷管)和3)分离线在发动机燃烧室到喷管的过渡段的喷管(喷管的内几何形状保持连续的;适宜于嵌入式喷管)。在超音速段分离的喷管具有下列特点:作用喷管活动超音速段的力力图将其贴近固定部分,也就是说,不是分离力,而是压缩力。这个特点应在设计铰接接头和密封时考虑。
我们来研究连接到固定喷管上的三个推力矢量控制系统:喷射液体、喷射气体和采用导流器(图9.9)。
图9.9、带推力矢量控制的喷管图: 图9.10、喷管的变参数图形
а—阻流板;б—在喷管嵌入段喷射气体;
в—在燃烧室外用喷射孔喷射
喷射液体和采用导流器的推力矢量控制系统既可用在外伸喷管中,也可用在嵌入式喷管中(图9.10)。
喷射热气体的推力矢量控制系统可有两种方案:
1)将放气孔配置在发动机燃烧室内的喷管嵌入段上(见图9.9,б);
2)将放气孔配置在发动机燃烧室外并用气体管路将热气体由燃烧室送到喷射孔。
按照超音速段的形状,将喷管分为锥形喷管和特型喷管。
图的进一步细化详图用图9.6,б所示。通过将所列出种类的结构方案不同组合,就可得到一百种左右的SRM喷管结构方案。
SRM可变参数表
程序化设计系统的可接受性由其程序对在发动机下列参数的所有组合条件下设计喷管的适用性来评估:推力、燃烧室压强、发动机工作时间、喉部面积、扩展比、推力矢量最大偏转角和推进剂成分。
此外,程序化设计系统的程序应使有可能在不同结构件的材料、工艺性、复杂性和安全系数变化时对结构评估,以便完成象在完成给定要求条件下保障成本最低、在完成一系列要求条件下保障最小质量,或者不超过给定质量保障成本最低这类要求。
结构的模块化
模块化的过程是设计就其结构型式对不同种类的喷管都是公用的或完全相同的结构件。例如,所有喷管的出口锥和嵌入式喷管的进口(头部)构件实际上是相同的。甚至象摆动喷管的弹性密封件这类复杂件主要具有完全相同的结构。
在下一个模块化阶段,对所有喷管公用的零件分类并对它们编制程序。
第十章:SRM的试验改进和可靠性
在转入批生产和使用前,SRM的结构及其参数与技术任务书要求各方面的相符性应得到技术任务书中所要求的可靠性水平所确认和证明。确认应主要以根据综合试验所得到的实际资料为基础。对结构的试验改进和对验证完成技术任务书所有要求的SRM综合试验是有经济根据的,因为要排除在批生产和使用过程中不允许的事故和原则性改进的可能性。
10.1、SRM原型机的试验改进试验的种类和试验量
原型机的试验改进从它的首批生产准备阶段和制作开始。在试制生产阶段,研究各种不同生产技术因素对发动机结构的影响。同时,根据设计师与机加工艺师、冶金专家、非金属材料加工工艺师、装配工和试验人员的密切协作结果,精确初步设计文件和工艺文件。在这个阶段,结构方案和所选工艺过程的可接受性用对SRM的所谓综合工艺检验冷试验来检验[5]。综合工艺检验冷试验来检验从对壳体的内压液压试验开始。每一台壳体预先通过加压液压试验。为了检验结构强度,从首批中抽出几台(2-3)壳体,其中包括1-2台带绝热层的壳体,并加载直至破坏。为了积累统计资料和对试验结果熟练分析,从最初试验,就对最感兴趣的壳体段进行应变测定是合理的。在用液压试验验证SRM主要部件的结构强度和检验壳体密封后,允许对全尺寸SRM进行综合冷试验、试验台点火试验和其它种类的地面改进试验。属于这些试验的有静态试验、重复静态试验、动态试验、热试验、加速环境试验、研制点火试验、运输试验和试验验证技术任务书要求的其它种类试验。
在研制试验过程中,通常对结构进行在设计文件中得到必然反映的改变。由于真实发动机试验成本高,试验量和测量量必须尽可能减少。为了缩短试验周期和减少试验费用,将不同的试验种类结合(也就是说,在一次试验过程中得到满足技术任务书要求最大量的信息)、多次使用在恢复或修理损失或遭受损坏零件(绝热层、油漆涂层、密封圈、固定件等)后的整体发动机或其构件的硬件来进行地面(而有时飞行)改进试验可提供很大的经济效益[81]。当在一定程度上可保证保障基本特性和工作安全性时,就从地面改进试验的初步阶段将发动机发送去在火箭装配中进行地面试验和飞行试验是很有益的。一方面,这使有可能得到表征SRM结构功能的最可信信息,另一方面,使有可能尽早开始对火箭飞行试验。在固体火箭发动已优化结构和根据试验得到的特性开始符合技术任务书中给定要求后,可认为改进试验完成。
在改进(工厂)试验之后,以跨部门试验结束的SRM标准试验和特种试验的阶段就到来。进行标准试验是为了评估在改进试验过程中对结构所做的变化的效果,而进行特种试验是为了确认发动机完成技术任务书的特殊要求(在海水浇注条件下的稳定性,加速环境试验等)。同时,经订货方(技术任务书编制者)同意,为了减少试验量,应考虑到在上一阶段(用来检验所交付的发动机批次的质量所进行的)检验试验和改进试验所得到的最大量的良好结果。
在完成对火箭装配中的SRM成功改进试验后,应通过国家试验。根据跨部门试验和国家试验结果,修改发动机的工作文件,并作出发动机开始批产和使用的决定。
静态试验使有可能在各种不同计算情况下测定发动机各构件在载荷作用下的实际应力变形状态。除燃烧室内液压外,用传递液压作动壳力的杠杆、环给发动机施加局部载荷。可借助充气橡胶囊或卡箍与液压作动壳系统连接的滑掌形成模拟迎面气流空气动力力作用的不均匀外部剩余压力近似情形。为了最精确再现因与发动机邻接火箭舱的作用对发动机的加载情形,它们应在刚度方面与实物的一致,或者,更好的是实物。
静态试验用使有可能根据时间进行详细测定和测量几何形状变化、燃烧室压强等的专用液压作动壳进行。
在结构设计水平高的条件下,为了节约资金,很少需要对1-2台以上发动机进行静态试验。
进行SRM的热试验是为了测定结构材料、绝热层和防护固定层与固体推进剂装药粘接以及直接装药的强度特性和变形特性因运动(空气动力)加热作用、发动机构件因燃烧产物和装药固化过程中温度变化的加热作用的变化。试验在有从加热观点来看最危险温度段变化的高温室中进行。通过在试验台和飞行试验过程中采用测温,就得到关于发动机各构件温度状态的附加资料。由于推进剂导热系数低,在发动机存放时的环境温度变化过程中,在装药中产生不均匀的温度场,这就导致在防护固定层装药中产生温度应力。为了测定装药中的温度场,可沿由允许钻孔和松弛的惰性体专门制作的装药肉厚安置热传感器。在测定标准装药温度的情况下,将传感器安置在装药外表面、内通道表面和端面上。
由于所得到的特性可信度最大和质量最高,SRM的试验台点火试验在试验总量中占比率最大。进行试验台点火试验的试验台应使有可能实时进行测量推力、燃烧室内压、温度状态、应力变形状态、照相和自动化高速摄影,同时进行测量俯仰,侧滑平面中推力矢量控制装置的侧向力和力矩(图10.1)。在必须模拟高空条件的情况下,在试验台上安置气压容器(图10.2)。
图10.1、带推力矢量控制的固体 图10.2、高空试验台示意图:
火箭发动机点火试验卧式试验台 1—高空试验室;2—主要的抽气系统;
3—真空计;4—辅助抽气系统
动态试验使有可能得到关于在飞行时、在地面使用时、运输时、过载时、燃烧室内压脉动时所产生的动态载荷条件下SRM耐振强度的客观信息。
异常试验结果的分析
可将结果是未完成给定要求的所有试验列入异常试验。异常试验可能伴随结构破坏或以某种参数(例如,燃烧室内压,工作时间等)不允许的偏差形式表现出来。
我们来开始研究与在冷强度试验(例如,液压试验)时结构力学破坏相关的这类试验。在结构根据错误强度计算制作,或者在对结构加载过程中出现了未考虑到的(难以计算的)因素的情况下,可能会发生结构过早破坏。例如,粘贴在绝热层上的弹载通信板区域中外绝热层变形增大超过计算值就可能导致绝热层沿通信板对称轴线开裂。在结构中存在在制作过程中所形成的缺陷(例如,由于允许的工艺偏差)也可能成为异常试验的原因。
对于所有列举的情况来说,可建议下列查明破坏原因的顺序。
1、仔细察看破坏位置。常常如果破坏的原因是肉眼能看得见的缺陷,就可马上查明原因;比如说,对于WCoSi-1和ВЛ-1类型的材料来说,特有的是存在使有可能很精确查明金属断裂点的《枞树枝状》缺陷(图10.3)。
图10.3、指明断裂点位置的《杉针形花纹》类型破坏方式:a—带有特有的《杉针形花纹》破坏区域照片;б—照片上所示的区域图
2、对从可疑段断口切下的试件金相研究(黑道、断口形貌、有夹杂和其它)。根据这些研究结果,可发现用肉眼无法看到的缺陷(表面扩散损伤(粉笔图案、无碳层、压折痕和其它)。与金相研究的同时,用从与结构破坏区域邻接区域切下的试件进行检验材料的力学性能。在很难发现明显断裂原因的情况下(可见的缺陷,偏低的力学性能),可建议下列查明异常试验原因的方式:
- a) 如果将进行结构强度计算时允许的误差假定作为异常试验的原因,那么,必须重新进行精确的和详细的验证强度计算;
- b) 如果将存在未考虑到(或很难考虑)的因素假定为异常试验的原因,在这种情况下,进行重复试验并详细测定应变;
- c) 如果存在有在所采用的标准缺陷水准中用现有的检验方法不能查明的缺陷,那么,严格限制所采用的制作检验方法,或者采用双重方法(例如,对壳体带附加着色探伤的超声检验)。
液压试验或气动试验时对结构的加载方式大多是相同的(加载速度、进行试验用的工装等)。因而,它们通常不是异常试验的原因。
在试验台点火试验或飞行试验后查明缺陷是一个较复杂的过程,因为在这里另外包括了象加载速度(载荷施加时间)、高温和高压气体的热作用、未考虑到的引起压强增大的发动机燃烧室中附加气体流入源。
在一般情况下,异常试验的原因可能为其中一种因素:缺陷、强度计算误差等。可根据所描述的方式进行查明原因。在这种情况下,结构的破坏通常发生在燃烧室内压低于计算压强的条件下。在压强可能急剧增大到很大压强级的狭窄翼槽中产生燃烧基点的情形可能是例外,可用进行模拟所假定缺陷的重复试验来证明。
在结构因超过计算值的载荷破坏的条件下,显然,主要的问题是查明载荷增大的原因并排除它们,而不是被动地争取提高强度,这实际上任何时候都不会带来成功的。
设计师对所进行的试验中发生的物理过程的了解、正确进行测量和判读所检测参数记录的能力在顺利调查异常试验原因中起着很大作用。例如,在波形图上曲线与计算特性偏差(图10.4)的出现应必须严格加以解释,或用随后试验验证。
示例。在对一台SRM系列试验中,在工作结束时,在波形图上出现压力《峰值》(见图10.4,e)。对它们出现的原因研究时的发现,在装填时包含在推进剂中增塑剂向绝热层中迁移的现象,边缘效应。这就使得装药附面层贫化增塑剂、形成多孔结构并因此增大燃速。此外,发现,在这种情况下,也发生其它危险现象。附面层贫化增塑剂使得推进剂装药附面层物理力学性能发生了实质性变化,减小了塑性,这就在附面层应力相当大的条件下,特别是在有端面出口时,导致装药破裂,也就是说,形成造成压力升高的附加燃面。在长期存放条件下,这导致出现不允许的为应力集中区并使装药破坏的大裂纹,从而导致出现异常试验结果。在查明压力升高的原因后,采取措施:采用机械阻止增塑剂从装药渗入绝热层—铝箔。这个措施能解决问题并会消除所描述的燃烧室内压升高的原因。
既然发生在产品中的所有过程都是相互关联的并随着时间而进行,在试验台试验过程中,就与时间绑定进行记录所有可测量的参数。
图10.4、标准波形图示例(实线—实际关系曲线,虚线—预测的关系曲线):а—标准波形图(正常工作);b—非计算压力降(附加通过截面打开,例如,在喉部截面嵌入块或由于破裂它的一部分飞出);c—非计算压强增大(例如,由于装药因不同原因破裂,或防护固定层下面装药表面因装药与防护固定层粘合强度不足分层而打开,燃气流入附加表面打开);d—点火器非计算动作的压强《峰值》;e—工作结束时的压强《峰值》,例如,由于增塑剂由装药中向防护固定层中迁移,或者装药有限附加燃面打开);f—在工作最开始进入状态时,由于装药破裂或附加燃面无限制的扩展打开,压强急剧增长
高速摄影也将画面与时间绑定进行。因为,所有的破坏过程在很短的时间间隔(1~10ms)进行,检测仪器的分辨能力应使有可能记录下这些过程(例如,除了普通摄影外,采用速度达每秒1000帧以上的高速摄影是合理的)。采用摄影机通常是使有可能既可按时间,也可按部位确定破坏点的决定性手段,因为它提供正在工作产品的总画面,同时传感器(应变温度传感器、压力传感器和其它传感器)与结构的具体点绑定,因此由它们所得到的最可信信息表征它们所安置的区域。当然,应根据传感器示数来评估其它区域的应力(温度或振动)状态,但是,在这种情况下,必须完全确定地表示发生在产品中物理过程的实质及其定性和定量相互关系。这些过程的概念越精确,对于没有传感器的区域来说,所得到的结果就越可信。
在查明异常试验时的破坏原因时,起着很大作用的是了解所试验对象的独特特点、在制作对象时允许的所有偏差和特别是那些可能影响功能的特点。例如,假定,在制作自由装填可粘合在壳体上的装药时,允许通过切除缺陷部位途径修复的缺陷并用惰性物质填充空隙,可是在工作时(在装药燃烧过程中),发生了导致破坏的压强急剧增大。如果试验后的分析表明,破坏发生在与装药修复段燃烧周期相对应的时间内,那么,在这种情况下,对装药缺陷部位修复质量不好可作为最可能的原因。
分析和制定旨在消除异常试验原因的措施可按两种途径中的一种途径进行。
第一种途径—用依次排除所假设的因素逐次检查异常试验所有可能的原因。从积累统计科学经验观点来看,这个途径是很有意义的。这个途径的不足是持续时间长和《纯》实验保障复杂。因此,这个方法在研制实践中使用得相对少,主要是用在原因很少和原因几乎明显的情况下。应当牢记,所查明和确认的原因也不排除同时进行基于其它可能原因的预防措施的可能性。
第二个途径—基于所有假定和清楚的原因同时采取措施。这个方法在实践中使用频繁得多,因为它能够最迅速得到发动机试验的满意结果,有时甚至不查明异常试验的真正原因。
由对所列出的方式分析可看出,时间和物资花费的合理性实质上取决于初步数据的质量和可信度、取决于在异常试验时可得到的所选先决条件的正确性。因此,重复试验(在异常试验后)要求不管是在制定试验大纲和直接试验方法时,还是在装备试验测量设备和所需灵敏度和分辨率的传感器以及记录精确判读的设备时都要仔细准备。
加快得到试验结果的一个重要因素是对所测量出的数据处理速度。目前,越来越广泛采用机器处理在试验过程中的测量结果,并以便于分析的表格和图表形式快速发送结果。
10.2、SRM的可靠性
可靠性被理解为保障起动无故障性、保障在给定的整个时间内功能、完成参数要求的发动机性能总合。
狭义上的可靠性一词被理解为发动机工作的无故障性。
可靠性是发动机的质量特性。它的数值可作为对发动机保持结构相同的所有发动机固有的平均无故障性的能力置信程度[33]。
将与可靠状态相反的发动机状态,也就是说,失去功能状态通常称为故障。
在SRM中区分出结构故障(结构故障:破坏、烧穿、固定处分开、活动部件卡滞,例如,在推力矢量控制系统中等)和参数故障—发动机参数(推力、工作时间、总冲、侧向力等)与允许偏差的范围。
可靠性(结构和参数的)是在SRM设计时奠定基础并在它的制作和使用过程中得到保障。这并不意味着,在设计阶段,例如,通过简单地增大结构的机械安全系数就可解决可靠性的保障问题。在设计SRM时,给定的可靠性通过制定能阻止产生故障原因的一系列措施来保障。比如说,众所周知故障的可能原因之一是,由于在发动机存放过程中温度的变化,在推进剂装药通道和它的固定处及绝热层等中积累的变形和应力。在这种情况下,《采取一系列阻止故障产生的措施》理解为利用以前所进行的试验经验和结果,或重新进行选择粘合层材料、绝热层材料和排除应力或变形积累,或者在所使用的材料允许范围内将它们减小到最低的结构方案的专门试验和研究。
采取消除其它所查明故障原因的措施的方法是相似的。
但是,导致SRM工作不十分满意的原因是多种多样的,绝大多数是不可能预测的。因此,故障的出现带有随机性质。预测具体单个发动机中的故障,而况且确定它的性质和在某一情况下的到来时刻不是可能的。同时,通过说明全部同型发动机,就可在统计试验结果基础上,估算发动机由有功能状态过渡到(结构和参数)故障状态的平均概率,并以某一概率保证发动机在给定使用条件下的可靠性。换言之,故障属于随机事件范畴,而可靠性的数量特性定义为概率特性。
在试验数量有限的基础上,由于必须具有关于全部发动机可靠性的概念,就应引入概率。我们通过例子来解释这一点。例如,假设对50台发动机试验,其中两台有故障,而48台获得了成功的结果。在这种情况下,可靠性将为0.96。这个估算是点估算,是成功试验与它们总数之比:式P=1-m/n中m—故障数量;n—所试验发动机的数量。
所得到的点估算最好是真正的可靠性,如果总共有50台发动机,它们所有最好都经过了试验。但是,这是不现实的情况。实际上,只是对制作好的发动机总数中的一部分发动机加以试验。这是因为,例如,与液体火箭发动机不同,SRM属于一次性起动系统,因而在所提交的批中,无论怎样都不能直接检验所有发动机的可靠性。否则,就没有什么可提供。如果根据50台发动机的试验结果,需要评估数百台发动机的可靠性,那么,点估算已不再是有足以代表性的。既然通过试验途径确定的故障数量是随机值,并可能结果是在对所指出的50台发动机试验时,所有50台发动机最好都无故障工作,或者仅观察到一个故障,那么,在这种情况下,变得很明显的是,可靠性的点估算不可能适用于整个数百台发动机。
可估算的可靠性真值可能位于相应局限于可靠性下限值和上限值某一置信区间,该区间宽度(Pв-Pн)取决于所试验的发动机数量(选取量)和所选的置信概率级。换言之,在试验数量有限的情况下,测定可靠性特性的真值是不会成功的;仅可以某一置信概率保证这些特性的变化范围。在下列表中,针对几种情况,其中包括对于所描述的例子,列出了可靠性范围值。
故障数量,m |
选取量,n |
可靠性点估算P |
可靠性下限(Pн)和上限(Pв) |
|||
在置信概率0.9条件下(错误风险0.1) |
在置信概率0.8条件下(错误风险0.2) |
|||||
Pн |
Pв |
Pн |
Pв |
|||
0 0 1 2 |
25 50 25 50 |
1 1 0.96 0.96 |
0.894 0.945 0.821 0.880 |
0.996 0.998 0.977 0.978 |
0.920 0.958 0.855 0.900 |
0.991 0.995 0.967 0.968 |
1 |
50 |
0.98 |
0.909 |
0.989 |
0.927 |
0.983 |
由所列出的推论可作出下列结论:可靠性估算不可能比它所依据的数据准确;如果发动机实际上可靠性低,那么,任何统计处理都不能改变这一点;结构的技术性能和质量产生发动机可靠性真值,而统计方法仅使有可能评估发动机固有的特性;全尺寸发动机的点火试验能提供最可信的可靠性数据。
在发动机的下列研制、生产和使用阶段进行测定产品的可靠性:
1)发动机的技术任务书编制和草图设计阶段(下面我们约定将这个阶段称为设计周期);
2)对发动机进行地面独立试验和在火箭装配中对发动机飞行试验阶段;
3)完成使用试验阶段;
4)批生产阶段。
在每一阶段,将可靠性计算评估结果与技术任务书中给定的可靠性值比较。
设计周期中的可靠性测定
在被称为设计周期的编制技术任务书和草图设计阶段,进行计算SRM各构件的可靠性,以便论证结构方案和工艺方案的选择并检验完成发动机及其构件可靠性的技术任务书要求[5,9,14]。从评估可靠性方法观点来看,设计阶段的主要特点为以下:
没有实物试验,或者实物试验量极其有限;
关于在该发动机工作条件下所使用的材料性能信息量不完全;
没有发动机各单独部件最终所采用的结构方案。
在这个阶段可靠性的计算主要任务:
论证发动机主要构件结构方案的最佳方案的选择;
根据结构材料物理力学性能的偏差,对发动机结构计算进行精确;
根据现有的绝热层特性值偏差试验数据,对所选的绝热层厚度进行精确预估;
检验完成产品及其构件可靠性的技术任务书要求的可能性;
制定提高材料性能稳定性和强度特性所需的工艺措施的建议;
对检验所采用方案所需的信息量(地面试验和飞行试验时)论证。
在设计阶段,假定将产品,例如,划分成下列组成构件:发动机的装药、壳体、封头和喷管。
对于任何一个构件来说,无故障工作的共同条件是条件ui=(xi-yi)>0,式中xi—该构件极限允许的载荷值(《强度》);yi—这个构件的载荷作用值(《载荷》)。
载荷的种类:支承的反作用力、轴向力、内压、温度应力、变形等。在一般情况下,任何构件的无故障工作概率:
P=P(u1>0;u2>0;u3>0,…,un>0)
计算的初步方程是用来测定《载荷》y和《强度》x的解析关系式:
X=f(λ1,λ2,λ3,…,λk)
Y=φ(z1,z2,z3,…,zi)
式中λ1,λ2,λ3,…, z1,z2,z3,.—函数变元,计算每一个具体部件所用的函数变元将是各自的。测定可靠性的概率计算问题包括测定《强度》x和《载荷》y的数学期望值和均方差。为了测定它们,需要知道所研究的参数分布规律。通常采用正态分布规律。
测定数学期望值和均方差的方法之一就是数学仿真方法。在采用这个方法时,进行测定某一个参数的《数学起动》。同时,包含在公式中的变元在每一次起动中采用其公差范围中的随机值。统计处理根据大量的《数学起动》所得到的未知参数xi和yi值,以便求出:
数学期望值
\(E\left( X \right)=\frac{\sum\limits_{1}^{n}{{{x}_{i}}}}{n};E\left( Y \right)=\frac{\sum\limits_{1}^{n}{{{y}_{i}}}}{n}\)
均方差
根据所得到的这种具体分布规律的E(X),E(Y),σx,σy值,测定概率P=P(u1>0;u2>0,…,un>0)。
为了减少工作量,在电子计算机上,按照数学仿真方法进行计算。
整体产品的无故障工作概率定义为发动机每一个构件的无故障工作概率:
PR=P1P2P3…Pn
在试验优化阶段上初步可靠性水平的验证
为了准许发动机地面试验或飞行试验,要求验证初步可靠性水平[5]。初步可靠性水平表征在一定阶段发动机的完善程度,为了验证其可靠性水平,规定一定数量的在地面独立试验或飞行试验供货配套中没有一次故障的发动机试验(n)。对初步可靠性水平的要求在发动机地面试验完善的总大纲中约定。初步可靠性水平按照公式计算(图10.5)PF=1-qF,式中qF—初步故障概率(或有缺陷发动机比率),它由公式β=(1-3qF)n测定(β=0.2—订货方风险—在与PF相同的文件中约定)。
图10.5、在无故障(m=0)和由α=[1-3(1-PF)]n测定的订货方风险α=0.2条件下,视试验数量而定的初步可靠性水平
实物试验的实时可靠性评估
为了在发动机的任何试验阶段实物试验测定所达到的可靠性水平,利用故障的二项式分布[5,14],求出可靠性的上限和下限及其点估算。
可靠性的上限Pmax=1-q02,可靠性的下限Pmin=1-q01,可靠性的点估算PT=1-m/n,式中n—考核试验数量;m-在该试验数量下的故障数量。q01和q02由如下关系式求出:
式中α—制造厂的风险;β—订货方的风险。
示例。进行了50次试验,遭到了20次故障,成功通过了30次试验。测定了α=β=0.1的Pmax,Pmin,PT。根据计算得到:Pmax=0.7,Pmin=0.5,PT=0.6。在实践中常常遇到故障数等于零,即m=0的情形。那么,上限和下限的公式将具有\({{P}_{\max }}=\sqrt{1-\alpha },{{P}_{\min }}=\sqrt[n]{\beta }\)形式。对于无故障时的可靠性点估算来说,采用近似关系式
\({{P}_{T}}=1-\frac{1}{2\left( n+2 \right)}\)
在批生产过程中的可靠性检验
为了确认技术任务书的可靠性要求(无故障工作概率),按照规定程序进行检验批生产过程中的产品可靠性,这个程序出自于在制造厂条件下,产品可靠性的最可信数据是可用根据实物试验结果检验技术条件的要求得到的[28]。应使用发动机所有种类的实物试验结果:在试验台和产品使用过程中的抽查检验试验。制作好的发动机总数(不算报废的)中进行抽查检验试验的发动机总的相对数量,处于按照取决于制作好的发动机总数的相应比例率所采用的水平。在这种情况下,制作好的发动机总量从开始交付飞行试验算起。
所研究的检验程序也可用来评估在工厂和国家试验期间的产品可靠性。
所有实物试验分为在评估可靠性时会被考虑的考核试验和不会被考虑的非考核试验。
如果制作、装配和本身试验都是按照现行文件要求进行的,并测量(测定)了发动机所有必需的参数,试验就认为是考核试验。
考核试验分为两类:
1)成功考核试验-在该条件下硬件和参数状态都满足技术条件要求;
2)失败考核试验—失效,在该条件下硬件的状态,或者即使是其中一个参数不满足技术条件要求。
在评估可靠性时,只考虑考核试验,不管是成功的,还是失效(而且在评估可靠性时,不考虑在其之后对所有先前提供的产品进行修复的故障)。如果因为故障违反技术任务书的可靠性要求,那么,产品供货终止,并只有根据有关企业和订货方商定的决定方可恢复。
主导批生产的企业保障可靠性报告。每一个供货企业负责自己部件和零件的可靠性。同时,可靠性的要求由根据地面独立试验和飞行试验结果校准的所有现行技术文件来保障,这一切都由制作工艺稳定性、装配工艺稳定性、结构稳定性、材料性能稳定性来保障。
产品的可靠性用无故障工作概率表征PT3=1-q0,式中PT3—技术任务书中给定的可靠性(无故障工作概率)(例如,PT3≥0.999;q0—故障概率(频率)。根据试验结果的故障频率按照公式q0=m/n测定,式中m—故障数量;n—考核试验数量。
统计检验方法使有可能建立一个在试验时局限于上限值q01和下限q02值的故障频率允许值范围,该范围假定在指定范围内的产品可靠性与PT3值相一致。
如果故障频率q0位于允许值的范围之外,即q0<q02或q0>q01,那么,试验数据就与所规定的假定相矛盾。同时,如果q0<q02,产品的可靠性也与技术任务书相符,如果q0<q01,产品的可靠性就低于技术任务书所要求的。
在试验完善阶段大型SRM可靠性的评估特点
大型SRM具有两个特点[28]:1)由材料和生产高成本以及试验的一次性所决定的有限试验数量;2)尽管相对简单,大型SRM一般都具有多构件系统,即使是一个构件的结构变化都可能引起系统其它部分许多构件结构相应变化,因而,在试验完善过程中不断对全尺寸发动机进行结构更改。
由于成本高,允许进行极少量的试验,以便验证可靠性。因此,为了保障所需的抽查量,要求尽可能使用在试验完善所有阶段的所有现有信息。而且,仅根据定性特征评估可靠性,并采用二项式分布来评估和验证它,二项式分布仅研究两种试验结果可能性:或者是成功,或者是失败。
所有的点火试验都被分为考核和非考核试验。在评估可靠性时考虑考核试验,非考核试验在评估可靠性时不考虑。
参考文献书目
1、阿布拉莫维奇Г.Н.:紊流射流理论。莫斯科:国立物理数学书籍出版社,1960,715页。
2、阿弗希耶维奇Е.А.:工业技术中的激光。莫斯科:知识出版社,1978,63页。
3、阿列马索夫B.E.,德列加林А.Ф.,季申А.П.:火箭发动机理论/В.П.戈鲁什科编辑。莫斯科:机器制造出版社,1980,533页。
4、火箭空气动力学/Н.Ф. 克拉斯诺夫,В.Н.科舍沃伊,А.Н.达尼洛夫,З.Ф.扎哈尔琴科。莫斯科:高等教育出版社,1968,772页。
5、固体弹道导弹/А.М.希纽科夫,Л.И.沃尔科夫,А.И.利沃夫,А.М.希什凯维奇;А.М.希纽科夫编辑。莫斯科:苏联国防部军事出版社,1972,511页。
6、比尔格尔И.А.,绍尔Б.Ф.,约西列维奇Г.Б.:机器零件的强度计算。莫斯科:机器制造出版社,1979,702页。
7、布洛赫А.Г.:热交换辐射原理。莫斯科:国家动力科学技术出版社,1962,331页。
8、博尔加尔斯基А.В.,穆哈切夫Г.А.,舒金В.К.:热动力学和热传导。莫斯科:高等教育出版社,1975,495页。
9、博利舍夫Л.Н.,斯米尔诺夫Н.В.:数学统计表。莫斯科:科学出版社,1965,464页。
10、布劳温М.П.:钢合金化原理和某些试验数据。复合合金结构钢。基辅:科学思维出版社,1965,292页。
11、维尼茨基А.М:SRM。莫斯科:机器制造出版社,1973,347页。
12、维诺戈拉多夫Б.С.,沙伊特季诺夫З.Г.:喷射化学中性气体的推力矢量控制系统推力特性。喀山:高等学校通报。航空技术,1977,№3,23—29页。
13、碳含量对板状结构钢抗拉强度的影响/Б.А.德罗兹多夫斯基,Л.М.佩弗兹涅尔,А.С.塔拉托娃等。—金属学和金属热处理,1964,№5,21—28页。
14、沃尔科夫Е.Б.,苏达科夫Р.С.,瑟里钦Т.А.:火箭发动机可靠性原理。莫斯科:机器制造出版社,1974,339页。
15、气体动力学函数/Ю.Д.伊罗夫,Э.В.凯里,Е.Н.马斯洛夫等。莫斯科:机器制造出版社,1965,398页。
16、吉尔什费利代尔Д.Ж.,克尔季斯Ч.,别尔特Р.:气体和液体分子理论。莫斯科:外文书籍出版社,1961,929页。
17、戈鲁别夫И.Ф.:气体和气体混合物的粘性。莫斯科:国立物理数学书籍出版社,1959,375页。
18、加速度场中的SRM装药燃烧。—火箭技术问题,1974,№4,45-59页。
19、叶罗欣Б.Т.,利帕诺夫А.М.:SRM非稳态和准稳态工作状态。莫斯科:机器制造出版社,1977,200页。
20、扎鲁宾В.С.:飞行器结构中的温度场。莫斯科:机器制造出版社,1966,215页。
21、SRM研究。译自英文。M.萨梅尔费尔德编辑。莫斯科:外文书籍出版社,1963,440页。
22、坎特罗维奇З.Б.:化工机械和设备的计算原理。莫斯科:国立机械科技书籍出版社,1960,743页。
23、卡尔达绍夫Д.А.:合成胶。莫斯科:化学书籍出版社,1964,494页。
24、卡尔皮诺斯Д.М.,图钦斯基Л.И.,维什尼亚科夫Л.Р.:新的结构材料/Д.М.卡尔皮诺斯和А.Н.克鲁申斯基编辑。基辅:高等教育出版社,1977,312页。
25、卡尔索П.,叶格尔Д.К.:固体导热性,译自英文/A.A.波梅朗采夫教授编辑。莫斯科:科学出版社,1964,487页。
26、科特列尔К.Л.М.:对高强钢所提出的要求。—汇编:高强钢/译自英文。莫斯科:冶金出版社,1965,9—23页。
27、凯戈尔Ч.:胶接:译自英文。莫斯科:世界出版社,1971,293页。
28、克柳格尔П.:大型SRM结构的预先计算。—火箭技术问题,1965,№1,24—32页。
29、科罗廖夫В.И.:层状个相异性增强塑料板和壳体。莫斯科:机器制造出版社,1965,272页。
30、库尔金С.А.:在压力下工作的焊接薄壁容器强度。莫斯科:机器制造出版社,1976,184页。
31、库塔捷拉泽С.С.:热交换理论基础。莫斯科:原子能出版社,1979,415页。
32、拉季什科В.А.:材料的刚度和强度诊断。里加:知识出版社,1968,320页。
33、洛伊德Д.К.,利波夫М.:可靠性。组织、研究、方法、数学工具。莫斯科:苏联广播电台出版社,1964,686页。
34、马克-阿列维Р.Ф.,考恩П.Л.,萨梅尔费尔德М.:用热气体点燃复合固体推进剂的机理。—汇编:SRM研究。莫斯科:外文书籍出版社,1963,397—415页。
35、飞行器的发动机装置计算机设计/C.B.鲁缅采夫编辑。—科技成果。航空制造业系列,第4卷。莫斯科:全俄科技信息情报研究所,,1977,221页。
36、梅西金В.С.:合金钢炼制原理。莫斯科:冶金出版社,1964,684页。
37、米勒,巴林顿:现代内弹道特性计算方法。—火箭技术问题,1970,№1,44—63页,№2,52—65页。
38、穆加列夫В.П.:多孔表面紊流附面层的热交换和特性研究。—丛书:热传递和质量传递,第1卷。明斯克:科学和技术出版社,1968,32—37页。
39、穆加列夫В.П.:吹入气体对附面层影响的若干问题。汇编:紊流。莫斯科:科学出版社,1970,87—92页。
40、国外航空发动机制造业中的新东西,1969,№2,35—48页。
41、火箭技术装备中的新结构材料。—火箭技术问题,1974,№10,64—81页。
42、诺伊斯:火箭技术装备中有前景的烧蚀材料:译自英文。火箭技术问题,1974,№8,83—89页。
43、奥布拉佐夫И.Ф.,瓦西里耶夫В.В.,布纳科夫В.А.:复合材料回转壳体的优化增强。莫斯科:机器制造出版社,1977,144页。
44、奥尔洛夫Б.В.,马津戈Г.Ю.:SRM设计的热力学和弹道学基础。莫斯科:机器制造出版社,1979,391页。
45、航空和航天火箭技术装备中的热传递原理/B.C.阿弗杜耶夫斯基,Б.М.加里采斯基,Г.А.戈列博夫等;В.К.科什金编辑,莫斯科:机器制造出版社,1975,623页。
46、潘克拉托夫Б.М.,波列扎耶夫Ю.В.,鲁吉科А.К.:材料与气流的相互作用。莫斯科:机器制造出版社,1976,224页。
47、帕皮罗夫И.И.:铍—结构材料。莫斯科:机器制造出版社,1977,157页。
48、佩涅尔:气体的定量分子光谱学和辐射能力。莫斯科:外文书籍出版社,1969,493页。
49、彼得松 P.::应力集中系数。译自英文,莫斯科:世界出版社,1977,302页。
50、彼得罗娃А.Б.:耐热胶。莫斯科:化学书籍出版社,1977,200页。
51、结构塑料在飞行器生产中的应用/А.Л.阿比博夫,Б.В.博伊佐夫,Г.А.莫洛措夫,И.Ю.舍戴曼;А.Л.阿比博夫编辑。莫斯科:机器制造出版社,1971,190页。
52、拉祖梅耶夫В.Ф.,科瓦列夫Б.К.:固体弹道导弹设计基础。莫斯科:机器制造出版社,1976,356页。
53、赖兹别尔格Б.А.,叶罗欣Б.Т.,萨姆松К.П.:固体火箭系统中的工作过程理论基础/Б.А.赖兹别尔格编辑。莫斯科:机器制造出版社,1972,384页。
54、火箭发动机/M.巴列尔,A.若莫特,Б.Ф.维别克,Ж.范德克尔克霍维。莫斯科:国立国防科技图书出版社,1962,799页。
55、罗萨托Д.В.,格罗维К.С.:用玻璃纤维缠绕。译自英文。莫斯科:机器制造出版社,1969,310页。
56、萨梅费尔德М.,卡维尼Л.Х.,巴季斯塔Р.А.:考虑到非稳态热流的固体推进剂动态熄灭理论。译自英文。—国外航空发动机制造业中的新东西,1972,№4,34—44页。
57、国外合成胶。莫斯科:全苏航空材料研究所科技情报室,1964,21页。
58、碳基结构材料的性能。手册/В.Г.纳戈尔内,А.С.科托索诺夫,В.С.奥斯特罗夫斯基等。В.П.索谢多夫编辑。莫斯科:冶金出版社,1975,335页。
59、斯泰茨И.А.谢尔采尔Х.:在不同初步压力条件下通过卸压熄灭复合推进剂/译自英文,国外航空发动机制造业中的新东西,1972,№4,44—50页。
60、技术信息。中央空气流涕动力研究院,1975,№8,№18。
61、乌埃Р.П.:研制合金时的断裂韧性试验。—汇编,断裂韧性应用问题。莫斯科:世界出版社,1968,384—396页。
62、乌伊尔松Дж.У.,忠松У.О.,索姆托萨尼季Р.К.:带双弹性密封的喷管。译自英文。—火箭技术问题,1972,№1,42—57页。
63、沃克Р.Е.,绍尔М.:液体性能对用喷射液体方法的推力矢量 控制系统效率的影响。—火箭问题,1965,№4,36—48页。
64、战术导弹火箭发动机推力矢量控制。—火箭技术,1974,№11,50—68(90)页。
65、弗雷德里克斯,绍尔:在SRM气体射流中的材料试验。译自英文,火箭技术问题,1974,№8,100—104页。
66、采杰别尔格Н.Ф.:气体和液体的导热性。莫斯科:国立动力科学技术出版社,,1963。
67、什莱别尔М.Н.:研制新的技术装备和比热。莫斯科:知识出版社,1975,63页。
68、施特赫尔М.С.:火箭发动机推进剂和工质。莫斯科:机器制造出版社,1976,304页。
69、尤尔吉斯Г.:金属化合物。莫斯科:知识出版社,1975,64页。
70、亚欣斯基Ф.Г.:三层板的加热计算。—航空技术。喀山:高校通报,1962,№2,95—101页。
71、Aerospace Engineering. 1962. Vol. 21, N5.
72、Air Force Digest International. 1966. 2, p.5-11.
73、Black R. E. and others. The Crystal Ball Focuses on the Next Generation of Transport Aircraft. SAE Preprint, N710750.
74、Chen N.H. Simplified Solution for Ablation in a Finite Slab.—AIAA Journal. Vol. 3, N6, June, 1965.
75、Composites. 1973, 4, N1, p. 34-38.
76、Day E.E., Baily L.G. AIAA Paper, N71—751, AIAA/SAE. 7-th Propulsion Joint Specialist Conf., June 14-18, 1971.
77、Des. Eng. (Gr. Brit). 1972. Nov, p. 48-50.
78、Eatough R. G. TRW Systems. AIAA Paper, N71-752, AIAA Joint Propulsion Specialist Conf., June 14-18, 1971.
79、Giles G. L., Blackburn C. L. and Dixon S. C. Automated Procedures for Sizing Aerospase Vehicle Structures (SAVES).—Journal of Aircraft. 1972, XII.
80、Interavia. 1972, 28, N6, p.654-656.
81、Journal of Spacecraft and Rockets. N5, May, 1969, p. 577-582.
82、Miller W. H. Measurement of Solid Rocket Motor Thermally Induced Radial Bond Stresses. —Journal Spacecraft, Nov., 1969, p. 1253-1258.
83、Nixdorf I. Hochtemperatur—Werkstoffein der Raumfahrt. —Luftfahrtechnik—Raumfahrtechnik. 1968, Bd4, N1, s. 7-12.
84、Russel A., Ellis. A step toward Automation of Nozzle Design. —AIAA Paper. AIAA Aerospace Computer System Conf., N69-975, September 8-10, 1969.
85、Sauegh G., Moy P. Utilisation laser de haute purssanu dans le travail des metaux. —Saudage et techn Connexes. 1977, 31, N5-6, p. 193—206.
86、Taback H. J. and others. Combustion Termination of Solid Rocked Motors.—Journal Spacecraft. 1965, V-V1, vol. 2, N3, p. 332—336.
87、Ward J. C. AIAA Paper N70—1386, AIAA 2nd Sounding Rocket Technology Conf., December 7—9, 1970.
索引已更改