大型固体火箭发动机柔性摆动喷管研究综述
摆动喷管是提升大型固体火箭发动机性能的关键技术,目前国外大型固发大部分使用柔性摆动喷管作为发动机喷管方案,但我国前期在此方面研究较少。目前,随着我国大型固体火箭发动机技术的不断发展,亟需研制能与之适配的大型摆动喷管。本文选取了国外具有代表性的大型固体火箭发动机,包括航天飞机助推器(ASRM)、Arian-5助推器(MPS)、VEGA火箭一级发动机(P80)、H-ll火箭助推器(SRB)等,对其柔性摆动喷管的研究进展和主要性能指标进行介绍、概括,辨析了大型柔性摆动喷管的研制关键技术,梳理出了大型柔性摆动喷管的研制流程及关键点,以期为我国大型高性能柔性摆动喷管的研制提供参考依据。
1 引言
立足于现代固体推进技术的大型固体火箭发动机具有推力大、结构简单、可靠性高、响应速度快、研制周期短等优点,作为重型运载火箭助推器、中、大型运载器芯级以及小型运载火箭主动力系统得到了广泛的应用。为了得到足够的控制力矩,大型固体火箭发动机应选择全轴摆动单喷管【1】。
柔性摆动喷管是当前应用最为广泛的摆动喷管类型【2】,其通过柔性接头将喷管固定体部分与活动体部分进行连接,具有结构可靠性高、重量轻、摆动性能稳定、固有频率高、响应速度快等特点。国外大型固体火箭发动机普遍使用大型全轴柔性摆动喷管(通常喉径大于300mm)实现推力矢量控制能力。本文通过对国外主要大型柔性摆动喷管的研究进展和主要性能指标进行分析,梳理出了大型柔性摆动喷管研制过程中的关键技术,以期为我国的大型高性能柔性摆动喷管的研制工作提供参考依据。
2 柔性摆动喷管的发展及分类
柔性摆动喷管是一种使用柔性接头作为活动部件的全轴摆动喷管:美国于1964年左右首先在该领域开展研究工作,1968年John Herbert 申请了柔性接头专利 【3】,Robert Woodberry 在上世纪70 年代开展了一系列试验并设计了一种橡胶/金属柔性接头用于全轴摆动喷管【4】,Walker 等人根据试验数据推导出了可实际应用于柔性接头设计的工程经验公式【2】;法国在该领域的研究稍晚于美国,于1968年启动了柔性摆动喷管的研究、设计工作,并于1970年成功完成了首台点火试验【5】。此后,世界各国开始广泛开展关于柔性摆动喷管的相关试验及研究工作。
柔性摆动喷管根据分类方法的不同可以分为多种形式:
a)根据柔性接头摆动中心相对于喷管喉部的轴向位置关系可将其分为前摆心摆动喷管、后摆心摆动喷管(见下图1/2);根据柔性接头的数量可将其分类为单接头摆动喷管及双接头摆动喷管(见下图3)【6】。
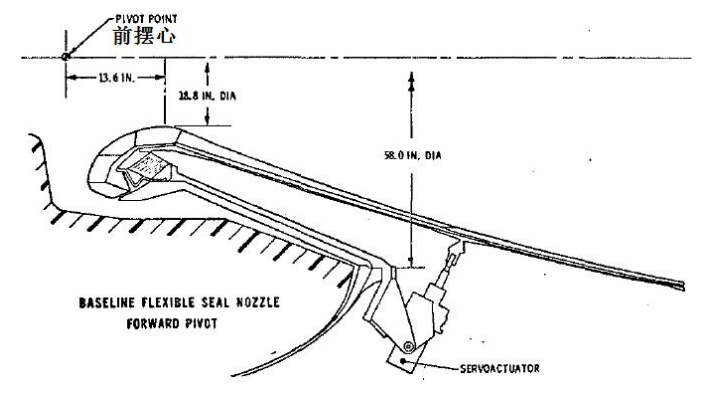
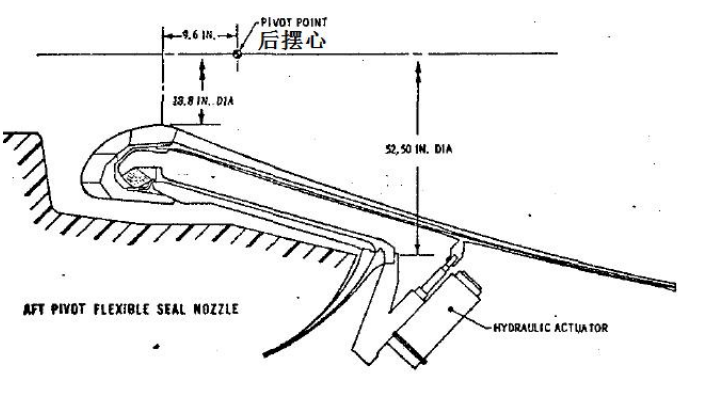
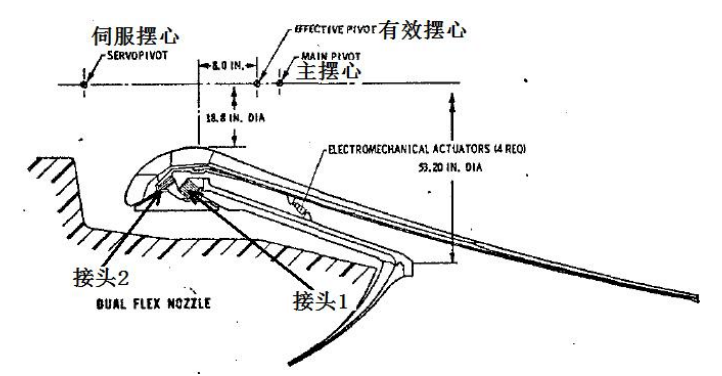
b)根据活动体分离线的位置,可将柔性摆动喷管分为亚音速分离线摆动喷管及超音速分离线摆动喷管,超音速分离线摆动喷管将活动体与固定体的分离线放置在喷管扩散段上游,收敛段及喉部为固定不进行摆动。1997年RAEllis和M.Berdoyes等人为了解决使用潜入式摆动喷管带来的发动机比冲损失问题,同时为了进一步提高发动机装填比,设计并测试了一种超音速分离线柔性摆动喷管,获得成功。随后两人还以Orbus1传统柔性摆动喷管为基础设计了一种超音速分离线摆动喷管,两种喷管的对比见下图4【7】。
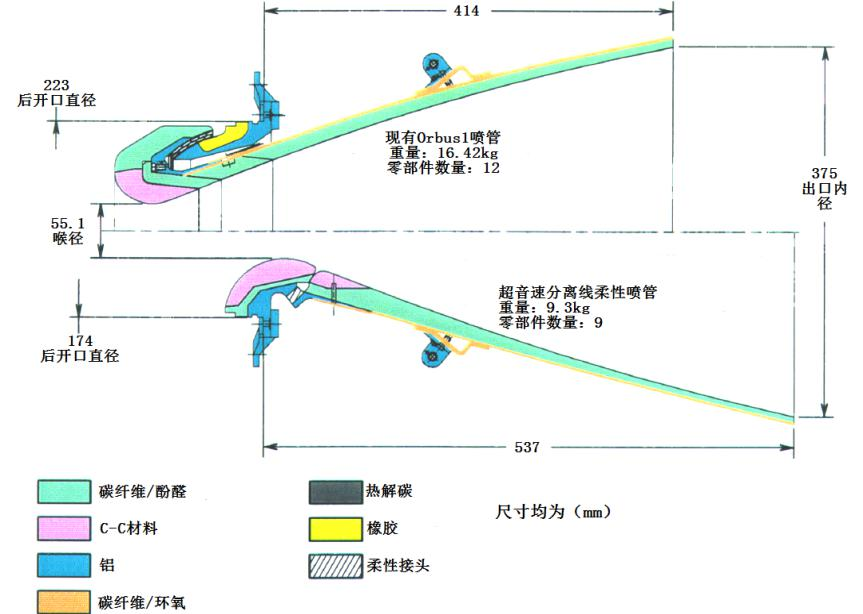
鉴于以上不同的分类方法,摆动喷管结构类型可有多种组合形式。在实际设计时可根据全箭(弹)控制力矩要求、发动机总体设计要求、伺服机构大小/功率限制及摆动包络等设计输入来合理选择摆动喷管类型。总体而言,柔性摆动喷管的设计目标是:选择合适的结构类型及材料方案,在满足各项输入指标、可靠性及成本要求的前提下提供较好的摆动弹性刚度及较小的结构重量【4】。
3 大型柔性摆动喷管技术发展
尺寸均为(mm)橡胶W柔性接头
柔性摆动喷管经过50年的发展,已被广泛应用于各种航天飞行器和运载工具的固体火箭发动机上:
a)作为大型运载工具的第一级,其推力在起飞推力中占了很大比例,如在航天飞机、大力神-4B、阿里安-5(欧洲)、H-IIA(日本)、GSLV.MKIII(印度)起飞推力中分别占到82%、100%、93%、80%、100%;在液体芯级周围并联捆绑具有柔性摆动喷管的固体发动机,可以有效地提高运载工具的性能。
b)作为固体运载火箭的主推力,如欧空局的VEGA,美国发展的飞马座(PEGASUS)、金牛座(TAULUS-1/2),俄罗斯的起点号(START),日本的M-5、爱普西龙(Epsilon),巴西的VLM-1运载器等。均使用柔性摆动喷管方案固体火箭发动机【1,8】。
本文选择具有代表性的几种大型柔性摆动喷管对其总体设计、材料方案、柔性接头及作动器类型进行介绍,其基本参数见表1:
表1 国外大型柔性摆动喷管基本参数表
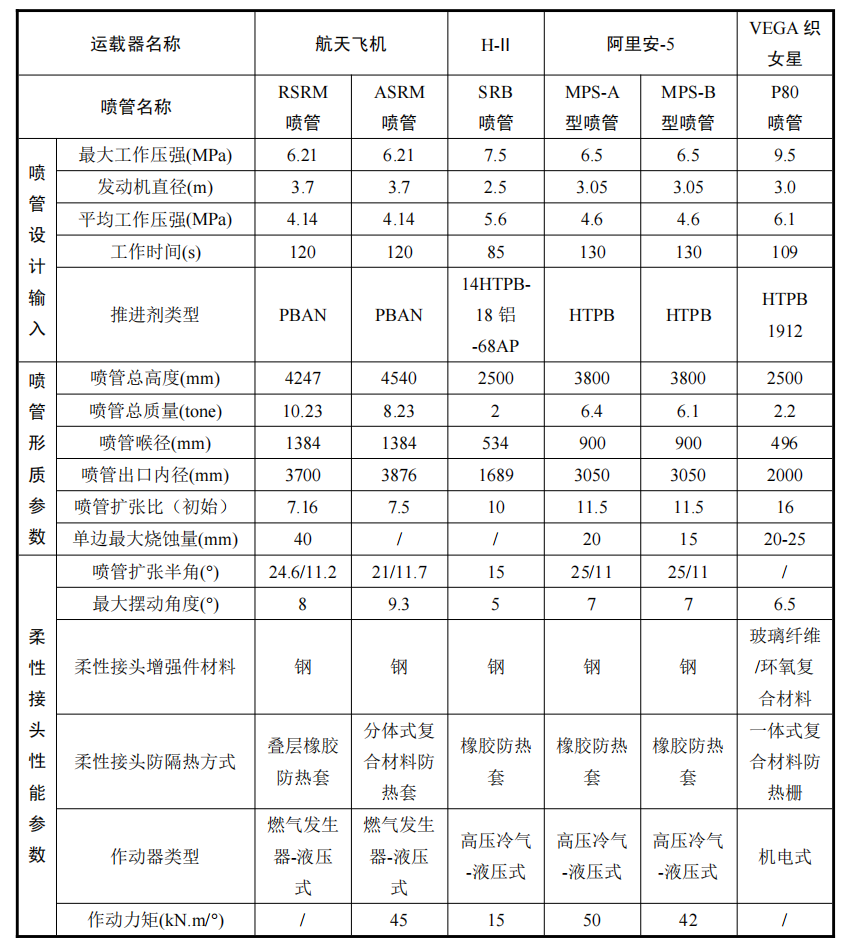
3.1 航天飞机助推器柔性摆动喷管
航天飞机固体火箭发动机(SRM)喷管是大型柔性摆动喷管的代表型号,其主要分为HPM(1985 年挑战者事故前)、RSRM(1986年重新设计)及ASRM(1992年升级改进型)3个阶段。其设计、分析和测试均由位于美国犹他州的 Morton Thiokol公司主导,并在NASA马歇尔空间飞行中心的管理下完成【9】。其结构形式为潜入式后摆心柔性摆动喷管,使用一套较为复杂的燃气发生器-液压式伺服作动器作为推力矢量控制机构【10】
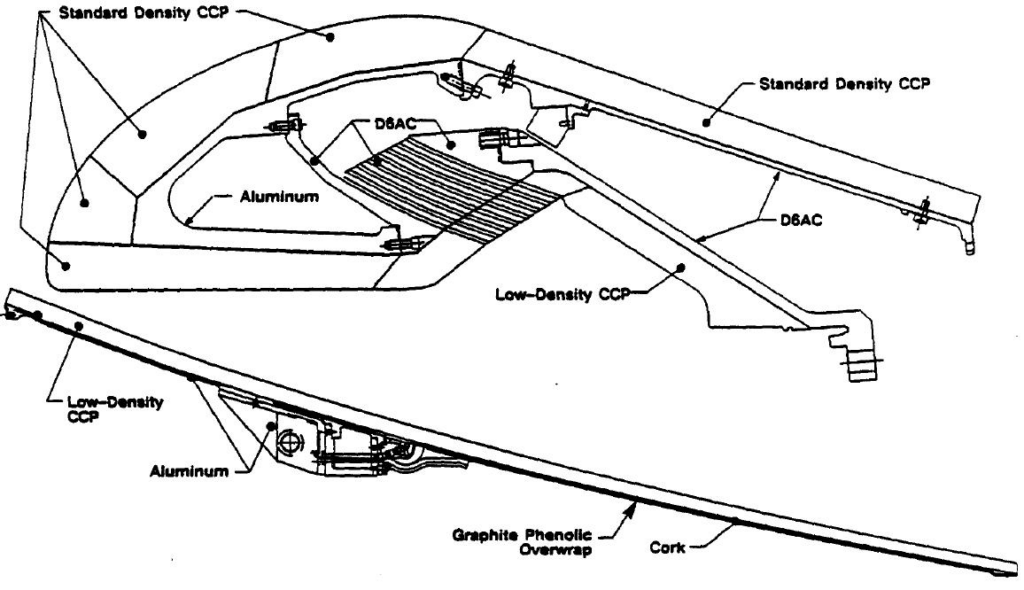
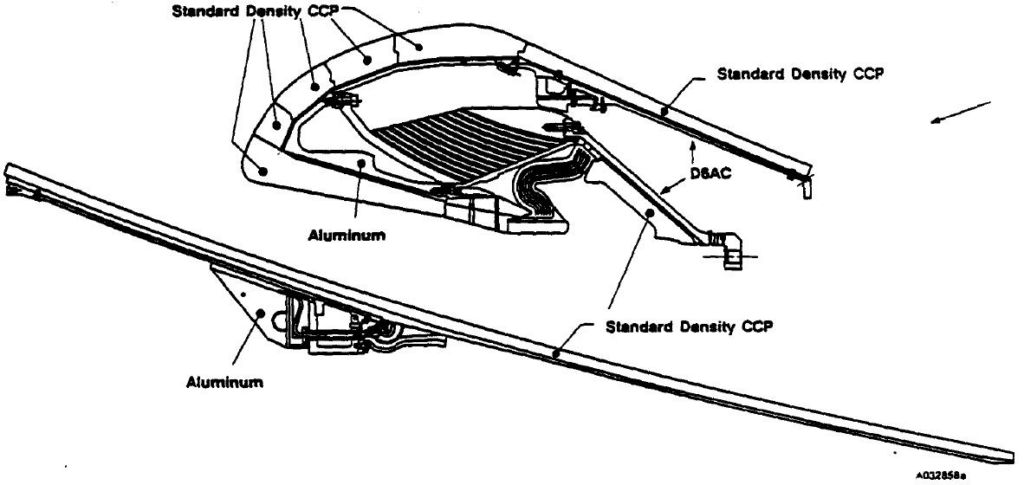
ASRM喷管是1992年为了进一步提高航天飞机固发喷管的性能、可靠性和安全性,在1986年设计的RSRM喷管基础上进行改进设计而来【11】。图5和图6分别为RSRM喷管与ASRM喷管结构简图,相较于以提高安全性能为主要目的而进行改进设计的RSRM喷管,ASRM喷管最显著的改变在以下两个方面:
a)减少了零件总数量,主要包括完全取消了喉部区域的一个压力密封连接接头(如下图7所示)及减少了其它喉部零件数量,从而进一步降低密封件失效的可能。ASRM喷管各部件的材料使用方案为:收敛段、喉部和扩散段绝热层小端绝热层使用标准密度碳布/酚醛树脂材料(1.45g/cm3);收敛段和喉部绝热层由3块部件组装而成(相比 RSRM的4块减少1块);扩散段绝热层大端(扩张比2.5以后)以及固定倒锥体绝热层使用低密度碳布/酚醛树脂材料(1.0g/cm3);扩散段后端壳体结构层使用碳/酚醛树脂结构件;喉部及前鼻端支撑为整体式铝制件。以上的一系列改进,可使喷管整体减重363kg。【12】
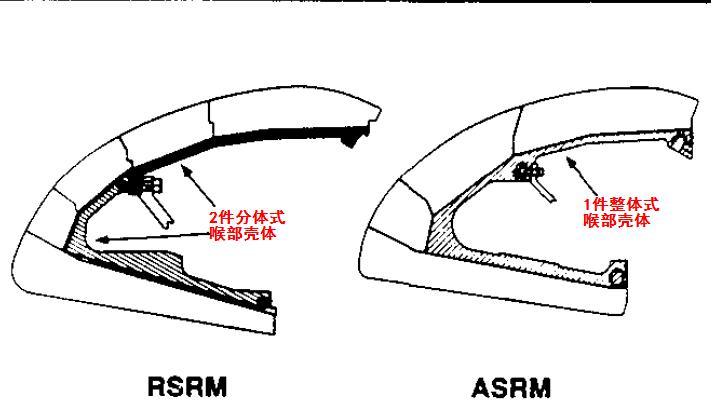
b)ASRM喷管另一重要改进是对柔性接头进行了重新设计,新喷管的柔性接头由8层天然橡胶弹性件和7层钢制增强片构成,同时新的柔性接头改用7层碳布/酚醛树脂材料与8层低模量丁异戊橡胶组成复合隔热套【11】。该项改进可使柔性接头减重1630kg以上。在ASRM喷管设计之前,这种复合材料隔热套技术路线就在很多喷气飞机发动机上得到了充分验证,被认为不管从生产工艺性还是减重上都比RSRM喷管使用的叠层防热套方案更有优势【13】。
ASRM喷管项目基于当时的材料与技术水平,通过简化的设计流程及健壮性设计【14】,满足了NASA所提出的生产工艺性、一致性及安全性要求。代表了当时大型摆动喷管设计的先进水平。
3.2 日本H-Ⅱ固体火箭助推器喷管
日本于1985开始启动H-II固体火箭助推器(SRB)的研制工作【15】,该型号固体火箭发动机由日本国家空间发展部负责研制与开发。每枚H-Ⅱ火箭在芯一级的两侧捆绑2枚SRB助推器,助推器直径1.8m,高23.4m,重量约为70吨,可提供约1560kN的海平面推力。该型发动机于1992完成了地面静止点火试验测试,获得成功。
日本的柔性摆动喷管技术自上世纪80年代开始发展【16】,SRB助推器使用潜入式后摆心柔性摆动喷管技术方案,其具体结构及材料方案见下图8。该喷管的活动部件是由多个金属壳体拼接而成,在金属壳体内侧使用了石墨喉衬以及碳纤维或石英纤维/酚醛树脂防隔热材料构成的内烧蚀、防热层进行保护。该型喷管的防隔热层安全系数为1.5。
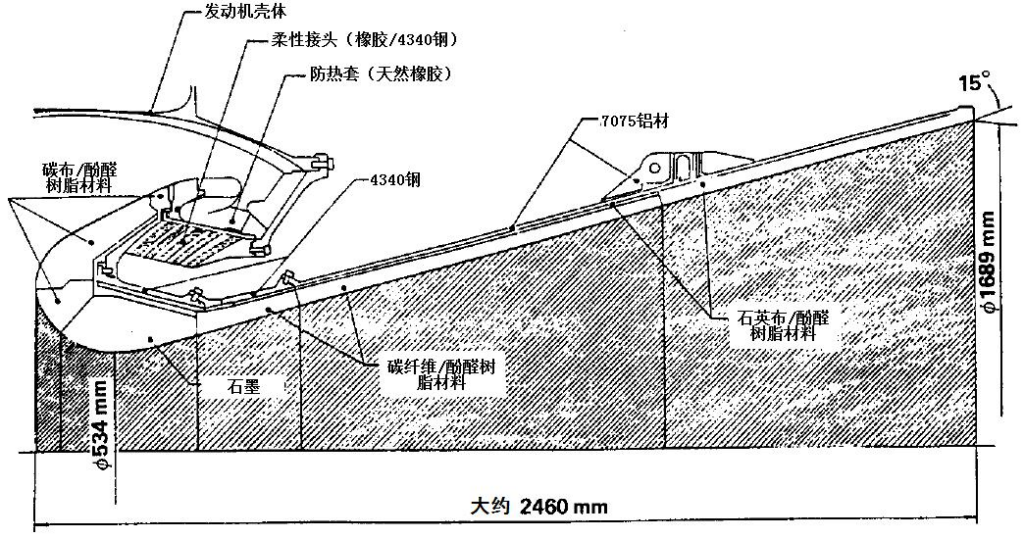
每台SRB固体火箭助推器喷管使用2个电液伺服作动器提供喷管摆动所需的力矩。为了尽可能的节约开发和制造成本,该型电液作动器直接由高压冷气来驱动液压元件,最大可提供120KN的执行力,下图9为其在喷管上的安装示意图 【17】。
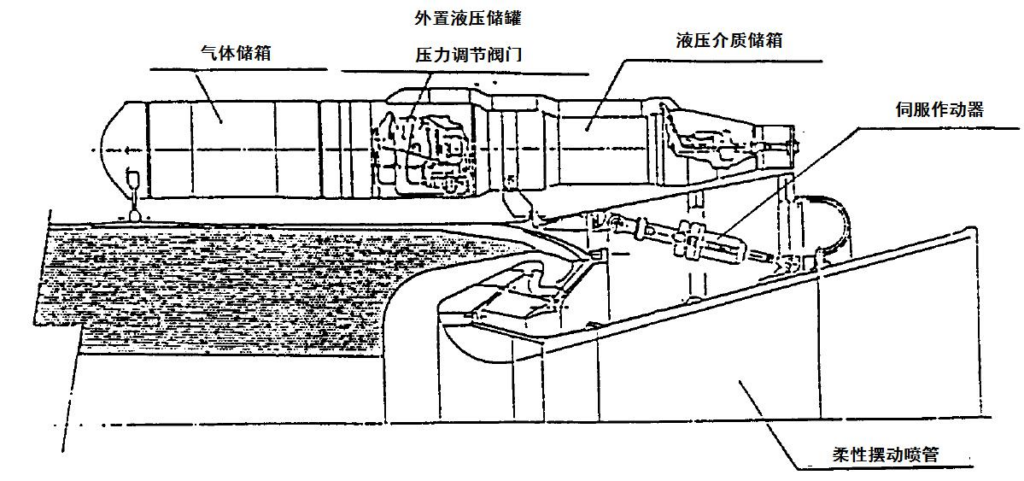
SRB喷管作为亚洲国家研制较大型固体火箭发动机柔性摆动喷管,在整体方案设计及伺服作动器选择上均有一定的借鉴意义。
3.3 阿里安-5固体火箭发动机喷管
欧洲的阿里安-5(Arian-5)运载器使用了两个捆绑式MPS(Moteur a Propergol Solide)固体火箭发动机,与芯级发动机并联提供约90%左右的火箭起飞推力,其同样使用柔性摆动喷管来实现发动机推力矢量控制。MPS柔性摆动喷管的研制历程主要分为两个阶段,早期型(A型)喷管由Snecma Moteurs 公司于1995年中期完成开发,并随着Arian-5火箭成功执行了至少20次发射任务。随着技术及材料工艺的发展,改进型(B型)喷管于2001年9月完成了开发及试验工作。两型喷管的制造商均为Snecma公司固体推进分部。
图10为A型喷管的结构示意图,为典型的潜入式后摆心柔性摆动喷管,一套由高压氦气罐作为动力单元及两个液压伺服作动器组成的推力失量控制系统使喷管产生可控摆动【181,该喷管的整体技术和材料方案与法国上世纪70-80年代研制的M4海基弹道导弹发动机喷管有较强的关联性。该型喷管在研制过程中总共进行了8次地面点火,并获得了至少28台以上的订单。喷管各部件的材料方案可以归纳为以下3类:
a)喷管的机械功能:结构稳定性和摆动功能是由金属结构件及柔性接头提供;
b)喷管的抗高温燃气烧蚀及防/隔热性能:是由C-C复合材料喉部组件及酚醛基树脂绝热层提供。柔性接头的保护是由一个硅橡胶保护套提供,保护套自身被一个酚醛基防护罩所保护;
c)喷管的外防热(主要用于防止其它一级发动机工作时产生的热辐射及热对流对喷管造成影响)性能:是由轻质的绝热材料如硅橡胶或软质酚醛基材料提供。
MPS柔性摆动喷管在两台液压伺服作动器的推动下可以实现最大7°的摆角,其摆动力矩为50KN.m/°,在扩散段壳体后段设计了加强环提供足够的强度用以安装伺服机构接口。
图 10 MPS-A 型喷管结构示意图及实物图
MPS-B型喷管是在A型喷管的基础上进行了重新设计,图11为A/B型喷管结构对比图,B型喷管的变化主要集中在:1)将喷管扩散段绝热层由3分段变为2分段结构,同时优化了绝热层厚度;将固定壳体的热防护层部件数量由分体式设计为一体式,并对气动外形进行了优化设计从而减少了部件制造成本;2)将活动倒锥体/柔性接头保护罩部分零件减少为2个;喉部分段数量减少至2段;3)零件数量的减少也导致了连接接头数量的减少。如此一系列改进措施再结合对零部件厚度尺寸上的优化,整个喷管相比于A型减轻了大约300kg(参数对比见表1),B型喷管的总重为6100kg。
以上一系列的改进使得喷管的主要部件数量由A型的20降低至B型的13件,可显著提高生产制造效率,而且由于B型喷管使用了诸多低成本材料及更先进的制造技术,进一步降低了成本,提高了喷管性能,这样多效并举可有效提高后续喷管订单数量。
MPS-B型喷管在未来还会吸收VEGA固体火箭一级P80发动机喷管的多项先进技术,从而演化为MPS-2型固体火箭发动机喷管用于后续阿里安-6型火箭的发射任务。
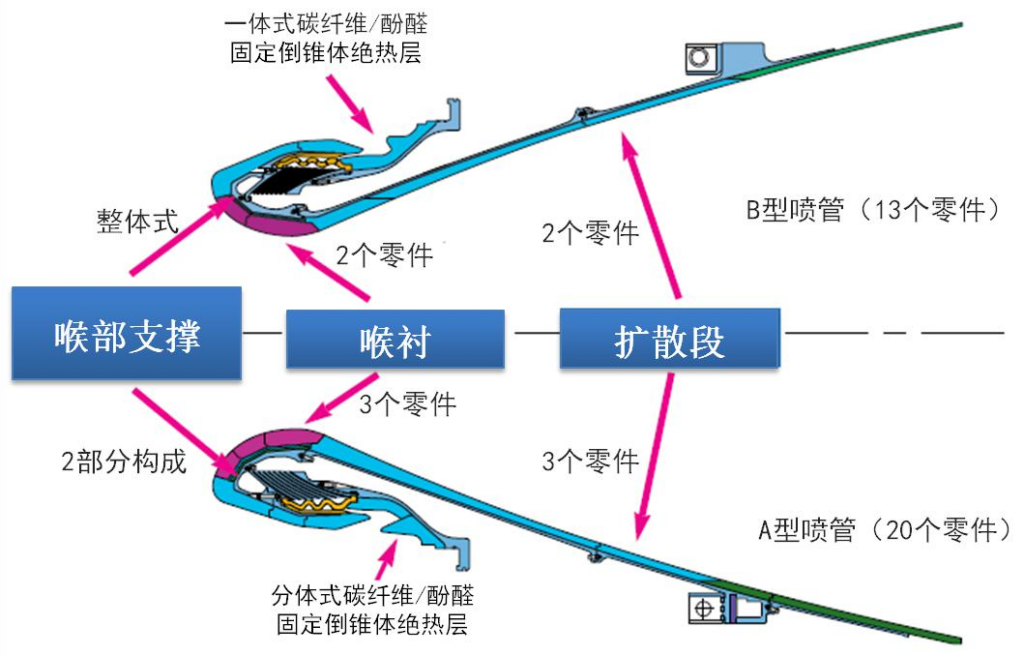
3.4 织女星固体火箭一级发动机P80喷管
欧洲织女星火箭是快速进入空间的中小型运载火箭,成本低,适用于欧洲卫星快速发射。其一级P80发动机综合集成了多项固体推进先进技术,技术水平处于世界领先水平【19】。该发动机柔性摆动喷管采用了诸多先进、低成本技术,其主要由法国Snecma公司固体推进分部负责开发及制造,于2003年初开始研制,2006年9月随P80发动机完成首台点火试车(喷管及试车照片见下图12),并于2012年2月13日在圭亚那库鲁航天中心随织女星(VEGA)火箭成功完成首飞【20】。
图12 P80开发阶段首台喷管及开发阶段首次发动机试车照片(2006-09)
P80发动机柔性摆动喷管同样采用了较为常见的潜入式后摆心形式(下图13)。该型喷管主要围绕两个目标开展研制工作:1)开发一种适用适用于织女星小型固体运载器的一级发动机喷管;2)为后续如阿里安-6使用的更大型固体火箭发动机喷管验证低成本、先进性技术 【21】。
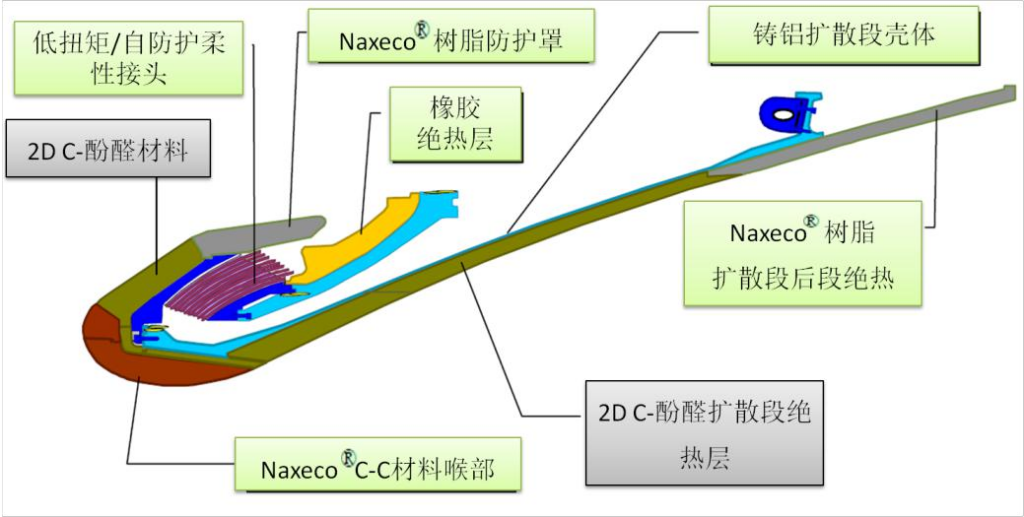
因此P80喷管在研制、设计过程中大量采用CFD/CAE手段对流场、烧蚀、工艺等进行了全面系统性仿真;并大量的使用低成本新技术,主要可总结归纳为以下几个方面 【20】:
a)防隔热功能:使用优化的低成本材料,如增强橡胶材料,新型Naxeco°树脂碳/酚醛树脂材料,常规玻璃钢/环氧基树脂材料,这些材料根据不同零件的需求按需选择;
b)机械性能:研发了新型低扭矩/自防护柔性接头,可以降低摆动喷管伺服机构的尺寸及功率,因此可以使用成本及技术难度更低的机电式伺服作动器,同时的大型铸铝扩散段壳体也被应用于喷管结构件;
c)内弹道性能:研发并使用了一种新型的低成本喉衬C-C复合材料。
以上新型喷管技术为后续更为先进、尺寸更大的柔性摆动喷管验证了技术方案可行性,为后续柔性摆动喷管的发展指明了方向。其中以下两项技术被认为是P80喷管最具有创新性的突破:
3.4.1 P80喷管低扭自防护柔性接头
下图14/15为P80的高性能柔性接头照片,该项成果被认为是P80喷管最为重要的创新点。其通过使用低剪切模量合成橡胶和复合材料增强件技术,为法国下一代柔性接头的发展指明了道路。较之前降低了40%剪切模量的橡胶件被试验证明可以使得柔性接头的摆动力矩降低同样的水平。当然,寻求降低柔性接头的摆动力矩自身并不能降低喷管制造成本,但这对喷管伺服机构来说却是极有意义的改变。这是因为摆喷伺服机构的输出力与柔性接头摆动力矩完全成正比关系,因此摆动力矩的降低会使得伺服机构的功率、尺寸及价格均得到降低。此外,更小的摆动力矩使得 P80 喷管可以使用比利时SABCA公司提供的机电式伺服作动器(EMA)以及相应的供电及控制单元(IPDU)。这项技术为简化大型固体火箭发动机的结构及发射准备流程提供了更大的可能。【20】

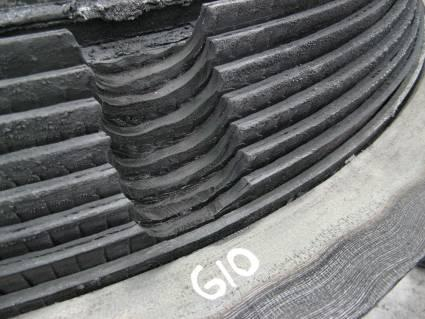
3.4.2 结构性Naxeco③/树脂绝热层材料
法国的碳纤维/酚醛防隔热部件在相当长的时间内都是用粘胶基碳纤维/酚醛树脂预浸料布带,使用半自动化的缠绕工艺制作而成。这种材料虽然拥有较好的抗烧蚀性能,但是在制造时需要专门的模具及缠绕设备,最终导致了其制造成本较高。因此在P80喷管上使用了新型结构性Naxeco*树脂绝热层材料。
表2简单列出了传统材料体系及工艺与Naxeco 9树脂防热材料的生产流程对比。对比可知,新材料的主要优点在于:1)通过3D针刺工艺使得材料具有优异的热-力学性能。这种纤维排布方式可有效防止制造过程中的分层现象从而提高零件制造过程中的保形能力,使得传统工艺中的金属支撑模具得以被取消;2)使用普通PAN基碳纤维降低材料成本,同时通过使用树脂传递模塑成型(RTM)工艺,消除了布带浸渍、储存和缠绕工艺所带来的一系列问题。【20】
表2 传统防热材料与结构性 Naxeco⑧/树脂防热材料工艺流程对比
4 大型柔性摆动喷管发展趋势总结
总结世界各航天强国的柔性摆动喷管研制历程,可确定大型潜入式后摆心柔性摆动喷管是目前大型固体火箭发动机喷管的主要发展方向。并且随着设计手段和材料水平的不断进步,世界各国柔
性摆动喷管技术目前仍在高速发展阶段。对国外大型摆动喷管技术发展趋势进行分析,其重点发展方向如下:
(1)先进大型摆动喷管总体设计技术
随着未来太空活动需求日益增长以及有效载荷质量不断增加,固体火箭发动机的尺寸及工作压强也在逐渐提高,以获得更大的推力及更好的能量发挥特性。因此,为了适应固体火箭发动机的发展,未来柔性摆动喷管将不断向大型化、高性能、低成本方向发展。这就需要在大型摆动喷管总体设计时使用更加先进的CFD、CAE分析手段,充分利用材料性能特点,不断优化结构布局,提高喷管及发动机性能。
图16是基于P80喷管技术设计的MPS2型发动机P2010喷管概念图,该型喷管是未来阿里安-6 运载器计划的一部分。表3为P2010喷管与现役阿里安-5助推器MPS-B型喷管的基本参数对比,新喷管在简化设计、减重及降低伺服功率上都比现有喷管有了较大改进。
从法国 MPS、P80、P2010系列喷管的发展趋势看,未来大型摆动喷管在设计上将进一步通过减少喷管轴向分段,设计新型自防护柔性接头等手段从而达到减少主要零部件数量、降低伺服作动器功率等目的。这样一方面避免了由于连接密封失效而导致发射失败的事故再次发生,另一方面在降低喷管成本的同时可以提高生产工艺性及生产效率,满足后续可预期的高密度发射需求。
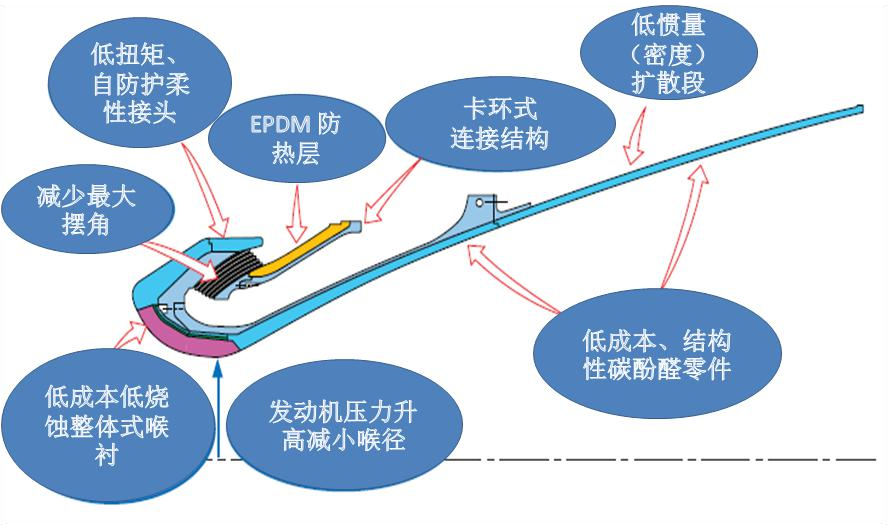
表3 P2010 喷管与 MPS-B型喷管主要技术指标对比
(2)低扭矩复合材料增强件柔性接头技术
新型柔性接头在 P80 喷管上的验证成功,为后续高性能柔性接头的研制指明了方向。不管在设计上还是制造工艺上,柔性接头的优化目标都是在向降低摆动力矩,整体质量及包络尺寸最小化,防热技术简单可靠,提高摆动稳定性及响应性发展。如下图 17/18 所示,柔性接头以上优化使得作动器类型由较复杂的液压式向机电式转变,可以极大的降低 TVC 系统复杂程度,减少运载器发射准备时间。
图 17 气动-液压式伺服控制系统组成
图 18 机电式伺服控制系统组成
(3)先进轻量化、耐烧蚀、低成本复合材料技术
随着固体火箭发送机总体质量比要求不断提高,最大烧蚀率要求不断降低,需通过1)使用新型的低成本纤维编织与自动化铺放技术(如图19所示的纤维预制体自动化缠绕及针刺技术),以及工艺匹配性好、热-力学性能优异的新型抗烧蚀树脂,从而降低生产成本,提高喷管生产效率;2)适合规模化、批量化生产的固化成型技术(如图20所示的RTM技术),来提高烧蚀/绝热层材料质量一致性,提高喷管整体可靠性。
图 19 Naxeco®喉衬预制体自动化针刺过程
图 20 使用 RTM 工艺生产的喷管扩散段
5 结束语
通过上文分析可知,在未来的航天发射中,使用潜入式后摆心柔性摆动喷管的中大型固体火箭发动机仍是主流发展趋势。国外航天强国的大型柔性摆动喷管经过近50年的发展后仍在持续更新迭代,目前正朝着低成本、高可靠、作动力矩小和可重复使用等方向不断发展,我国在该领域的发展已相对滞后。
但是随着近年来我国商业航天产业的蓬勃发展,以及固体火箭发动机技术的不断进步,均为大型柔性摆动喷管的发展带来了良好的机遇。建议后续:1)我国应密切跟踪国外大型柔性摆动喷管技术发展路线,根据我国的设计水平、材料水平确定符合我国情的大型柔性摆动喷管发展规划,加紧追赶国际领先水平;2)整合大型柔性摆动喷管开发过程中的上下游产业,加强国内柔性喷管研制领域的优势单位的合作,为国家级决策提供支持;3)随着近年我国大型固体发动机技术的发展,应以此为牵引尽快启动与之适应的大型柔性摆动喷管预先研究工作,尽早突破大型先进柔性摆动喷管低扭矩自防护柔性接头、大功率伺服作动器、低成本高性能耐烧蚀/防隔热材料等关键技术,从而提升大型固体发动机整体性能。
参考文献
[1] 阮崇智,”大型固体火箭发动机研制的关键技术,”固体火箭技术,卷 28,编号1,pp.23-28,2005.
[2] E.K.A,B.M.V and C.M.R,”Effect of Shim Percentage on Non-Linear Static Behavior of Flex Seal of Rocket Nozzle,” in 4th International Conference on Materials Processing and Characterization,2015.
[3] J.Herbert,Redlands,F.J.Kovitch and M.McCorkle,”Flexible Joint Means”. USA Patent 3,390,899,2 July 1968. [4] R.F.Woodberry,”Flexible Joints For Thrust Vector Controls,” in AIAA/SAE 1lth Propulsion Conference, Anaheim,CA,1975.
[5] M.Berdoyes,”The French Deterrent Force SRMs:Genesis of Flexseals,” in 44th AIAA/ASME/SAE/ASEE Joint Propulsion Conference & Exhibit,21-23 July,2008.
[6] J. W. Wilson, W. O. Johnson and P. C. Sottosanti, “Dual flex– A low horsepower flexible seal nozzle,” in AIAA/SAE 7th Propulsion Jint Specialist Conference,Salt Lake City,UT,June,1971.
[7] R.A.Ellis and M.Berdoyes,”Supersonic Splitline(SSSL)Flexible Nozzle Technology Evaluation Program,” American Institute of Aeronautics and Astronautics,1997.
[8] T. Wekerle,”Brazilian Thrust Vector Control SystemDevelopment: Status and Trends,”in 52nd AIAA/SAE/ASEE Joint Propulsion Conference,2016.
[9] A.R.Canfield,E.E.Anderson and G.E.Nichols,”Space Shuttle Nozzle Development,” in AIAA/SAE 14th Joint Propulsion Conference,Las Vegas,Nev,July 25-27,1978.
[10] J. R. Cowan and W. N. Myers,”Design and Testof a High Power Electromechanical Actuator for Thurst Vector Control,” in AIAA/SAE/ASME/ASEE 28th Joint Propulsion Conference and Exhibit,Nashville,TN,Jujy 6-8, 1992.
[11] 刘勇琼,”先进固体火箭发动机的喷管研制,”固体火箭技术,卷 4,编号 12,pp.26-28,1992.
[12] W.J.Kearney and J.D.Moss,”ADVANCED SOLIDROCKET MOTOR NOZZLE DEVELOPMENT STATUS,” in AIAA/SAE/ASME/ASEE 29th Joint Propulsion Conference and Exhibit, Monterey, CA, June 28-30, 1993.
[13] J. W. Edwards,”ASRM Nozzle Design and Development,” in AIAA/SAE/ASME 27th Joint Propulsion Conference,Sacramento,CA,1991.
[14] R. E. Mitchell,”The Advanced Solid Rocket Motor,”in AIAA Space Programs and Technologies Conference,March 24-27,1992.
[15] T.Fujita,Y.Fukushima and M.Nagatomo,”H-II Solid Rocket Booster Design and Development,” in AIAA Space programs and Technologies Conference,Huntsville,AL,March 24-27,1992.
[16] H.Inohara,T.Fujiwara and T.Murakami,”Development of Movable Nozzle for Solid Rocket Motor,” in AIAA, 1983. [17] E. Ishibashi, S. Okaya and T. Endo, “H-II Solid Rocket Booster Thrust Vector Control System,” in 3lst AIAA/ASME/SAE/ASEE Joint Propulsion Conference and Exhibit, San Diego, CA, June 10-12,1995.
[18] P. Caye and D. Descamps,”ARIANE 5 Thrust Vector Control Development Status,” in 30th AIAA/ASME/SAE/ASEE Joint Propolsion Conference,Indianapolis,IN,June 27-29,1994.
[19] 徐丹丹、王健英、闫大庆,“织女星火箭固体发动机喷管技术研究,”推进技术,编号 8,pp.64-70,2016.
[20] B.D,G.E and D.M,”P80 Nozzle Development& Qualification Synthesis,” in 44th AIAA/ASME/SAE/ASEE, Hartford,CT,2008.
[21] E. Gautronneau, C. Cros, P. Pascal and M. Cutroni, “Vega program – The P80 FW SRM nozzle,” in 40th AIAA/ASME/SAE/ASEE Joint Propulsion Conference and Exhibit, 11 – 14 July, 2004
本文选自:周子翔等的会议论文